Фотоотчет: Ремонт двигателя мотоцикла «ИЖ-Планета» 2, 3, 4 и пятой модели. Ремонт двигателя мотоцикла
Капитальный ремонт двигателя мотоцикла в Москве | Чистка и синхронизация карбюраторов мотоцикла
Надежный ремонт двигателя мотоцикла в Москве в мотосервисе “HARD DAMAGE”!
Мотор является сердцем мотоцикла. И от его работы зависит качество передвижения и безопасность на дороге. Сами по себе моторы мотоциклов во многом отличаются от автомобильных. Во-первых, это связано с габаритами легкой техники, а во-вторых с большей степенью форсирования.
Мотоциклетный мотор, как и автомобильный, имеет срок, который измеряется пробегом. После определенного пробега он теряет свою мощность, что сказывается на его работе в целом.
Среди самых распространенных проблем в системе двигателя является:
● потеря мощности;● большой расход топлива и масла;● трудности при запуске.
Для устранения мелких неполадок достаточно просто проведения диагностики и базовой регулировки систем и узлов двигателя мототехники. Но если диагностика определит более серьезные проблемы, то потребуется капитальный ремонт двигателя мотоцикла.
Практически каждый водитель самостоятельно может определить тревожные сигналы в системе двигателя.
На это могут указывать:
● нехарактерный шум и стук;● увеличение расхода топливно-смазочных материалов и охлаждающей жидкости;● снижение или повышение компрессии;● сизый дым из глушителя;● изменение характеристик в коробке передач.
Если вы обнаружили хоть один из вышеперечисленных признаков, сразу же обращайтесь к профессионалам. Любое затягивание может привести к более глобальной поломке мотора или его элементов.
Мотосервис HARD DAMAGE выполняет ремонт двигателей мотоциклов в Москве. Ремонт этой части мотоцикла может быть как локальным и направленным на устранение конкретных неполадок, так и глобальным капремонтом с последующей разборкой и сборкой двигателя.
Мотосервис выполняет работы любой сложности и любых марок мотоциклов – BMW, Aprilia Ducati, Honda, Suzuki, Kawasaki, KTM Yamaha.
В перечень услуг по ремонту двигателя входит:
● чистка и синхронизация карбюраторов мотоцикла;● чистка инжектора;● синхронизация карбюраторов;● замена прокладки ГБЦ и цепи ГРМ;● регулирование клапанов;● замена сцепления на мотоцикле и регулировка дисков сцепления;● полная установка выхлопной системы;● замена обгонной муфты;● замена сальников коленвала на мотоцикле;● снятие и установка двигателя любой конструкции и сложности (1 цилиндр, 2 цилиндра, 4 цилиндра).
Мотосервис проводит любые работы связанные с восстановлением двигателя, коробки передач и других узлов и систем двигателей, известных марок мотоциклов, скутеров, квадроциклов, гидроциклов и снегоходов.
Качественный ремонт значительно увеличивает послеремонтный ресурс двигателя и синхронизирует работу его элементов. Каждый двигатель уникален и без специальных знаний здесь никак не обойтись. Поэтому лучше доверять только проверенным мастерам своего «железного друга».
Специалисты утверждают, что правильный ремонт двигателя не просто продлит его срок службы, но и поможет усовершенствовать его элементы, и адаптировать под конкретные условия эксплуатации.
Ремонт двигателя происходит в несколько этапов:
1. Перед тем, как приступить к ремонту производится диагностика мотора на выявление неисправностей в нем;
2. Полная мойка агрегата;
3. Разборка пластиковых и других элементов, чтобы достать двигатель;
4. Съем двигателя и его мойка;
5. Выявление всех неисправностей и коррекция дефектов.
Чтобы разобраться в чем дело нужна тщательная диагностика, иначе замена отдельных деталей без предварительного установления причин приведет к новому ремонту;
6. Промывка и очистка деталей двигателя от нагара, закисаний и устранение других визуальных дефектов. Стандартная чистка карбюратора мотоцикла может решить проблему неисправностей в моторе;
7. Регулировка клапанов на мотоцикле;
8. Проверка состояния подшипников и передач двигателя;
9. Любые изношенные и детали, которые не подлежат ремонту;
10. Сборка, установка двигателя мотоцикла, запуск и обкатка.
Во время сборки двигателя необходима тщательная регулировка зазоров клапанов двигателя. От их положения во многом зависит работа систем двигателя и расход топлива.
Мотосервис HARD DAMAGE уже больше 7 лет осуществляет ремонт и уплотненное сервисное обслуживание мотоциклов, скутеров, квадроциклов и снегоходов любой сложность. Каждый сезон наши специалисты и механики обслуживают более 1000 единиц мото- и другой маневренной техники.
К нам обращаются владельцы известных мировых марок: Хонда, БМВ, Ямаха, Сузуки и других. Цена услуг зависит от сложности работ и стоимости деталей.
Наши специалисты имеют огромный опыт ремонта моторов, ходовой, узлов и систем мотоциклов. В работе мы используем только качественные и оригинальные запчасти и расходные материалы. Все запчасти находятся непосредственно на нашем складе, и вам не придется терпеть долгие дни или недели ожиданий.
Все ремонтные работы осуществляются только с применением специального профессионального оборудования, а на все работы и запчасти вы получаете гарантии мотосервиса HARD DAMAGE.
У нас самый высокий уровень сервиса, наши специалисты всегда учтут ваши пожелания по ремонту и тюнингу мототехники. Уютный зал ожидания с вкусным кофе поможет расслабиться и отвлечься во время ожидания обновленного «железного коня».
harddamage.ru
Ремонт двигателя и КПП мотоцикла в Москве
Симптомами ремонта двигателя мотоцикла являются:
Этапы работ по ремонту двигателя мотоцикла:
Все работы по ремонту двигателя мотоцикла проводит высококвалифицированный моторист с большим опытом работы. Дается гарантия 1 год на все производимые работы.
Регулировка клапанов мотоцикла
Проверяют тепловые зазоры согласно сервисному руководству на Ваш мотоцикл, а также после разборки головки или замены цепи привода ГРМ или при появлении характерного "цокота" из головки цилиндров.
Увеличенные зазоры приводят к появлению повышенного шума при работе двигателя, а при слишком малых зазорах клапана не будут закрываться, и двигатель не будет развивать номинальную мощность, а порой и трудно заводиться.
Наш мотосервис осуществляет:
Обращаем ваше внимание, что после регулировки клапанов в ряде случаев необходима синхронизация карбюраторов мотоцикла.
Ремонт и замена сцепления мотоцикла
В качестве одного из важнейших механизмов мотоциклов является сцепление. Это хоть и достаточно простой конструктивный элемент, однако на него возложена важная задача. В основе работы сцепления мотоцикла лежит сила трения между его дисками. Осуществляется передача крутящего момента мотора ведомым деталям, которые в свою очередь передают крутящий момент КПП.
Необходимость в ремонте сцепления в Москве продиктована различными факторами, среди которых можно выделить интенсивный режим эксплуатации мотоцикла в городе. Кроме того, ремонт сцепления мотоцикла востребован в случае планового износа отдельных его элементов.
Распространенные неисправности сцепления мотоцикла
Ремонт или техническое обслуживание сцепления мотоцикла предполагает следующие работы:
Довольно часто неисправность цепи газораспределительного механизма (ГРМ) мотоцикла обусловлена увеличением шага между звеньями. Как результат, двигатель мотоцикла начинает неправильно работать на холостом ходу. Поэтому вовсе неудивительно, что цепь начинает перескакивать одновременно на несколько зубьев. Чем это чревато? Во-первых, двигатель будет глохнуть. Во-вторых, могут быть замяты клапаны. А это в свою очередь может потребовать дорогостоящего ремонта двигателя мотоцикла в Москве. Поэтому при обнаружении первых признаков неисправности рекомендуется заменить цепь ГРМ мотоцикла.
Ремонт головки блока цилиндров (ГБЦ) двигателя мотоцикла
Ремонт головок блока (ремонт ГБЦ) - объемный комплекс работ, требующий достаточное количество специального оборудования, высококвалифицированного персонала и богатого опыта.
Мотосервис "PRORACING" оказывает следующий комплекс работ по ремонту ГБЦ мотоцикла:
www.proracing.su
Ремонт двигателя мотоцикла, регулировка клапанов в домашних условиях
Симптомами ремонта двигателя мотоцикла являются:1. Посторонний шум в двигателе
2. Большой расход масла
3. Расход охлаждающей жидкости
4. Малая компрессия в двигателе либо большая разница между цилиндрами
5. Чрезмерная высокая компрессия, связанная с нагаром в камере сгорания
6. Сизый дым из глушителя
7. Явная утечка масла из двигателя
Регулировка клапановРегулировка клапанов
У всех владельцев четырех тактных мотоциклов настает такой период как — пора заглянуть в клапана. Причина этому в основном повышенный цокот самих клапанов из-за износа или же из-за пробега. Регулировка клапанов один из самых интригующих моментов мотоциклиста, так как этот процесс на первый взгляд кажется сложным.
Процесс регулировки клапанов довольно непрост, требует аккуратности, свободного времени и хорошего инструмента. На инструменте остановимся подробно, нам потребуется набор щупов с точностью до 0,01 мм, набор ключей и накидных головок, динамометрические ключи, магнит для примагничивания мелких деталей, микрометр.
Инструмент нашли, выпросили или купили, теперь приступим. Мотор должен быть остывшим, чтобы не обжечься и правильно замерить клапанные зазоры. Они обычно замеряются при температуре 20°.
1. Отсоедините клапан регулировки давления в картере и снимите его
2. С правой стороны мотора открутите крышку, закрывающую звезду зажигания.
3. Крышку не потеряйте. Она еще пригодится.
4. После откручивания 3 болтов, крепящих клапанную крышку вы увидите такую картину.
5. Поверните коленвал по часовой стрелке до совпадения метки Т с меткой на крышке. Это Верхняя Мертвая Точка (когда впускные и выпускные клапана закрыты) для 1 и 3 цилиндра (слева направо по ходу движения).
6. С правой стороны метки IN и EX на распредвалах должны стать параллельно плоскости головки блока цилиндра.
7. Это важно! Если метка Т совпала, а метки IN и EX не совпали, значит поверните коленвал по часовой стрелке на 360 градусов (один оборот).
8. Подготовьте бумагу для записи значений зазоров.
9. Замеряйте клапанные зазоры на впускных клапанах 1го и 3-го цилиндра.
Поверните коленвал на полоборота (180°) и померяйте зазоры на выпускных клапанах 2-го и 4-го цилиндра.
Затем поверните коленвал на полоборота (180°) и померяйте зазоры на впускных клапанах 2-го и 4-го цилиндра.
Затем поверните коленвал на полоборота (180°) и померяйте зазоры на выпускных клапанах 1-го и 3-го цилиндра.
10. После замера у вас должна получиться подобная запись.
11. Стандартные значения указаны слева.
Впуск(IN) 0,20 мм (+/- 0,03) Выпуск (EX) 0,28 (+/- 0,03)Как мы видим почти все клапана уложились в зазоры, но впускные клапана 2-го и 4-го цилиндра вплотную подошли к пределам.
Снимаем натяжитель цепи ГРМ. Не забываем зафиксировать пружину стопором!
12. Снимаем крышку распредвалов.
13. Вынимаем выпускной распредвал. Будьте с ним предельно аккуратны, не поцарапайте его, не роняйте!
14. Под ними вы увидите колпачки, под которыми находятся шайбы.
15. С помощью магнита подцепите колпачок.
16. Всегда работайте только с одним колпачком, не перепутайте их!
17. Опять же с помощью магнита достаньте шайбу.
18. Измеряем ее толщину микрометром.
19. Теперь вам надо рассчитать толщину новой шайбы. Она рассчитывается по формуле :
A=(B-C)+D
A = нужная нам толщинва шайбы B = записанный клапанный зазор C = номинальный зазор D = толщина старой шайбыОсталось найти нужную нам шайбу в наборе.
20. Кладем новую шайбу обратно в паз.
21. Повторяем подобное со всеми клапанами, где требуется регулировка. Затем ставим выпускной распредвал обратно и снимаем впускной распредвал.
22. Регулируем клапана, там где это требуется. Затем ставим на место распредвал.
Правильно выставляем метки на распредвалах и звезде зажигания.
23. Устанавливаем на место натяжитель, не забываем его взвести. Затем устанавливаем его на место, вынимаем стопор и он натягивает цепь ГРМ.
24. Ставим на место крышку распредвалов. Болты затягиваем крест -накрест с усилием 12 N-m динамометрическим ключом. Затяжка от руки не допустима!
25. Ставим на место крышку. Болты затягиваем с усилием 10N-m.
26. Завинчиваем крышку звезды зажигания с усилием 18 N-m.
Ставим на место инжектора, свечные колпачки, подключаем их и остальное собираем в обратном порядке.
Регулировка клапанов одноцилиндрового двигателяРегулировка клапанов одноцилиндрового двигателя
Впускной клапан крупным планом
Поворачиваем против часовой стрелки, как показано, глядя в отверстие
Видим 3 радиальных выемки на маховике. Тот, который в середине является верхней мертвой точкой (ВМТ), однако четырехтактный двигатель может показывать нижнюю мертвую точку (я не уверен насчет этого суждения). Впрочем, это не имеет значения. Важно то, чтобы проверить выпускной зазор пока видна центральная выемка. Если получится, добираемся щупом 0,003 до зазора нашей ВМТ. Если нет, вращаем маховик дальше на 360 градусов против часовой стрелки и проверяем зазор. На этот раз он будет на месте. Таким образом шанс все сделать с первого раза составляет 50/50. Кстати, не используйте функцию трещотки на вашем инструменте. Как только вы увидите пазы маховика, просто крутите вашим инструментом один полный оборот чтобы увидеть пазы снова.
Требуется знать спецификации для клапанных зазоров. Сначала делаем выпускной зазор - 0,006-0,007 дюймов.
Нужны щупы соответствующего размера
Зазор выпускного клапана
Слишком большой зазор нуждается в регулировке. Легко может подойти 0,007 размер щупа
Требуется клапанный инструмент. Некоторые используют кончик спицы. Я обнаружил что вот такой инструмент намного удобнее. Используйте 3 мм сторону. Он будет прочно держать регулировочный болт клапана, пока вы затягиваете блокирующий болт.
Ослабьте стопорный болт 10 мм рожковым ключом, отрегулируйте клапан, проверьте щупом. Итак, один зазор правильный. Прочно удерживая клапан соответствующим инструментом, затяните гайку. Вот где инструмент удобен!
Затягивать стопорный болт надо динамометрическим ключом с усилием 10 ft*lbs
Динамометрический ключ в работе
Зазор слишком большой, требуется регулировка
Регулировка впускного клапана
Затягиваем впуск
Замена цепи ГРМЗамена цепи ГРМ
Не снимая двигателя (в случаях где доступ к головки и ЦПГ свободный), снимаем крышку клапанов, натяжитель цепи, распредвал, если доступ к цепи органичен, снимаем и головку. Выжимаем одним концом съёмника, штифт старой цепи ЦРМ, до конца, очень важно попасть в центр штифта. Проделываем ту же операцию с новой цепью, но есть маленький секрет, не нужно впрессовывать штифт новой цепи до конца (это затруднит последующую сборку цепи) Прикрепляем конец старой цепи, к концу новой цепи, аккуратно пропускаем цепь, через двигатель, не забывая проверить что бы цепь корректно попала на шестерню коленвала (важно) после того как новая цепь заняла своё место, рассоединяем старую и новую цепь и приступаем к сборке новой цепи. Для этого тем же концом съёмника запрессовываем штифт новой цепи, на место, при этом контролируем что бы отверстия под штифт, совместились. После переворачиваем обратным концом съёмник, зажимаем штифт новой цепи и ударами молотка развальцовываем штифт, при этом нужно крепко удерживать съёмник.
Замена маслаЗамена масла
Периодичность смены масла, а также объем и тип масла указываются в сервисном мануале мотоцикла. Для спорбайков, это как правило масло 10W-40, около 2,5 литров, каждые 6000 км. Масляный фильтр можно менять один раз на две смены масла.
Замена масляного фильтра
Замена масляного фильтра
Дождитесь, когда все масло стечет и начните замену масляного фильтра. Открутите старый фильтр.
Берем новый масляный фильтр и наливаем в него масла до краев. Это делается для того, чтобы при первом запуске мотор мотоцикла не работал без масла. Чтобы фильтр лучше “сел”, резиновую прокладку, которая идет по ободку фильтра, надо тоже обязательно жирно обмазать маслом.Фильтр на место закручиваем рукой! Затягивать съемником не нужно, а то потом не открутите! Просто с силой и до конца! Дождавшись, когда все старое масло вытечет, закручиваем на место болт, являющийся пробкой сливного отверстия и заливаем в двигатель свежее мотороное масло.
Чистка поддона и маслозаборникаЧистка поддона и маслозаборника
Бывает, что диски сцепления крошатся, и их части попадают в картер. Иногда при замене дисков роняют их куски в поддон. Определить это можно при замене дисков сцепления. Удалять куски из двигателя надо обязательно, т.к. они могут забить сопло маслозаборника или попасть в механизмы. Как правило, все куски падают в поддон, и для их извлечения необходимо его снять, предварительно слив масло двигателя. Снять поддон несложно, часто для этого требуется снять выхлопной коллектор и радиатор (предварительно слить антифриз). Учитывайте, что прокладку придется менять (очень сложно ее не повредить). Не рекомендуется использовать герметик. Когда снимите поддон, внимательно ищите куски, в том числе мелкие частицы. Маслозаборник надо не только очень тщательно проверит на наличие кусков во всасывающем сопле, но и промыть керосином, т.к. в нем могут быть мелкие частицы.После извлечения всех кусков попробуйте сложить из них недостающие фрагменты дисков. Отлично, если найдете все куски. Иногда это не удается сделать, тогда требуется дальнейшая разборка двигателя.
b.lodki-ua.com
Фотоотчет: Ремонт двигателя мотоцикла "ИЖ-Планета" 2, 3, 4 и пятой модели
Сейчас уже редко где можно встретить «Планету», особенно в стоковом исполнении. Дедовские сараи где они когда-то стояли в изобилии уже давным давно вычищены страждущими, а помойки где они когда-то валялись — поросли травой…
Единственное место где еще можно найти что-нибудь более менее приличное — местные газеты объявлений. Можно поискать и на «Авито», но прежде чем там брать — смотрите товар в живую, а то пришлют вам сумку кирпичей вместо двигателя…
Мне повезло: я нашел в местной газетенке объявление о продаже двигателя от мотоколяски, выехал на место, осмотрел, договорился, купил и привез домой. То что двигатель от мотоколяски пусть вас не пугает — двигатель полностью идентичен родному планетовскому.
Вобщем, когда я раскидал двигатель — обрадовался и тут же огорчился… Обрадовался потому что двигатель был стоковый и не имел следов вмешательства. Там еще масло было родное и свеча СССР-овская. Огорчился потому что поршневая и нижний подшипник шатуна были убиты.
Хороший заводской цилиндр в запасе у меня был: расточенный в ремонтный размер + к нему когда-то давно был куплен заводской поршень, хромированные кольца и палец.
Шатун я купил в интернет-магазине. Удалось найти еще заводской — не пластилиновый. Я его немного доработал: сделал небольшой пропил в нижней головке для улучшения смазки подшипника, разпрессовал коленчатый вал, старый шатун выкинул, поставил новый и потом отцентрировал коленчатый вал с помощью индикатора.
Инструменты
Из инструментов на понадобится:
- Дрель или шуроповерт
- Сверло по металлу на 4 — 5 мм
- Плоский надфиль
- Технический фен
- Оправки. В качестве оправок можно использовать сантехнические сгоны
- Мощная плоская отвертка
- Рожковый или накидной ключ на 14
- Хомут
- Молоток или киянка
- Масленка или шприц
- Герметик
Подготовка
Для выполнения качественного ремонта — детали двигателя должны быть чистыми, резьба в картере прогнана, сальники и прокладки — новыми.
Сначала чистим масляные каналы в кривошипных камерах. Каналов в двигателе Иж-Планета — два: один в левой половинке картера, другой — в правой. Находим каналы и если они сильно забиты — прочищаем их проволокой, промываем чистым бензином и продуваем сжатым воздухом.
Установка подшипников и сальников
Устанавливаем в левую половинку картера стопорное кольцо.
В зависимости от модели коренного сальника — устанавливаем в посадочное отверстие коренного подшипника распорную втулку, либо, если сальник у вас изначально стоял широкий (есть такие) — нагреваем картер и с внутренней стороны картера ставим сальник до упора в стопорное кольцо.
На моем двигателе стоял обычный узкий сальник, поэтому я ставлю втулку.
При помощи оправки в предварительно нагретый картер ставим коренной сальник.
Быстро, пока не остыл картер ложем на сальник маслонаправляющию шайбу. Маслонаправляющая шайба имеет профиль в виде блюдца. Кладем ее на сальник так, чтобы вогнутой стороной она была обращена к нам, а выгнутой к корзине сцепления.
Пока картер не остыл — прессуем в него с помощью оправки наружную обойму коренного подшипника.
Если вы будите менять коренные подшипники на новые — не поленитесь: найдите лист железа толщиной 7-8 мм, выпилите в нем клин под шатун, пропустите лист железа между щек коленчатого вала и при помощи оправки набейте коренной подшипник на цапфу.
Таким образом вы обезопасите себя от порчи коленчатого вала. Коренной подшипник имеет очень большой натяг и заходит на цапфу с очень большим усилием. Не редки случаи, когда люди попросту выбивали цапфу (цапфа на планетовском коленчатом вале запрессовывается в щеку) внутрь коленчатого вала, но подшипник одеть им так и не удавалось.
Родной made in USSR 2505 КМ
Установка коленчатого вала
Смазываем чистым моторным маслом кромки коренного сальника и подшипник. Укладываем левую половинку картера на брусочки, берем в руку коленчатый вал и с проворачиванием вставляем его в картер. Вставлять коленчатый вал нужно очень аккуратно немного проворачивая его. Если коленчатый вал тупо забить в картер — 100% завернете кромку сальника!
Сборка половинок картера
Обезжириваем разъем половинок, выбиваем немного направляющие втулки так, чтобы они вышли над плоскостью на 5-6 мм. В зависимости от вашего желания — собираем КПП. Лично я, КПП собираю только после сборки двигателя, мне так удобней.
Наносим на разъем любой автомобильный герметик, устанавливаем вторую половинку картера, достукиваем ее кияночкой, устанавливаем крышку КПП и стягиваем картер болтами.
Болты тянем не абы как, а строго по фен-шую: тянем примерно на треть усилия сначала середину крест накрест, потом периферию и постепенно увеличивая усилие за несколько кругов затягиваем болты на сколько хватает силы.
Установка цилиндропоршневой группы
Пока герметик не высох — крышку КПП снимать не желательно, спешка в этом деле не к чему. Лучше не торопить события и пока сохнет герметик — установить цилиндр.
Закапываем немного моторного масла:
- в верхнею головку шатуна
- нижнею головку шатуна
- в оба масляных канала кривошипной камеры
Для улучшения смазки в бобышках поршня желательно просверлить отверстия. Но можно и не сверлить — зависит от вашего желания.
Устанавливаем в бобышку стопорное кольцо поршневого пальца. Перед установкой — стопрное кольцо желательно немного разогнуть и обязательно после установки проверить как оно село:
- Если стопорное кольцо будет болтаться — разогните его или замените на новое
- Если стопорное кольцо ляжет не всей плоскостью — замените его на новое
Нагреваем феном поршень и при помощи оправки забиваем палец в поршень так, чтобы он вышел внутрь не более чем на 5-6мм.
Ищем на днище поршня метку в виде стрелки.
Ориентируем поршень стрелкой к выпускному окну цилиндра («на выхлоп»), надеваем поршень на шатун, забиваем поршневой палец и устанавливаем второе стопорное кольцо.
Вставляем в цилиндр кольца и замеряем щупом зазор между замками:
- Если зазор будет меньше 0,3—0,45 — подточите замки колец надфилем
- Если зазор будет больше 0,3—0,45 — ставьте новые кольца, если не поможет — растачивайте цилиндр в ремонтный размер
Для улучшения притираемости колец и снижения шума от работы двигателя на кромках колец желательно снять фаски. Если охота позаморачиватся: положите кольцо на ровную поверхность и надфилем немного скруглите кромки.
Одеваем кольца на поршень, заливаем поршень с кольцами маслом, устанавливаем прокладку под цилиндр (желательно на герметик), стягиваем кольца хомутом. Хомут вырезаем из жести и из этой же жести сгибаем скобу, которой мы будем его фиксировать.
Одеваем цилиндр.
После того как кольца зайдут в цилиндр — расстегиваем хомут, осаживаем цилиндр и прикручиваем его к картеру.
Проворачиваем несколько раз коленчатый вал и если поршень будет ходить в цилиндре легко и без скрежета — опускаем его немного вниз, наливаем в цилиндр немного моторного масла, устанавливаем на цилиндр новую прокладку и прикручиваем головку.
Устанавливаем на свое место дополнительный опорный подшипник коленчатого вала, сверху ложем необходимое количество регулировочных шайб и фиксируем его стопорным кольцом. Регулировочные шайбы должны обеспечивать осевой люфт коленчатого вала в пределах 0,1мм.
Перед установкой закрытые подшипники нужно обязательно открыть! Сюда идет обычный 304.
С другой стороны коленчатого вала устанавливаем фланец с коренным сальником. Обратите внимание на масляный канал по которому масло поступает к правому коренному подшипнику коленчатого вала. По старой «доброй» колхозной традиции этот канал замазывают герметиком и смазка подшипника прекращается. Во избежание этой неприятности — ставьте фланец на сухую без герметика и будет все пучком.
После того как высохнет герметик можно приступать к регулировке и сборке коробки переключения передач и ставить на место корзину сцепления.
Номера подшипников и сальников двигателя мотоцикла Иж-планета 2, 3, 4 и пятой модели.
- Коренные подшипники коленчатого вала 2505к
- Дополнительный опорный подшипник коленчатого вала 304
- Правый сальник ИЖ-ю сб. 1-48-3
- Левый коренной сальник ИЖ-ю сб. 1-50
alisa-motors.ru
Ремонт двигателя мотоцикла Bandit 1200
Ремонт двигателя мотоцикла Bandit 1200
Ремонт мотора мотоцикла Suzuki Bandit после некорректной переборки в другом сервисе.
Со слов владельца - после некачественной сборки мотор был запущен. "Было много масляного дыма и посторонние шумы".
ДВСку привезли к нам в разобранном состоянии. Детали были сильно загрязнены, следы коррозии на стальных элементах крепежа означали, что двигатель пролежал в сыром помещении минимум несколько лет - неизвестно, в собранном или вскрытом состоянии.
Отдельно в коробке шел набор "сделай сам" - смесь крепежа от этого двигателя, и нескольких других мотоциклов. Было сказано, что детали от этого мотора "вроде бы все здесь" :)
Мы смогли не просто восстановить этот двигатель, но и форсировать его - увеличением рабочего объема, установкой спортивных распредвалов и карбюраторов.
Начнем с разборки того, что пока не может называться Двигателем - и изучения состояния имеющихся деталей. Так же нужно определить все ли детали на месте, оригинальные они - или нет.
Блок цилиндров
Большое количество герметика на привалочных плоскостях. Царапины. Следы окисления на алюминиевых деталях и коррозия на крепежных элементах, гильзах. Сборка явно была выполнена с нарушением заводских технологий - видимо, повторно использовались старые прокладки ГБЦ и блока, а "для надежности" применили герметик.
Головка блока цилиндров
Снаружи - более-менее целая (за исключением грязи, нагара и герметика).
Но внутри - все имеющиеся маслоканалы тщательно заполнены герметиком.
Картер двигателя
Вот в таком виде он попал к нам на стол:
Внешний осмотр - некоторое количество отсутствующего крепежа. Все резиновые уплотнения подлежат замене, так как они высохли и потрескались от старости. Большое количество грязи внутри.
После снятия боковых крышек стало понятно, что над кронштейном датчика положения коленчатого вала тоже "поработали" - отверстия под крепежные винты довольно неаккуратно расточены, видимо была попытка вращать датчик для изменения начального угла опережения зажигания. На пластине нацарапаны "метки".
Поддон двигателя
Как говорится - без комментариев.
Внутри найдено:
- Направляющая от ГБЦ
- Песок
- Обломки пластика от башмака цепи ГРМ
- Герметик
- Тонкая металлическая шайбочка
- Насекомое в сетке маслоприемника
Мы затрудняемся идентифицировать, к какому виду из отряда Blattoptera принадлежит данное насекомое - и предоставляем уникальную возможность сделать это Читателю самостоятельно:
Биология - не наш профиль, мы не можем рассказать - чем моторное масло привлекательно для тараканов, а вот объяснить как появились глубокие царапины на шейках коленвала - проблем нет:
На всех шейках коленвала присутствует существенный износ, царапины и задиры. Такие повреждения характерны для наличия крупных частиц абразива в масле. Нескольких минут работы мотоцикла после неправильной переборки двигателя - хватило, чтобы получить существенную выработку на деталях:
Похоже, что в мотор при сборке попал абразив от "болгарки", точила (наждака), или чего-то подобного.
На этом заканчиваем историю "как делать не надо", и переходим непосредственно к ремонту мотоциклетного двигателя:
Восстановление коленвала мотоцикла
Установили коленвал на станок. Напылили металл на поврежденные шейки методом Plasma Spray Coating
После нанесения покрытия выполнили финишную полировку вала. Результат ремонта мотоциклетного коленвала - на фото:
Ремонт ГБЦ мотоцикла
Разобрали и вынули клапана ("рассухарили").
Отмыли от грязи и герметика. Поправили поврежденные седла, заменили маслосъемные колпачки:
Для очистки клапанов от нагара использовали подогретый щелочной раствор и ультразвук. Щетки и прочие механические средства применять нельзя - ими можно оставить царапины на стержне клапана:
Далее - особенно комментировать нечего. Обычный процесс ремонта и сборки картера двигателя мотоцикла. Очистка всех деталей, использование только оригинальных комплектующих, новые прокладки и вкладыши. Единственное, что было модифицировано в "нижней" части двигателя - на зуборезном станке несколько "завалены" углы на некоторых шестернях КПП для снижения ударных нагрузок при переключении передач.
Фотографии сборки блока:
Механизм привода копирного вала КПП:
Посадочное отверстие под сальник вала ведущей звезды пришлось наваривать "аргоном" и протачивать - были глубокие забоины - видимо, кто-то пытался извлечь сальник без разборки двигателя, поддевая его отверткой или чем-то подобным:
Перед установкой коленвала на вкладыши нанесено специальное густое масло, обеспечивающее смазку в первые секунды работы двигателя, пока штатный маслонасос не прокачает систему:
Корзина сцепления - пожалуй, единственная деталь, которую не пришлось ремонтировать:
Расточка и сборка блока цилиндров
Установлены поршневая группа Wiseco увеличенного диаметра:
Блок цилиндров - расточен под соответствующий диаметр, выполнена хонинговка (финишная обработка, удерживающая масляную пленку на зеркале цилиндра). Подобран оптимальный зазор в компрессионных кольцах. Блок установлен на нижнюю часть картера:
Так как шпильки крепления ГБЦ - одноразовые, к тому же они были существенно повреждены коррозией и предыдущими "мастерами" - разумеется, мы их заменили на новые - но не фирмы Suzuki, а усиленные - выдерживающие почти вдвое большую нагрузку на разрыв. На фотографии - стандартная шпилька (справа) и усиленная.
Штатные распредвалы этого мотора - повреждены коррозией. Ставим спортивные валы Youshimura:
Окончательная сборка головки цилиндров и газораспределительного механизма:
Ставим маслоприемник и поддон:
Закрываем клапанную крышку. Ставим масляные магистрали, стартер, генератор. На этом - ремонт двигателя мотоцикла можно считать завершенным.
Настройка карбюраторов на диностенде
После сборки - двигатель был установлен в раму мотоцикла. Вместо штатный карбюраторов - установлены плоскодроссельные Mikuni.
Несмотря на то, что производитель карбюраторов указывает, что "синхронизация не требуется" - на всякий случай мы проверили ее электронным прибором собственной разработки. Разумеется, присутствовала разница давлений между цилиндрами. После точной настройки карбюраторов и выравнивания давления - мотор на холостом ходу заработал значительно ровнее:
После подбора положения иглы и главного жиклера - диностенд показал впечатляющие 151л.с. и крутящий момент в 122 Ньютонов !Результаты - на графиках со стенда:
aes-moto.ru
Как сделать правильный капитальный ремонт двигателя, чтобы он был лучше нового.
Большинство водителей, отдавая двигатель своего автомобиля в какое нибудь СТО для капитального ремонта, заранее знают, что отремонтированный мотор будет всё же несколько хуже нового, и ресурс его будет естественно меньше. Ведь многие рассуждают так — «новый есть новый». Но очень мало водителей знают, что если сделать ПРАВИЛЬНЫЙ капитальный ремонт двигателя, то он «пробежит» намного больше нового серийного заводского мотора.
А что значит правильный капремонт и какой он должен быть? Об этом большинство водителей и не подозревают и спокойно отдают свой двигатель в сервис, надеясь, что там якобы мастера всё сами знают. Только вот впоследствии, водители удивляются малому ресурсу отремонтированного двигателя, и грешат на некачественные запчасти. В этой статье мы подробно разберём, что значит правильный капремонт двигателя, и возможно после прочтения этой статьи, многие водители начнут более внимательно выбирать ремонтников и ремонтную мастерскую, или же всё таки начнут ремонтировать двигатель своими силами.
Я уже писал о ремонте двигателей в этой, вот этой ну и вот в этой статьях, в которых я описал азы обычного капремонта двигателей автомобиля и японского мотоцикла и желающие могут кликнуть и почитать. Но кто хочет СУЩЕСТВЕННО увеличить послеремонтный пробег (ресурс) двигателя своего мотоцикла или автомобиля, то советую читать дальше.
Так как же осуществить такой капитальный ремонт своего отработанного двигателя, чтобы он стал лучше нового заводского? Да не так уж и сложно, если принять во внимание то, что серийное производство двигателей, это обычный конвеерный поток, в котором серийным деталям двигателя не уделяют должного внимания, это просто не реально.
Ну а ремонт двигателя, даже поставленный на поток, в какой то хорошо оснащённой мастерской — это искусство, потому что для каждого двигателя нужен индивидуальный подход. Например при деффектовке деталей, при которой каждая деталь тщательно изучается, чуть ли не под микроскопом, а иногда и дорабатывается специалистами и становится лучше новой детали.
В некоторых грамотных зарубежных мастерских, капитальный ремонт любого двигателя, плавно переходит в его тюнинг, то есть доводку серийных деталей до совершенства. И не смотря на то, что такой ремонт дороже обычного (ведь ручной труд всегда дороже), спрос на него всегда большой и клиенты стоят в очереди.
Потому что отремонтированный таким способом двигатель, во первых намного мощнее и долговечнее нового серийного мотора, а во вторых он ещё и дешевле нового серийного мотора. Ведь большинство самых дорогих и трудоёмких операций, делаются только на заводе, при производстве двигателя с нуля.
И если даже зарубежные заводские (серийные) двигателя при ремонте нуждаются в доводке и усовершенствовании, то что говорить про наши отечественные заводы, которые работают в условиях низкой оплаты труда рабочим и постоянной нехватки средств на усовершенствование серийного производства. Где даже крепёжные болты сидений забиваются молотком ?!?!
И в целях экономии времени (а время как известно это деньги) на большинстве отечественных автозаводов, намеренно пренебрегают некоторыми важными операциями. Например каждый инженер или металло-эксперт знает, что после отливки блока цилиндров, он должен отлежаться на полке определённое время.
И благодаря этой выдержке (старению), постепенно снижается внутреннее напряжение каждой детали, и при этом она может даже немного потерять форму (покоробиться). И только после того, как деталь принимает свою окончательную форму, только после этого её можно начинать обрабатывать (выбирать фрезой все отверстия и плоскости).
Так вот, на некоторых заводах выдержку блоков и головок не делают, и в итоге, после обработки отверстий и плоскостей, со временем деталь меняет форму, и уже все плоскости не параллельны, отверстия тоже (например постели подшипников валов). И плоскости разъёма блока и головки, после сборки будут не параллельны коленвалу, распредвалу и другим валам двигателя. Нетрудно догадаться, какой в итоге получится двигатель и каков будет его ресурс.
Из вышесказанного следует сделать вывод, что отечественный бэушный блок цилиндров или головка, которые проработали не одну сотню километров, ни чем не хуже, а даже лучше новых деталей, так как со временем произошла приработка сопряжений, осадка и детали в старении не нуждаются. И это большой плюс для того, чтобы после ремонта такие детали стали лучше новых заводских.
Не менее важная деталь, это цилиндры двигателя, а точнее их поверхность. Многим известно, что после расточки цилиндров (о расточке подробнее читаем тут), их поверхности (стенки) нужно отхонинговать (хотя современные станки позволяют производить хонинговку и без предварительной расточки).
То есть необходимо обработать стенки всех цилиндров специальным инструментом, называемым хоном, который после обработки превратит поверхность стенок цилиндров в шершавую, с очень мелкими канавками и выступами (если смотреть под микроскопом, как на рисунке 1). Большинство водителей знают, что благодаря мельчайшим канавкам на поверхности цилиндров лучше удерживается моторное масло (для смазки поршней и колец).
Так вот, для сравнения и для дальнейшего размышления, приведу ещё один пример, объясняющий почему у отечественных двигателей (да и у зарубежных тоже — после нашего ремонта) такой маленький пробег (у новых моторов) и послеремонтный пробег тоже. А всё дело в том, что на наших отечественных автомобильных заводах, да и в 95% всех ремонтных мастерских, применяют для хонинговки цилиндров алмазные абразивные бруски.
На зарубежных же заводах и ремонтных мастерских, никогда не пользуются такими брусками и применяют безобразивные бруски, которые следует менять в несколько десятков раз чаще, чем алмазные абразивы. А нашим заводам и мастерским главное что? Да то, что абразивный брусок остаётся пригоден для работы даже после тысячи отхонингованных блоков, ведь какая получается экономия?! И плевать на то, что ресурс мотора снизится в десятки раз, зато производство дешёвое.
Но почему же абразивные бруски для хонинговки не применяют за рубежом и от этого ресурс их двигателей намного больше? Да потому что при обработке поверхности цилиндра таким бруском, частицы абразива внедряются (шаржируются) в металлическую поверхность стенок цилиндра, а затем при работе двигателя, «съедают» его поршни с кольцами, и в итоге происходит быстрый износ поршневой.
А безобразивные бруски, которые применяют за рубежом, и которые намного быстрее образивных изнашиваются, изготавливают из достаточно мягких сплавов, и при работе они как бы не сколько срезают поверхность стенки цилиндра, а сколько давят и выглаживают её. В итоге, на металлической поверхности стенки цилиндра образуется очень тонкий слой, работающий не как абразив, а примерно как твёрдая смазка, существенно сокращающая износ цилиндров и поршней (и уменьшающая трение).
Кстати, если кто не знает, за рубежом уже давно забыли что такое ремонтные кольца и не применяют их. Зачем, когда на современных зарубежных машинах (например свежие Мерседесы), при правильном изготовлении блока мотора (а на некоторых никасилевое покрытие) и современном методе изготовления поршневых колец, нет необходимости менять кольца, и «проходит» двигатель без замены колец миллион километров пробега ! Кто хочет узнать об этом подробно, то кликаем здесь и читаем на здоровье.
Выше мы рассмотрели один из важных моментов правильной хонинговки цилиндров, который если вы примените при ремонте своего двигателя, то существенно увеличите его ресурс. Но существуют и другие важные моменты. Не все водители и даже ремонтники знают, что после установки блока на двигатель и затяжки его головки, геометрическая форма цилиндров немного меняется, так как металл есть металл. То есть при обжатии цилиндр (или цилиндры) перестаёт быть строго цилиндрическим, даже если его изготовили очень точно и до обжатия он был таким.
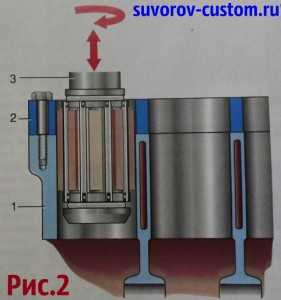
Правильная хонинговка цилиндра.1 — блок цилиндров, 2 — алюминиевая плита с отверстиями, вместо головки, 3 — хон с безабразивными брусочками.
А это значит, что и обрабатывать при ремонте любой цилиндр, нужно ОБЖАТЫМ примерно так же, как он будет обжат на двигателе после ремонта. Проще говоря, нужно изготовить из толстой плиты (или из старой головки — см. рисунок 2) плиту, с отверстиями под хон и под крепёжные болты, которые обожмут цилиндры так же как и на двигателе (с таким же положенным моментом). После расточки цилиндров и отжатия болтов (и снятия плиты и блока), геометрическая форма отремонтированных цилиндров, тут же немного нарушится.
Но теперь остаётся только собрать и установить на отремонтированный таким способом блок штатную головку двигателя и обжать весь бутерброд положенным моментом, и геометрия расточенных цилиндров станет идеальной ! Цилиндры отремонтированного таким способом двигателя, станут лучше новых заводских! Ведь при серийном производстве двигателей на заводах, вышеописанную правильную технологию расточки и хонинговки вряд ли применяют (а если и применяют, то только на зарубежных престижных автомобилях).
Кстати, и в большинстве ремонтных мастерских, так правильно моторы тоже не ремонтируют, а если кто то из редких ремонтников и делает это, то его ещё надо поискать, чего вам очень советую. Ну и напоследок ещё один нюанс правильного ремонта.
Большинство ремонтных мастерских, при расточке цилиндров, главной (базовой) плоскостью считают нижнюю плоскость картера (там где поддон двигателя). Проще говоря, берут и ставят блок цилиндров на крепёжный стол станка, затем зажимают блок и начинают обработку. Но никто из расточников никогда не задумывается (а если и задумывается, то только когда делает свой двигатель), а точно ли параллельна нижняя плоскость блока оси коленчатого или распределительного вала?
И если даже при серийном производстве, особенно отечественном, и выполнили это важное условие (что с трудом верится), то от каждодневных нагрузок в процессе эксплуатации, это условие со временем нарушилось. И может быть даже всего на доли градуса, а может и больше, а кто это знает и кто проверяет ? Да всего лишь какие то единицы действительно грамотных мотористов.
В итоге, ось коленвала (да и распредвала тоже) оказываются не перпендикулярны стенкам цилиндра (осям цилиндров). И получается, что на шатуны двигателя постоянно будет давить пусть небольшая, но всё таки изгибающая сила. Кольца, поршни, да и стенки цилиндров будут изнашиваться неравномерно. К тому же между поршнями и стенками цилиндров, будет образовываться не правильная плёнка масла, а менее устойчивая клинообразная плёнка, которая будет постоянно выдавливаться из под трущейся пары (поршень-цилиндр).
Кстати, слой масла в виде клина, будет и между шейкой и вкладышем коленвала (см. рисунок 3). Результат всего этого — ускоренный износ и естественно малый ресурс двигателя.
Из вышесказанного следует сделать вывод, что прежде чем начинать обработку цилиндров блока, очень важно проверить постели коренных вкладышей (да и любых постелей) на их точную цилиндричность и соосность (точную перпендикулярность отверстий постелей к отверстиям цилиндров). И уже исходя от этого, правильно закреплять блок в станке и обрабатывать поверхность цилиндров.
При необходимости лучше не подкладывать под нижнюю плоскость блока пластины, если эта плоскость не перпендикулярна осям цилиндров, а лучше шлифануть эту плоскость на станке, чтобы исправить дефект. И после этого можно буде уже спокойно укладывать блок на стол расточного станка и растачивать, или хонинговать цилиндры (опять же правильным — безабразивным хоном). Настоящие мотористы профессионалы (к сожалению чаще за рубежом) делают именно так.
И если даже кто то не вс состоянии сделать правильный капремонт двигателя своими силами (не у каждого ведь есть станочный парк в собственной мастерской), то по крайней мере вы, прочитав эту статью, сможете уже адекватно контролировать мотористов, которым вы доверите ремонт своего двигателя, а это важно.
Я надеюсь, если прочитав эту статью, вы сделаете капремонт своего двигателя, учитывая все нюансы, описанные здесь, то в итоге вы увидите очень интересные результаты такого ремонта, а именно: намного снизится угар и естественно расход масла, а так же выхлоп вредных веществ в атмосферу (может кому то это не важно, но мне да), чуть уменьшится расход топлива (ведь потери на трение уменьшатся), и существенно уменьшится скорость износа цилиндров, колец и поршней.
Ну, а самый главный прикол такого правильного капитального ремонта двигателя, это то, что ресурс вашего отремонтированного мотора, почти в два раза превысит ресурс абсолютно новенького заводского серийного двигателя; успехов всем!
suvorov-castom.ru
Устройство и ремонт мотоциклов.
Очистка от нагара.
Камеры сгорания цилиндров чаще требуется очищать от нагара у двухтактных двигателей, чем у четырехтактных, причем тем чаще, чем меньше рабочий объем цилиндра. У двухтактных двигателей, имеющих рабочий объем 125 см3, нагар следует очищать после 2000 км пробега мотоцикла, а у двигателей, рабочий объем которых равен 350 см3, — после 4000 км. В четырехтактных двигателях очистку от нагара производят после 5000—6000 км пробега, а при малом расходе масла и применении бензина А-74 этот срок увеличивается вдвое.
Канавки для поршневых колец очищают при замене их. Специально очищать канавки требуется только в случае уменьшения компрессии вследствие недостаточной подвижности колец.
Глушители двухтактного двигателя чистят по мере надобности, примерно после 4000—8000 км пробега мотоцикла (больший пробег относится к двигателям с большим рабочим объемом цилиндра). У четырехтактного двигателя необходимость очистки глушителя наступает не ранее чем после 10 000 км пробега мотоцикла.
Удаляемый нагар желательно предварительно размягчить, смочив его растворителями. Для этого, например, на головку поршня кладут на некоторое время тряпку, намоченную в керосине с растворителем (ацетоном). После этого нагар можно легко удалить. Сухой нагар соскабливают ножом, шабером или любым другим скребком.
Нагар в канавках удобно снимать специальным приспособлением (рис. 31) или обломком поршневого кольца. При соскабливании нельзя повреждать адюминиевые детали, в особенности боковые стенки канавок поршня. К концу очистки для ускорения работы можно использовать щетку из медной проволоки.
Нагар в двигателях, работавших на этилированном бензине, содержит ядовитые отложения свинца. При удалении нагара необходимо соблюдать меры предосторожности. Очищаемые детали предварительно следует выдержать в керосине; эту работу нельзя производить в жилом помещении.
Для удаления нагара из двигателя снимают головку цилиндра и выпускную трубу. При отделении головки от цилиндра надо следить за тем, чтобы не была повреждена прокладка. На ней ставят метку для установки при сборке в прежнее положение. Гайку, крепящую выпускную трубу к патрубку цилиндра или головки, следует отвертывать не ударами, а ключом для круглых гаек; при этом нужно следить за тем, чтобы не была повреждена прокладка, находящаяся между трубой и патрубком.
Перед очисткой головки поршня он должен быть установлен в в. м. т.
У двухтактных двигателей очищенный поршень устанавливают в н. м. т., закрывают тряпкой продувочные окна и очищают нагар в выпускных окнах
Очищенные от нагара детали и крепящие их болты и гайки промывают керосином и вытирают чистой тряпкой. Перед установкой головки на цилиндр осматривают соединяемые поверхности и прокладку. Обнаруженные неровности осторожно спиливают бархатным напильником, а прокладку, имеющую разрывы, заменяют новой. При отсутствии прокладки заводского изготовления ее вырубают вручную из армированного асбестового полотна. Сначала в прокладке делают малые отверстия, потом — большое, после чего обрезают по контуру. Можно также вырубить прокладку из листовой красной меди или алюминия толщиной 0,3—1 мм. Медную прокладку перед установкой нужно нагреть докрасна и быстро опустить в воду для того, чтобы она была мягкой.
Устанавливая головку, вначале слегка завертывают две гайки (или два болта), расположенные по диагонали; потом также попарно завертывают противолежащие гайки, затем, начиная с первой пары, окончательно затягивают гайки, постепенно увеличивая усилие, прилагаемое к ключу. При таком порядке затяжки гаек или болтов головки прокладка зажимается равномерно. Попытки чрезмерно тугим завертыванием достигнуть герметичности при испорченной прокладке приводят к повреждению резьбы или обрыву болтов. После нескольких часов работы двигателя, дав ему остыть, подтягивают на холодном двигателе ослабевшие болты и гайки головки.
Для очистки от нагара канавок поршня снимают цилиндр, стремясь не повредить прокладки под ним. Новую прокладку вырубают из любой плотной той же толщины бумаги и пропитывают олифой или маслом. Если в верхней части цилиндра имелась ступенька вследствие износа его зеркала, то при установке прокладки из более тонкой бумаги во время работы двигателя будет слышен стук. При глубоких повреждениях на соединяемых плоскостях цилиндра и картера прокладку надо смазать бакелитовым или шеллачным лаком или нитрокраской.
Для защиты от поломки юбки поршня при случайном ударе о шатун, когда цилиндр снят, под поршень устанавливают деревянный брусок 1 с прорезью (рис. 32, а) или внутрь поршня втискивают свернутую чистую тряпку 2 (рис. 32, б). Для предохранения картера от попадания посторонних предметов его прикрывают фартуком, завязанным веревкой вокруг шатуна.
Кольца вынимают из канавок и устанавливают в канавки поршня обязательно с помощью трех-четырех стальных пластинок (рис. 33). Две пластинки просовывают под концы кольца в стыке, а с помощью других выводят кольцо из канавки. Мотоциклисты часто не пользуются стальными пластинками и считают, что если кольцо не сломалось, то операция выполнена правильно. Но при снятии и надевании кольца без пластинок неизбежна его деформация, вследствие чего нарушаются точность формы кольца, его приработка и равномерность давления на стенки цилиндра. При снятии колец отмечают их размещение по канавкам и при сборке устанавливают на прежние места. При этом необходимо убедиться в том, что все углы канавок поршня очищены от нагара; особенно тщательно надо очищать канавки около стопоров (у двухтактного двигателя). Замки колец у двухтактных двигателей располагают точно на стопорах. У четырехтактных двигателей замки колец размещают в канавках в шахматном порядке. Желательно, чтобы замки были обращены к боковым и передней стенкам цилиндра, которые менее нагружены (рис. 34). У двигателей типа М-62 менее нагруженная стенка в правом цилиндре — верхняя, а в левом — нижняя. Перед установкой цилиндра поршень с кольцами слегка смазывают маслом.
При надевании цилиндра на поршень применяют для сжатия колец хомут из жести (рис. 35, а) или массивное кольцо с конусным отверстием и вырезанным участком для прохода шатуна (рис. 35, б).
Последнее приспособление более удобно, так как при его использовании можно следить за расположением стыков колец в сомкнутом состоянии, что особенно важно при сборке двухтактного двигателя. Однако цилиндр можно надевать на поршень, сжимая кольцо, например, поясным ремнем или придерживая концы кольца отверткой. При сжатии кольца следят за тем, чтобы замок сомкнулся, и слегка нажимают на цилиндр. При сильном нажатии на цилиндр кольца ломаются. Застревание цилиндра на кольце соответствующего диаметра у двухтактных двигателей свидетельствует о неточном совпадении замка кольца со стопором в канавке поршня. Во время установки цилиндра отверстия в его фланце должны находиться против соответствующих шпилек картера. При повертывании цилиндра вокруг продольной оси в четырехтактном двигателе нарушается правильное расположение замков колец, а в двухтактном двигателе могут сломаться кольца в результате попадания их концов в окна цилиндра. Гайки крепления цилиндра завертывают так же, как и гайки головки, о чем было указано выше.
Замена поршневых колец.
Примерный срок службы поршневых колец в четырехтактных двигателях соответствует 10 000 — 15 000 км пробега мотоцикла. У двухтактных двигателей этот срок значительно меньше (4000—8000 км). Меньшие цифры относятся к двигателям, имеющим меньший объем цилиндра. При применении высококачественных масла и бензина и установке фильтра тонкой очистки и эффективного воздушного фильтра можно значительно увеличить срок службы поршневых колец. Компрессионные поршневые кольца заменяют в случае уменьшения компрессии, а масло-съемные — при увеличении расхода масла, если установлено, что они неисправны.
Признаками износа поршневого кольца, при котором его необходимо заменить, являются увеличение зазора в замке (больше 3 мм), потемнение отдельных участков рабочей поверхности и значительное уменьшение его упругости. Замена колец при увеличении зазора в пределах 1 мм мало целесообразна. У маслосъемных колец дополнительным признаком необходимости замены их является износ рабочих кромок.
Для определения износа кольцо вставляют в цилиндр. Затем положение кольца выравнивают, вводя поршень. Зазор в замке кольца измеряют щупом 3 (см. рис. 24)..
Перед установкой нового кольца следует проверить зазор в замке, соответствие высоты кольца ширине канавки и толщины кольца глубине канавки, а также прилегание кольца к зеркалу цилиндра. Ориентировочно зазор в замке должен быть равен 0,2— 0,3 мм или примерно 0,1 мм на каждые 25 мм диаметра цилиндра. У верхнего кольца зазор в замке должен быть несколько больше, чем у нижних колец, так как при работе двигателя оно нагревается сильнее. Если зазор мал или отсутствует, то спиливают торцы кольца в стыке зазора (рис. 36, а). При недостаточном зазоре кольцо, расширившееся во время работы двигателя, вызовет заклинивание поршня в цилиндре. Для работы в цилиндре, имеющем допустимый износ, кольца в стыке необходимо спилить так, чтобы нормальный зазор в замке получался у середины цилиндра и был меньше у нижней, менее изношенной части зеркала.
Для проверки соответствия высоты кольца ширине канавки кольцо вставляют наружной стороной в канавку. Кольцо должно под действием своего веса плотно входить в канавку и свободно в ней перекатываться. Зазор между кольцом 2 и боковой стенкой канавки поршня 1 при измерении щупами (рис. 36, 6) составляет примерно 0,02—0,06 мм у четырехтактных двигателей и 0,05 — 0,1 мм у некоторых двухтактных двигателей. При тугой посадке кольцо будет недостаточно подвижно, пригорит и заклинится в канавке. При увеличении зазора во время работы двигателя кольцо будет перемещаться между боковыми стенками и угар масла увеличится, а боковые стенки канавки и торцы кольца быстро износятся; возможна даже поломка кольца. Поэтому если между кольцом и боковой стенкой канавки зазор будет очень большим, то такое кольцо не пригодно для использования.
Толщину кольца можно уменьшить до нужного размера, шлифуя его торцы мелкой наждачной шкуркой, положенной на ровную поверхность.
Соответствие толщины кольца глубине канавки проверяют следующим способом. Кольцо 2 наружной стороной вставляют в канавку поршня 1 и к поршню, параллельно его продольной оси, прикладывают ребром линейку 3, как показано на рис. 36, в. Кольцо должно утапливаться в канавке на 0,5—0,65 мм и свободно перемещаться в радиальном направлении между дном канавки и линейкой. Если перемещение кольца отсутствует, то при расширении поршня и образовании под кольцом нагара кольцо наружной поверхностью сильно будет давить на зеркало, и поршень заклинится в цилиндре. Поэтому необходимо подбирать кольцо с меньшей радиальной толщиной или, в крайнем случае, спилить кольцо изнутри.
Для проверки прилегания кольца к зеркалу цилиндра кольцо вставляют в цилиндр и смотрят, нет ли просвета между кольцом и зеркалом. При больших просветах кольцо бракуют.
У двухтактных двигателей перед установкой колец дополнительно проверяют сопряжение выемки в замке кольца со стопором в канавке поршня. В некоторых случаях приходится ставить кольца несколько большего размера. У таких колец следует спиливать торцы в замке до получения нужного зазора. Кольцо со спиленными торцами будет удовлетворительно работать, если его диаметр до спиливания торцов в замке превышал диаметр цилиндра не более чем на 1—1,5 мм. При большем первоначальном несоответствии диаметров кольцо, установленное в цилиндр, приобретает форму овала (рис. 36, г) и не будет плотно прилегать к зеркалу. Опиливание торцов колец дает худший результат при установке их в цилиндрах малого диаметра. Лучше поставить приработанное кольцо с увеличенным зазором в стыке, чем кольцо, плохо прилегающее к зеркалу цилиндра.
При установке приработанного кольца с увеличенным зазором в стыке меньше проходит газов в камеру сгорания через зазоры между поршнем и цилиндром. В случае установки кольца, плохо прилегающего к зеркалу цилиндра, возрастает температура поршня, вследствие малой площади контакта кольца с зеркалом цилиндра.
Замена поршня.
Срок службы поршня соответствует примерно времени износа на нем двух комплектов поршневых колец. У поршня изнашиваются канавки для колец, отверстие под палец и юбка. Пределом износа поршня можно считать образование между нижней частью юбки и зеркалом цилиндра зазора, составляющего 0,005 диаметра цилиндра, что при диаметре цилиндров 50, 60, 70 и 80 мм соответствует 0,25; 0,30; 0,35 и 0,4 мм. Зазор измеряют у нижнего края передней или задней стороны юбки при расположении поршня в нижней части цилиндра.
У четырехтактного двигателя диаметр нового поршня внизу юбки (по которому подбирают поршень к цилиндру), измеряемый на расстоянии 5—10 мм от ее края, меньше диаметра цилиндра примерно на 0,05—0,1 мм (см. рис. 24). Большие зазоры относятся к цилиндрам с большим диаметром. У двигателей мотоциклов М-61 и К-750 и других двигателей, имеющих такой же диаметр цилиндра, зазор составляет 0,08—0,1 мм. Диаметр юбкя поршня этих двигателей выбит на днище поршня.
У двухтактных двигателей при подборе поршня зазор измеряют или внизу юбки, или в IV поясе, под нижним поршневым кольцом. Например, у двигателей мотоциклов М-104, К-58, Ява и у других двигателей с небольшим диаметром цилиндра поршень обычно подбирают к цилиндру с зазором внизу юбки не менее 0,06—0,07 мм. Зазор между цилиндром и поршнем у мотоцикла «Ковровец-175А» измеряют на расстоянии 20 мм от нижнего края поршня. Этот зазор равен 0,06—0,08 мм для алюминиевого цилиндра с гильзами и 0,04—0,06 или — для чугунного цилиндра. При установке поршня от алюминиевого цилиндра в чугунный может произойти заклинивание поршня. При использовании поршня чугунного цилиндра в алюминиевом зазор между поршнем и цилиндром будет несколько увеличенным, что несущественно отразится на работе двигателя. При измерении зазора между поршнем и цилиндром под нижним кольцом зазор должен быть в пределах 0,13—0,15 мм. Поршни мотоцикла «Ковровец- 175А» разделены на размерные группы, обозначенные цифрами 0; 1 и 2. Цифра 0 соответствует большему диаметру, а цифра 2 — меньшему.
У двигателя мотоциклов ИЖ-56 и ИЖ «Планета» зазор между поршнем и цилиндром одинаковых размерных групп в поясе под нижним кольцом на высоте 55 мм от нижнего края юбки равен 0,06 мм. В этом случае между разрезной юбкой поршня и цилиндром нет зазора. Поршни и цилиндры двигателя маркируют цифрами 1; 0 и 00. Цифра 1 соответствует меньшему диаметру, а цифры 00 — большему. Размерная группа указана на фланце цилиндра и на головке поршня.
У двигателя мотоцикла ИЖ «Юпитер» зазор между поршнем и цилиндром одинаковых размерных групп в поясе под нижним кольцом, измеренный на расстоянии 58 мм от нижнего края юбки, равен 0,15 мм, а внизу юбки 0,4 мм. У двигателя мотоцикла «Панония» зазор между цилиндром и поршнем внизу поршня составляет 0,8 мм, над первым кольцом 0,32 мм, над третьим кольцом 0,14 мм.
Поршни и цилиндры двигателей мотороллеров, подбираемые с соблюдением тех же правил, разделены на размерные группы, обозначенные цифрами 0; 1 и 2. Цифра 0 соответствует большему диаметру, а цифра 2 — меньшему. Например, у двигателя мотороллера ВП-150 цилиндр с обозначением 0. имеет диаметр 57,02—57,01 мм, а поршень с таким же обозначением — диаметр 56,92 мм, т. е. между поршнем и цилиндром имеется зазор 0,1 мм. У двигателя мотороллера Т-200 цилиндр с обозначением 0 имеет диаметр 62, 02—62, 01 мм, а поршень с таким же обозначением — диаметр 61,96—61,95 мм; таким образом, зазор между цилиндром и поршнем составляет 0,6 мм.
Указанные выше зазоры, устанавливаемые заводом, нужно стремиться выдержать и при ремонте. Однако, если трудно точно подобрать поршень к цилиндру, то допускается увеличивать или уменьшать установленный зазор на 0,01— 0,03 мм, в особенности при комплектовании двигателя с допустимым износом цилиндра. Важно только при меньшем зазоре во время обкатки двигателя строго придерживаться всех правил обкатки, чтобы не допустить заклинивания поршня в цилиндре.
При износе юбки во время работы двигателя слышен стук поршня о стенки цилиндра, увеличивается расход масла и ухудшается компрессия вследствие плохого прилегания колец к зеркалу цилиндра. В двухтактных двигателях, кроме того, неплотно закрываются газораспределительные окна и уменьшается компрессия в картере, из-за чего резко ухудшается продувка, затрудняется пуск двигателя и снижается его мощность. Срок службы изношенного поршня путем установки новых колец можно продлить только на короткое время, так как в этом случае износ колец происходит быстрее.
Перед установкой поршня, осматривая его боковую поверхность, проверяют, не работал ли поршень в цилиндре с перекосом (рис.37). Эта неисправность часто является следствием перекоса втулки поршневого пальца, неумело обработанной разверткой, или искривления шатуна. Шатун искривляется при неосторожной выпрессовке и запрессовке поршневого пальца, а также в том случае, если двигатель переносят с места на место, держа за шатун.
При установке поршня нужно соблюдать определенные правила. У четырехтактных двигателей поршни с разрезной юбкой (при отсутствии указаний завода-изготовителя) устанавливают разрезом к передней менее нагруженной стенке цилиндра. У двухтактных двигателей на головке поршня имеются стрелка и надписи, указывающие расположение поршня в цилиндре. При установке поршня на двигатель мотоцикла ИЖ «Планета» стрелка, выбитая на головке поршня, должна быть направлена вперед, а при установке поршня на двигатель мотоцикла ИЖ «Юпитер» — назад. В случае несоблюдения этих указаний возможны западание концов поршневых колец в окна цилиндра и поломка колец при движении поршня (см. рис. 23).
Замена поршневого пальца и его втулки.
При нормальном износе двигателя ослабление посадки поршневого пальца в бобышках поршня и образование зазора между пальцем и втулкой в шатуне происходят одновременно с износом поршня. Поэтому желательно поршень, палец и втулку заменять одновременно. Однако если новый палец в старой втулке можно установить достаточно плотно, то втулку не меняют. На поршневых пальцах и бобышках поршня завод ставит цветные метки. При комплектовке палец и поршень должны иметь метки одинакового цвета.
При замене втулки 2 (рис. 38) верхней головки шатуна 1 ее выпрессовывают и запрессовывают или в тисках 5 с помощью оправки 3 и отрезка трубы 4 (рис. 38, а) или посредством вспомогательного болта 6 с гайкой и шайбой 7 (рис. 38, б). При подгонке пальца ко втулке надо учесть следующее.
Вследствие нагревания поршня при работе двигателя посадка пальца в бобышках ослабевает. Поэтому палец следует устанавливать более плотно в бобышках поршня и менее плотно — во втулке шатуна. Если этого не удается добиться подбором пальца, то втулку слегка развертывают раздвижной разверткой. При использовании простой развертки для точной подгонки можно на ее грани на V3 окружности наложить полоску тонкой бумаги. Развертка прорежет бумагу, но все же снимет во втулке небольшую стружку. Поршневой палец, смазанный маслом, должен легко вдвигаться во втулку шатуна при слабом нажиме большого пальца. Более тугая посадка или покачивание пальца во втулке недопустимы. В бобышки поршня палец должен вдвигаться с усилием. Желательно установить палец с натягом 0—0,002 мм. В этом случае палец, нагретый до температуры 20° С, можно вдвинуть в обе бобышки поршня сильным нажатием пальца руки. При такой посадке поршневой палец перемещается в осевом направлении, но не вращается. Если нагретый до указанной температуры палец можно вдвинуть в бобышки, только смазав маслом (или в крайнем случае при нагревании поршня до температуры 40° С), то натяг равен примерно 0,004 мм. При повторной выпрессовке и запрессовке сухого пальца нарушается точность подгонки его к поршню.
Туго сидящий в поршне палец лучше выпрессовывать посредством хомута с винтом (рис. 39). При выполнении этой операции с помощью молотка и оправки 1 поршень надежно подпирают массивным деревянным бруском 3. Для облегчения установки пальца поршень предварительно нагревают в кипящей воде. Отверстия в бобышках поршня 5 и во втулке шатуна 4 совмещают, продевая в них оправку 6. Вторым концом оправку вставляют внутрь поршневого пальца. В нагретый поршень палец входит легко только до тех пор, пока он не нагреется; поэтому слегка смазанный маслом палец вталкивают в поршень возможно быстрее.
Замена кривошипа.
Неразборный кривошип при обнаружении износа подшипника шатуна (см. раздел «Определение износа деталей, расположенных в картере») желательно заменить новым кривошипом. Однако при наличии необходимых запасных частей, токарного станка, индикатора и пресса изношенный подшипник шатуна можно восстановить, не обращаясь к услугам мастерской. Эту работу может выполнить квалифицированный механик; поэтому ниже приводятся рекомендации только относительно некоторых важнейших особенностей ремонта кривошипа.
В случае износа кривошипа, при работе которого слышен стук, не следует эксплуатировать мотоцикл. На поверхностях кривошипного пальца и шатуна при этом образуются повреждения от наклепа и выкрашивания, которые не удается устранить шлифованием. Ролики также нельзя больше использовать.
Кривошип можно распрессовать небольшим прессом или специальным съемником. На рис. 40 показан съемник, изготовленный на токарном станке и предназначенный для разборки кривошипов двигателей М-61 и ему подобных. Съемник надевают на съемочные выступы наружной щеки кривошипа так, чтобы винт (диаметром 27 мм, шаг резьбы 3 мм) упирался в кривошипный палец. Съемник закрепляют в больших тисках или приваривают к стальной балке. Под винт съемника надо подложить шайбу и густо смазать ее и резьбу универсальной среднеплавкой смазкой (солидолом). При завинчивании винта съемника надо пользоваться длинным воротком. Для выпрессовки кривошипа двухтактного двигателя можно обойтись без подобного съемника и пользоваться прессом.
При сборке коленчатого вала двигателя типа М-61 на прессе можно прежде запрессовать кривошипные пальцы цилиндрическими концами в среднюю щеку и затем напрессовать на конусные концы крайние щеки, обеспечивая осевое перемещение шатуна между щеками в пределах 0,04—0,14 мм. Центрирование коленчатого вала производят в центрах токарного станка с помощью индикатора. Биение коренных шеек на длине 20 мм не должно превышать 0,05 мм.
Если шейки параллельны, но не соосны, то их положение выравнивают ударами алюминиевого молотка по щекам (рис. 41, б), а если расположены под углом, то сжимают в тисках (рис. 41, а).
У кривошипа одноцилиндрового двухтактного двигателя М-103 и ИЖ «Юпитер» биение шеек на длине 20 мм не должно превышать 0,02 мм, у двигателей ИЖ 56, ЙЖ «Планета» — не более 0,03 мм.
При установке новых шатуна, пальца и роликов необходимо, чтобы радиальный зазор в подшипнике шатуна двигателя мотоцикла М-61 был равен 0,01—0,02 мм (причем шатуны с подшипником правого и левого цилиндров должны иметь одинаковую массу), двигателей мотоциклов М-103 — не более 0,012 мм и двигателей мотоциклов ИЖ-56, ИЖ «Планета», ИЖ «Юпитер» — не более 0,016 мм. При незначительном увеличении радиального зазора срок службы роликоподшипника шатуна немного уменьшится; в результате сборки без зазора роликоподшипник может разрушиться в течение первых часов работы двигателя. Кроме того, следует обеспечить правильный осевой зазор роликов подшипника. В противном случав ролики будут притормаживаться с торца и скользить (а не катиться), вследствие чего на них образуются лыски и подшипник выйдет из строя.
Диаметры роликов не должны отличаться один от другого более чем на 0,002 мм. Так точно измерить диаметр роликов вне заводских условий нелегко. Поэтому надо проверить размеры роликов в комплекте микрометром, чтобы не допустить большого отклонения в размере отдельных роликов. Даже при наличии в комплекте одного ролика, диаметр которого значительно больше диаметра остальных роликов, подшипник при работе выйдет из строя. Следует обращать внимание на качество шлифования новых роликов и на формы роликов, бывших в употреблении, на наличие и полировку закругления перехода цилиндрической части в торец.
В случае отсутствия запасных частей умеренно изношенные кривошипный палец и отверстие в шатуне иногда восстанавливают шлифованием на станке или с помощью притира и устанавливают ролики увеличенного диаметра. При отсутствии запасной сменной втулки нижней головки шатуна, например у двигателей типа М-72, можно расточить головку (лучше отшлифовать) шатуна и установить в нее кольцо толщиной 2,5—3 мм, сделанное из стали 12ХНЗА и подвергнутое цементации и закалке. Кроме того, можно использовать внутреннее кольцо шарикоподшипника (сталь- ШХ15) соответствующего внутреннего диаметра (50 мм), отшлифовав его снаружи под размер шатуна. При запрессовке кольцо охлаждают сухим льдом, а шатун подогревают.
Замена, растачивание цилиндра и установка в него гильз.
Цилиндр заменяют новым; растачивают под поршень увеличенного размера или вставляют в него гильзу, если износ верхней части зеркала составляет примерно 0,15— 0,2 мм, а также при образовании на нем задиров и рисок. Вследствие износа зеркала цилиндр становится конусным (вверху шире, внизу уже) и овальным (вытянутым по оси, обычно перпендикулярной к поршневому пальцу). Увеличенный износ верхней части цилиндра — следствие высокой температуры и недостаточной смазки этой части цилиндра. Овальность получается в результате большего. воздействия поршня на переднюю и заднюю стенки. Образование овальности вызывается также смыванием смазки с зеркала потоком смеси из карбюратора, деформацией и местными перегревами цилиндра.
Износ цилиндра определяют, измеряя его с помощью нутромера с индикатором. Приближенно конусность цилиндра можно определить с помощью поршневого кольца и щупов, измеряя зазор в замке кольца, которое последовательно устанавливают в верхнем неработающем поясе цилиндра, ниже, в месте наибольшего износа, в средней и нижней частях цилиндра.
Нормальную компрессию нельзя восстановить путем установки в изношенный цилиндр нового поршня и колец, так как поршень и кольца не могут хорошо приработаться к зеркалу овального сечения. В особенности плохо прирабатываются хромированные кольца. Их не следует ставить в изношенный цилиндр. Изношенный цилиндр растачивают и шлифуют до размера, соответствующего ремонтному размеру поршня. Для таких цилиндров заводы выпускают поршни ремонтных размеров.
При правильной установке гильзы в изношенный цилиндр износостойкость зеркала повышается. Например, для цилиндров диаметром около 78 мм можно использовать гильзы из специального чугуна от двигателя автомобиля «Москвич-407; отличающиеся высокой износостойкостью (необходимость шлифования их возникает примерно через 100000 км пробега). Для облегчения установки гильзу следует охладить искусственным льдом, а цилиндр нагреть в кипящей, воде. Чтобы установить гильзу из чугуна СЧ 24- 44 в цилиндр, изготовленный из алюминиевого сплава АЛ108 (двигатель мотоциклов «Ковровец-175А» и др.), его нагревают до 220—250° С, а затем запрессовывают гильзу с натягом 0,08—0,2 мм. При установке гильзы в цилиндр необходимо учесть следующее. Проникновение масла между гильзой и цилиндром резко ухудшает охлаждение. В случае установки даже с зазором гильза не будет перегреваться, так как она при нагревании расширяется, вследствие чего зазор устраняется кроме того, при этом лучше сохраняется цилиндрическая форма гильзы.
bike78.narod.ru