Бронешлем – эволюция развития. Современные шлемы
Современные бронешлемы - защитные структуры и технологии изготовления
12:44 / 11.03.12

Индивидуальная защитная экипировка бойца на поле боя используется уже не одну тысячу лет и ее компоненты хорошо известны историкам и археологам, изучены до малейших подробностей. Испокон веку важнейшей частью боевой защиты считается бронешлем (БШ). Конструкция и геометрическая форма БШ менялась со временем в зависимости от постоянного совершенствования оружия и средств поражения, от которых надо было защитить человека. Однако, материал, из которого изготавливали корпус БШ - его главную конструктивную часть, практически не менялся на протяжении многих веков. Этим материалом был гомогенный тонкий листовой металл - сначала медь и бронза, потом железо и сталь. До начала 80-х годов XX века только стальные БШ использовались во всех армиях мира. В этой статье специально для ИА "Оружие России" сотрудники НИИ "Стали" Д.Купрюнин, А.Егоров и Е.Чистяков рассматривают некоторые аспекты, относящиеся к современным материалам и конструкциям БШ.
Главнейшая задача БШ, сформулированная военными ведущих мировых держав, состоит в защите головы бойца от самого массового на поле боя фактора поражения - осколков естественного дробления осколочно-фугасных снарядов, мин и гранат, а также защите черепа от ударных нагрузок.
В середине XX века, когда были проанализированы результаты 1-й и 2-й мировых войн и последующих локальных конфликтов (в Корее и Вьетнаме), стало очевидно, что стальной гомогенный БШ не может обеспечить защиту головы бойца от наиболее массовой части спектра осколочного потока поражения на современном поле боя. Уровень его противоосколочной стойкости (ПОС) был весьма низок и не превышал V50%= 300-350 м/с для осколка массой 1г (50%-ная вероятность непробития корпуса БШ).
Надо сказать, что сделать защиту с более высокой ПОС можно только за счет увеличения толщины корпуса БШ, что сразу "приведет" к существенному увеличению носимой на голове массы. Так, например, чтобы поднять ПОС стального БШ с V50%= 300м/с до V5o%= 600 м/с надо почти удвоить толщину корпуса с 1,6мм до 2,5мм, что при физической плотности стали рст=7,85 г/см3 приведет к увеличению массы корпуса БШ с 1500г до 2350г.
Это недопустимо, т.к. существуют медико-технические ограничения по величине допустимой носимой массы БШ, которые предписывают максимальный предел для общевойскового БШ в 1600г. Такое ограничение обусловлено тем, что опытно-экспериментальным путем медиками была определена возможность получения тяжелой травмы шейного участка позвоночника человеком при превышении носимой распределенной массы БШ на голове сверх 1600г.
Таким образом, на рубеже 60-х - 70-х г.г. XX века появилась задача создания низкоплотных полимерных материалов, обладающих соизмеримым с высокопрочной сталью пределом прочности, которые пришли бы на замену стальному листовому прокату в производство БШ и позволили бы значительно повысить ПОС корпуса без увеличения его массы.
Кроме того, полимерные материалы, ввиду своих физико-механических свойств, лучше поглощают и рассеивают ударно-волновую энергию взаимодействия средства поражения с защитной структурой преграды, чем гомогенная высокоуглеродистая сталь.

Такой материал был впервые разработан американской фирмой «Dupont» и был назван «параарамидным волокном», имевшим предел прочности такой же, как у конструкционной стали, а физическую плотность рар.=1,43 г/см3, что более чем в 5 раз легче стали. Из параарамидного волокна сделали нить линейной плотности 110 текс. (масса нити в граммах на 1000м длины), которая получила торговую марку «Kevlar®29», и соткали полотно удельной массой 255 г/м2.
Из этой ткани была изготовлена квазигомогенная многослойная тканево-полимерная структура, которая в эквивалентной массе с гомогенной монолитной сталью показала вдвое более высокую ПОС и существенно меньший динамический прогиб композиции при взаимодействии с имитатором стандартного осколка и пистолетной пулей 9мм калибра. Первый в мире тканево-полимерный шлем появился в США.
Его разработала Натикская научно-исследовательская лаборатория Армии США в конце 1970-х годов. В начале 1980-х годов он был принят на вооружение сухопутных войск. Шлем получил название Personnel Armor System, Ground Troops (PASGT). Он был выполнен из ткани на основе волокна Kevlar®29 и связующего - фенольной или PVB смолы.
Масса БШ составляла 1,4 (3,1 фунта) -1,9 кг (4,2 фунта)} имел 5 типоразмеров - XS, S, M, L, XL. Уровень ПОС шлема определялся военным стандартом MIL-STD-662E, полицейским NIJ 0106 и составлял V50% = 600м/с по стандартному осколку STANAG 2920, что примерно соответствует уровню в V50%=570...580 м/с по стальному шарику массой 1,03 г, которым испытываются все российские шлемы. Противоударные характеристики регламентированы стандартом MIL-h54099A.
Технология изготовления этих шлемов достаточно проста. Ткань, пропитанную полимерным связующим, проще говоря, смолой, укладывают в несколько слоев в форму. Полученную заготовку прессуют при определенной температуре, связующее полимеризуется, твердеет. От прессованной оболочки обрезают облой, устанавливают подтулейное устройство - шлем готов,
Так как ткань, пропитанную смолой; называют «препрегом», то и технология изготовления шлемов получила название «препреговой». Основное преимущество этой технологии - простота и малая зависимость конечного результата от точности соблюдения режимов прессования. Поэтому достаточно быстро шлемы, аналогичные PASGT, начали выпускаться во многих странах.
За 30 лет произведено несколько миллионов штук шлемов типа PASGT, он принят в качестве основного в НАТО и до сих пор используется Армией США. В армиях многих стран по всему миру используется или этот шлем или его аналоги. Количество фирм-производителей шлемов типа PASGT перевалило за несколько сотен. Соответственно и разброс характеристик этих шлемов, как по массовым, так и по защитным характеристикам достаточно велик.

Хотя в целом шлем удовлетворял требованиям военных, работы по его совершенствованию были начаты уже в конце 90-х годов. Работы эти были инициированы началом реализации во многих странах мира программ по оснащению бойца будущего столетия. Этими программами боец и его экипировка рассматриваются как единая система, которая, взаимодействуя с другими системами, должна максимально эффективно выполнять боевую задачу.
Средства защиты, и шлем в частности, принимаются программой как элемент, который кроме выполнения защитных функций должен комплексироваться с другими элементами системы. Практически все программы «Боец будущего» рассматривают шлем как платформу для установки приборов ночного видения, связи, навигации, дисплеев для самоконтроля и информационных функций, что неминуемо приводит к увеличению массы, нагружающей голову.
Поэтому еще в 1996 году МО США была выдвинута двухгодичная программа SEP (Soldier Enhancement Program - Программа повышения боевых возможностей солдата), в рамках которой должна была быть разработана и испытана каска с более легкой основой. В качестве цели была поставлена задача снизить вес шлема на 25%.
Однако реализовать эти цели зарубежным разработчикам удается с большим трудом. Основная причина кроется как раз в созданной и эксплуатируемой ими технологии. Уже давно стало ясно, что баллистическая ткань наиболее эффективно работает, когда ее отдельные нити имеют возможность при упругой деформации растягиваться, достигая предела текучести, что происходит при максимальных нагрузках на материал.
Ткань сама по себе уже ограничивает эластичность нитей и от типа плетения стойкость ткани может существенно меняться. Если же ткань пропитать смачивающим клеевым составом и превратить в жесткий композит, то баллистические характеристики такого композита будут хуже, чем у эквивалентного по массе ничем не связанного тканевого пакета.
Тем не менее, применяя новые, более эффективные, чем Kevlar®29 материалы, зарубежным разработчикам удалось на 10-15% снизить и массу шлема и поднять его ПОС. Так, применение нового усовершенствованного арамидного волокна «Kevlar® KM2» и изготовление из него нитей более низкой линейной плотности (44текс, 67текс.) позволило снизить вес шлема на 8-10%.
Дальнейшие исследования по снижению веса привели к разработке и принятию на вооружение армии США в 2002 г новой, также арамидной, каски АСН (Advanced Combat Helmet), имеющей ещё меньший вес. Правда, снижение веса обеспечивалось, в основном, уменьшением на 8 % площади защиты, но разработчикам удалось увеличить на 6% ее ПОС.
Усиленно работает над проблемой снижения массы шлема и бывший разработчик шлема PASGT- исследовательская лаборатория NATICK. Так, в настоящее время она исследует два новых материала, которые могут решить проблему снижения веса. Один из них - известный материал «Zyion». Используя этот материал, фирме удалось получить шлем массой всего в 800 г. (1,79 фунт).
Однако, этот материал оказался нестойким к воздействию солнечного света, воды и потому непригодным для использования в шлемах. Сейчас фирма исследует новый материал на основе волокна М5, разработанного фирмой Magellan Systems Int. Расчеты показывают, что при том же уровне защиты использование материала М5 позволит уменьшить массу шлема на 35 %. Однако, пока американский солдат воюет в шлеме, масса которого не менее 1,3-1,5 кг, а ПОС не превышает 680-700 м/с по STANAG-2920.

Россия значительно позже многих зарубежных стран начала думать о замене стальной каски CLU-68 на тканево-полимерную, хотя работы по созданию такой каски начались в НИИ Стали в инициативном порядке еще с середины 80-х годов. Разработчики института начали осваивать принципиально другую технологию -технологию термопластичного прессования квазигомогенных многослойных пленочных структур, или - как ее часто сейчас называют - «пленочную» технологию.
Суть ее проста - слои баллистической ткани прокладываются тонкой термопластичной пленкой. Затем пакет закладывается в прессформу, нагревается, прессуется и охлаждается. Пленка расплавляется и соединяет слои ткани. После охлаждения получается жесткая гомогенная оболочка корпуса шлема. По расчетам разработчиков пленка, размягчаясь, не смачивает нити ткани, оставляя им практически полную свободу предельной упругой деформации, а значит, стойкость такой композиции должна быть выше, чем у эквивалентного по массе препрега.
Практика показала, что расчет был верен. Правда, чтобы прийти к желаемому результату институту потребовалось почти 10 лет. Именно столько шла отработка промышленной высокопроизводительной технологии получения шлемов требуемого качества. Зато у разработчиков появилось широкое поле для оптимизации композиции. Варьируя набором тканей в лицевых и тыльных слоях, меняя толщину и материал пленочного связующего можно было подобрать наиболее оптимальный вариант для заданных условий.
В 1999 году первый серийный шлем, произведенный в НИИ Стали под индексом «6Б7», поступил в вооруженные силы российской армии. По своим характеристикам он сразу же превзошел свой зарубежный аналог: масса - не более 1,3-1,35 кг, противоосколочная стойкость -560 м/с, что соответствует 600-610 м/с по STANAG.

К 2005 году НИИ стали разработал и сдал на вооружение еще 3 модели шлемов - 6Б26, 6Б27 и 6Б28. Все они являлись и до сих пор являются рекордсменами по массе и стойкости. Оптимизируя состав пакета, НИИ Стали удалось создать шлем массой не более 1,1 кг с ПОС выше 700 м/с (по STANAG - 730-740 м/с), причем не в опытном экземпляре, а в серийном производстве. Это прототип конструкции общевойскового БШ 2-го поколения.
Естественно, столь высокие характеристики шлема были достигнуты соответственной ценой. Так, жесткие требования предъявляются к качеству используемой баллистической ткани, малейшее отклонение от паспортных характеристик отправляет ткань в брак. Технология допускает использование в пакетах только цельных кусков, тогда как в препреговой технологии можно использовать пакеты, набранные из кусков баллистической ткани.
Это приводит к увеличению расхода дорогостоящей ткани и, соответственно, стоимости конечного продукта. Сам процесс прессования тоже требует большего времени, чем в препреговой технологии, поскольку контролируемый нагрев заготовки и ее охлаждение происходят непосредственно в прессовой оснастке. Правда своими последними работами разработчики НИИ Стали показали, что резервы в оптимизации этой технологии есть и они не малые.
Найдены решения по сокращению цикла нагрева и охлаждения заготовки. Не следует забывать еще ряд важных моментов. Поскольку пленочная технология не использует вредных смол, она на порядок экологически чище, что проявляется как в производстве, так и при эксплуатации шлема. Да и для организации крупносерийного производства пленочная технология прогрессивнее препреговой, поскольку позволяет автоматизировать процесс сборки тканево-полимерных пакетов для прессования, тогда как в препреговой технологии эта операция выполняется вручную.
Следуя из вышесказанного, и зарубежная, и отечественная конструкция тканево-полимерного БШ используют в качестве защитной структуры многослойную квазигомогенную композицию на основе высокопрочной арамидной ткани и полимерного термореактивного или термопластичного связующего, которое скрепляет слои ткани по всей толщине структуры и заставляет работать корпус БШ как сплошную высокопрочную упругую оболочку - «полимерную броню».

Очень важно отметить тот факт, что сплошная гомогенная оболочка корпуса позволяет оптимально использовать физико-механические свойства материалов структуры, а именно: рассеивать ударную волну, образованную импульсом проникающего высокоскоростного средства поражения, и формируемую ей волну упругой деформации композитного материала, обеспечивая допустимые значения величины динамического прогиба оболочки.
Величина динамического прогиба оболочки корпуса БШ при непробитии защитной структуры является определяющим фактором запреградного контузионного воздействия на голову человека. Поэтому максимально допустимая величина динамического прогиба оболочки всегда определяется в ходе государственных испытаний образцов БШ с помощью рентгеноимпульсной установки в реальном масштабе времени.
Кроме технологии пленочного термопласта, используемой для создания гомогенных сплошных оболочек корпусов БШ, в России была разработана «смешанная» технология, которая включает элементы препреговой технологии в сочетании с «сухими» слоистыми тканевыми арамидными пакетами. При этом наружные тканевые слои защитной структуры пропитываются полимерным термореактивным связующим, а внутренние слои остаются сухими.
Такая структура получила название от своих разработчиков (ЗАО ЦВМ «Армоком») - «дискретно тканевая структура» (ДТС). Начиная с 2000г. российские ВС заказывают тканево-полимерные БШ, изготавливаемые и по пленочной технологии и по технологии ДТС примерно в одинаковых количествах. Только в 2010 - 2011 гг. их было произведено и поставлено в армию около 70 000 шт. Причем, боевые защитные и эксплуатационные характеристики гомогенного и дискретно-тканевого БШ абсолютно одинаковы, цена обоих образцов единая.
В чем же различие? А различие БШ как раз и кроется в составе структуры полимерной защитной композиции, получаемой в результате альтернативных технологических процессов прессования оболочек корпуса. В случае использования пленочного термопласта, как уже было отмечено, получается гомогенная сплошная структура оболочки и процесс взаимодействия средства поражения с такой преградой в общем лежит в плоскости классической теории прочности и упругости материалов.
Корпус БШ, полученный по технологии ДТС, имеет выраженную гетерогенную структуру в состав которой входят две внешние относительно твердые и тонкие оболочки, придающие жесткость всей конструкции, и сухой слоистый пакет арамидной ткани, расположенный между оболочками. Такая структура называется «разнесенной», т.к. более высокоплотные слои находятся на расстоянии друг от друга, а между ними располагается низкоплотный материал.
Разнесенная схема защитной структуры имеет свои преимущества. Например, более эффективное поглощение и рассеивание ударной волны за счет наличия границ раздела между разноплотными слоями материалов композиции. Но это преимущество достигается большей толщиной комбинированного корпуса БШ с ДТС - до 15мм, в то время, как толщина гомогенного пленочного корпуса в самой массивной подтулейной зоне не превышает 8мм.

Но кроме этого преимущества больше никаких защитных выгод технология ДТС не дает, не говоря уже об относительно низкой производительности изготовления таких конструкций, прежде всего, за счет большой доли ручного труда, применяемого при сборке тканевого пакета. Вместе с тем, ДТС имеет один существенный недостаток - слишком малую толщину жестко-упругой внутренней оболочки корпуса БШ, задача которой состоит в том, чтобы за счет поглощения энергии упругой деформации сухого тканевого пакета сократить величину динамического прогиба полимерной композиции.
Но т.к. сухой тканевый пакет не связан с тонким упругим подпором из препрега, то и вся энергия упругой деформации пакета приходится на локальную зону поражения тонкой препреговой оболочки, а не распределяется равномерно послойно по всей толщине структуры, как у гомогенного тканево-полимерного корпуса. В этом случае, если в эквивалентных условиях сравнивать значения динамического прогиба двух технологически разных БШ - гомогенного и ДТС, то оказывается что для ДТС величина динамического прогиба больше, чем у гомогенного пленочного термопласта.
Вопрос: «какая из технологий более предпочтительна и прогрессивна?» находится в компетенции Заказчика, который на этапе государственных испытаний детально определил все ТТХ обоих БШ, каждого в отдельности, и допустил в серийное производство оба образца. Пока идет серийное производство тканево-полимерных БШ первого поколения можно было бы и не заострять внимание на технологических аспектах производства различных образцов, тем более, что производство ведется по действующей рабочей конструкторской документации литеры «О1», утвержденной Заказчиком,
Однако, при создании боевой экипировки 2-го поколения, Заказчик выдвинул требование о разработке единой конструкции, а значит и защитной структуры, общевойскового БШ. Становится злободневным «отложенный» Заказчиком вопрос - «Какая структура полимерной защитной композиции отвечает современным требованиям по противоосколочной и противопульной стойкостям в максимальной степени? Какая структура обеспечивает наиболее приемлемые значения запреградного контузионного воздействия?»
Совершенно очевидно, что ответ на этот вопрос Заказчик может получить только после комплексных сравнительных испытаний различных БШ, в том числе и зарубежного производства, в первую очередь медико-биологических исследований результатов динамического воздействия средств поражения на корпус БШ и голову человека. Не ответив на этот вопрос, нельзя будет принять выверенного и обоснованного решения в области боевой экипировки на длительную перспективу.
Не менее интересный материал о бронешлемах можно прочитать здесь.
www.arms-expo.ru
Бронешлем – эволюция развития | Армейский вестник

Индивидуальная защита против используемого противником оружия известна нам с очень далеких времен, и по сей день она постоянно изучается и совершенствуется. Одной из составляющей индивидуальной защиты является защитный головной убор. Форма, конструкция, геометрия и устройство его постоянно совершенствовалась, менялись названия защитного головного убора, и в наши дни он имеет название — бронешлем.
Совершенствование защитного головного убора зависело от применяемого оружия, которое имеет тенденцию совершенствоваться намного быстрее средств защиты. Однако суть бронешлема не менялась – защитный головной убор должен был максимально снизить вероятность поражения головы человека от применяемого вооружения.
Долгое время неизменным оставался материал, из которого выполняли бронешлем – тонкий гомогенный лист металла, от меди до стали. Стальные бронешлемы были основными головными защитными элементами экипировки всех вооруженных сил мира до конца прошлого столетия. Их история стала заканчиваться в 80-е годы прошлого столетия, с появлением тканево-полимерного шлема.
История создания современных бронешлемов
В наши дни задача бронешлемов не изменилась — это защита головы от применяемого вооружения, осколков различных снарядов, гранат и мин, уменьшения вероятности попадания из стрелкового оружия, а также предохранение от ударов и нагрузок. В середине прошлого столетия рост новых технологий дал возможность начать работы над низкоплотными полимерными материалами с повышенным пределом прочности в отличие от стали.
Результатом анализа военных конфликтов и мировых войн стало очевидное слабое обеспечение стальным шлемом защиты головы военнослужащего от большинства видов осколков от применяемого вооружения. Уровень ПОС – противоосколочной стойкости шлема из листовой стали, обеспечивал до 350 м/с для одного осколка в 1 грамм (условно), пробивающего корпус бронешлема с 50-процентой вероятностью. Это условная мера, принятая для проведения оценивания ПОС.
Улучшение ПОС стальных шлемов приводило лишь к увеличению их массы которую приходилось бы носить военнослужащим на голове. К примеру, для увеличения стандартного ПОС стального шлема вдвое, до 600 м/с, необходимо увеличить толщину стального листа почти вдвое, что увеличивало вес БШ на 700 грамм до 2,35 кг. Но тут всплывает другая проблема: проведенные эксперименты по ношению шлемов выявили их предельный вес -1,6 кг. Превышение данного веса резко увеличивало возможность получения тяжелых травм шейного позвоночника.
В начале второй половины прошлого века шли изыскания по созданию шлемов из различных материалов. Успешные результаты создания полимерных материалов с низкой плотностью и высоким пределом прочности дали возможность использовать такие материалы в различных сферах человеческой деятельности.
Основной же сферой применения стала возможность замены стальных листов и частей в военной сфере. Как выяснилось, полимерный материал к тому же обладает лучшими физико-механическими свойствами по поглощению и рассеиванию ударно-волновой энергии применяемых средств нападения, чем шлемы из стальных листов.
Первые разработки
Первыми добились успеха конструкторы американской компании «Dupont». Полученный материал получил название параарамидное волокно. Материал по прочности соответствовал конструкционной стали, его физплотность равнялась 1,43 г на куб.см. – шлем из такого материала весил в пять раз меньше стального.
Запатентованная торговая марка параарамидного волокна — Kevlar®29. Из данного волокна выделывали нить, обладающей линейной плотностью в 110 текс и создавали полотно с удельной массой 255 г на кв.м. Из полотна изготавливали квазигомогенную тканево-полимерную многослойную структуру, которая при одинаковом весе с монолитной гомогенной сталью показывает улучшенные вдвое характеристики ПОС.
Кроме того, при воздействии осколков или пули калибра 9-мм заметен намного меньший динамический прогиб под ними. Первыми, кто создал «тканевый» шлем, стали Соединенные Штаты Америки. Шлем спроектировали и создали в Натикской НИЛ СВ в 70-х годах. На вооружение Соединенные Штаты принимают «тканевый» шлем в начале 80-х годов, под названием «PASGT» — Personnel Armor System, Ground Troops.
Технология создания PASGT
Бронешлемы создавали из ткани, в основе которой использовали Kevlar®29 и фенольную или PVB смолы. Вес БШ – 1,4-2,9 кг в зависимости от назначения. Серийные бронешлемы имели 5 размеров XL/S/M/L/XL. Характеристики ПОС определялись военными и полицейскими стандартами.
Военный MIL-STD-662E и полицейский NIJ 0106 соответствовали до 600 м/с для осколка стандарта STANAG 2920 пробивающего корпус бронешлема с 50-процентой вероятностью. Этот стандарт приблизительно равен российскому стандарту при испытаниях отечественных моделей бронешлема.
Само изготовление шлемов довольно простое – материал пропитывают смолой и несколькими слоями укладывают форму. Фому опрессовывают под необходимой температурой. Смола полимеризуется и затвердевает. Затвердевшую оболочку обрезают облой. После этого, оболочка получает подтулейное устройство и процесс создания шлема завершен. Такой метод изготовления называется метод препрегов, от названия ткани, пропитанной смолой (препреги). Простота такой технологии привела к широкому изготовлению и распространению аналогичных шлемов во многих государствах.
По сегодняшний день было изготовлено несколько миллионов шлемов PASGT или их аналогов, почти все ВС стран блока НАТО обеспеченны «тканевыми» шламами. В Соединенных Штатах сухопутные подразделения до сих пор экипируются шлемами PASGT. ВС других стран также имеют в своей индивидуальной экипировке подобный шлем собственного или зарубежного производства. Поэтому характеристики БШ тканевого изготовления разных стран могут существенно отличатся друг от друга.
Современные разработки бронешлемов – США
Все современные разработки во многих странах идут по программам оснащения бойца будущего. Основой таких программ является единая система по обеспечению эффективного выполнения поставленной задачи. Единая система – полное взаимодействие всех систем экипировки между собой для их эффективного применения носителем.
Хоть программы каждого государства и отличаются между собой, БШ в них во всех стал «носителем» различного вспомогательного и дополнительного оборудования, типа ПНВ, средств навигации и связи, информационных дисплеев различной направленности, видеокамер и спецоборудования. Все эти решения привели к повышению носимого на голове веса. Пентагон в 1996 году разработал программу «повышения боевых возможностей солдата». По ней было необходимо создать шлем на более легкой основе с конечной массой 75% PASGT.
Реализация программы проходила с большими трудностями. Основная причина крылась в используемых технологиях. В итоге, используя для создания ткани новые современные технологии, удается снизить вес БШ до 15%, и немного поднять ПОС. Для создания БШ использовали улучшенное арамидное волокно Kevlar® KM2, линейная плотность получаемых нитей снизилась в 2 раза. В 2002 году Соединенные Штаты принимают на вооружение бронешлем «Advanced Combat Helmet» малого веса. Этого удалось добиться сокращением на 8% площади защиты, но, правда, улучшились на 6% характеристики ПОС.
Современные разработки бронешлемов – Россия
Российская Федерация в вопросе замены шлемов из листовой стали на тканево-полимерные отстала от западных конкурентов. Но разработки «тканевых» шлемов начались, правда, по собственной инициативе, еще в 80-е годы в НИИ Стали. Советский Союз освоил иную технологию производства шлемов – термопластичное прессование многослойных квазигомогенных пленочных структур, получившую упрощенное название «пленочная».
Технология создания российских плёночников
Суть технологии так же не очень сложная – между слоями баллистической ткани прокладывают тонкую термопластичную пленку. Потом, полученный пакет помещают в углубленную пресс-форму, в которой пакет нагревают, прессуют и охлаждают. Термопластическая пленка при нагревании плавится и соединяет между собой два слоя ткани. Так создается оболочка российского шлема.
Такая технология позволила добиться стойкости шлема больше чем американские препреги. До реализации данной технологии НИИ Стали шел целое десятилетие. Но теперь, благодаря тому, что технология досконально изучена, путем замены ткани, толщины ткани и «пленки», можно подобрать необходимый вариант исполнения бронешлема.
Первый российский тканевый пленочной шлем поступает на вооружение России в 1999 году под индексом 6Б7. Пленочник сразу обходит по характеристикам зарубежный аналог:— максимальная масса 6Б7 не превышает минимальную массу PASGT;— ПОС 560 м/с, что по STANAG – 610 м/с.
В 2005 году у ВС России появились еще 3 модели БШ – 6Б28,6Б27, 6Б26. Они на данное время являются лучшими по характеристикам БШ в мире. Последняя новинка от НИИ Стали – общевойсковой шлем 2-го поколения готовый пойти в серийное производство. Шлем имеет вес не более 1,1 кг, ПОС по STANAG до 740 м/с.
Как не жаль, но достижение таких характеристик не обошлось без увеличения цены. Малейшие отклонения в характеристиках баллистической ткани сразу означает брак. В пакеты отбираются только целые куски ткани, в отличие от американской технологии. Все это привело к подорожанию конечного продукта – бронешлема. Из плюсов технологии – высокая экологичность (не используются смолы) и автоматизация производства.
В России есть еще одна технология создания БШ – смешанная или дискретно-тканевая структура (ДТС). Разработчик компания «ЦВМ Армоком». Смысл технологии использование элементов препреги и сухих арамидных слоистых пакетов. В пакетах только наружные слои ткани пропитывают смолой, а внутренние остаются сухими. Такая структура создания называется разнесенной.
Положительный момент такого способа – более эффективное рассеивание и поглощение ударных волн, который достигается большой толщиной корпуса бронешлема – до 1,5 сантиметров. Для сравнения – пленочный бронешлем имеет толщину не более 0,8 сантиметра. Отрицательный момент смешанной технологии – малая толщина внутренней жесткоупругой оболочки. Динамический прогиб у данного бронешлема больший, чем у бронешлема изготовленного по пленочной технологии.
Открытый вопрос экипировки российского солдата будущего
С 2000 года российские военнослужащие получают бронешлемы выполненные по пленочной и смешанной технологиям приблизительно в равном количестве. Все характеристики и цена у них практически одинаковы. По опубликованным данным известно, что в 2010-11 годах ВС РФ получили 70 тысяч бронешлемов созданных по этим технологиям.
еперь же перед выходом БШ 2-го поколения в серийное производство, как и всей экипировки 2-го поколения, военное ведомство выдвигает требования к ее созданию – единая система. Это приведет к тому, что в России останется только одна технология создания БШ, и кто из них более будет соответствовать выдвинутым требованиям, сможет определить только сам заказчик при проведении комплексных испытаний единой системы 2-го поколения.
Недалекое будущее БШ — нанотехнологии
Американские и российские конструкторы «NATICK» и НИИ Стали разрабатывают новые технологии создания бронезащиты. Американцы проводят исследования двух новых материалов созданных при помощи нанотехнологий –«Zyion» и волокно фирмы «Magellan Systems Int» М5.
Первый материал позволил создать шлем весом около 0,8 кг, но материал пока неустойчив к воде и солнечному свету. Волокно при использовании поможет снизить вес американского шлема почти на треть, пока ведутся исследования.
Российские специалисты создали материал который увеличил ПОС, уменьшил динамический прогиб, но материал тоже на данное время «боится» воды. Технология носит название жидкой брони.
/Роман Джерелейко, topwar.ru/
army-news.ru
Современные бронешлемы – защитные структуры и технологии изготовления
В этой статье будут рассмотрены некоторые аспекты, относящиеся к современным материалам и конструкциям БШ.
Конструкция и геометрическая форма БШ менялась со временем в зависимости от постоянного совершенствования оружия и средств поражения, от которых надо было защитить человека. Однако материал, из которого изготавливали корпус БШ - его главную конструктивную часть, практически не менялся на протяжении многих веков. Этим материалом был гомогенный тонкий листовой металл - сначала медь и бронза, потом железо и сталь. До начала 80-х годов XX века только стальные БШ использовались во всех армиях мира.
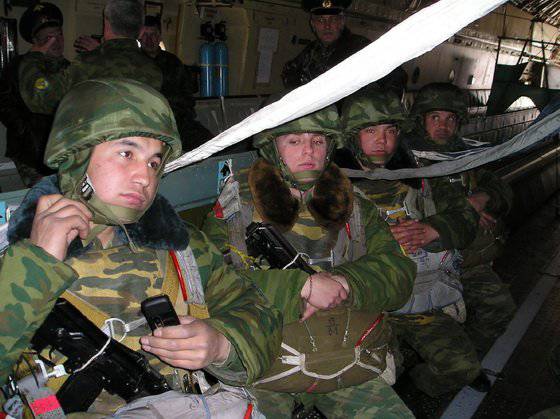
Бойцы в бронешлемах
Главнейшая задача БШ, сформулированная военными ведущих мировых держав, состоит в защите головы бойца от самого массового на поле боя фактора поражения - осколков естественного дробления осколочно-фугасных снарядов, мин и гранат, а также защите черепа от ударных нагрузок.
В середине XX века, когда были проанализированы результаты 1-й и 2-й мировых войн и последующих локальных конфликтов (в Корее и Вьетнаме) стало очевидно, что стальной гомогенный БШ не может обеспечить защиту головы бойца от наиболее массовой части спектра осколочного потока поражения на современном поле боя. Уровень его противоосколочной стойкости (ПОС) был весьма низок и не превышал V50%= 300-350 м/с для осколка массой 1г (50%-ная. вероятность непробития корпуса БШ). Надо сказать, что сделать защиту с более высокой ПОС можно только за счет увеличения толщины корпуса БШ, что сразу приведет к существенному увеличению носимой на голове массы. Так, например, чтобы поднять ПОС стального БШ с V50%= 300м/с до V5o%= 600 м/с надо почти удвоить толщину корпуса с 1,6мм до 2,5мм, что при физической плотности стали рст=7,85 г/см3 приведет к увеличению массы корпуса БШ с 1500г до 2350г. Это недопустимо, т.к. существуют медико-технические ограничения по величине допустимой носимой массы БШ, которые предписывают максимальный предел для общевойскового БШ в 1600г.
Такое ограничение обусловлено тем, что опытно-экспериментальным путем медиками была определена возможность получения тяжелой травм шейного участка позвоночника при превышении носимой распределенной массы БШ на голове сверх 1600г.
Таким образом, на рубеже 60-х - 70-х г.г. XX века появилась задача создания низкоплотных полимерных материалов, обладающих соизмеримым с высокопрочной сталью пределом прочности, которые пришли бы на замену стальному листовому прокату в производство БШ и позволили бы значительно повысить ПОС корпуса без увеличения его массы. Кроме того, полимерные материалы, ввиду своих физико-механических свойств, лучше поглощают и рассеивают ударно-волновую энергию взаимодействия средства поражения с защитной структурой преграды, чем гомогенная высокоуглеродистая сталь.
Такой материал был впервые разработан американской фирмой «Dupont» и был назван «параарамидным волокном», имевшим предел прочности такой же как у конструкционной стали, а физическую плотность рар.=1,43 г/см3, что более чем в 5 раз легче стали. Из параарамидного волокна сделали нить линейной плотности 110 текс. (масса нити в граммах на 1000м длины), которая получила торговую марку «Kevlar®29», и соткали полотно удельной массой 255 г/м2. Из этой ткани была изготовлена квазигомогенная многослойная тканево-полимерная структура, которая в эквивалентной массе с гомогенной монолитной сталью показала вдвое более высокую ПОС и существенно меньший динамический прогиб композиции при взаимодействии с имитатором стандартного осколка и пистолетной пулей 9мм калибра.
Первый в мире тканево-полимерный шлем появился в США. Его разработала натикская научно-исследовательская лаборатория Армии США в конце 1970-х годов. В начале 1980-х годов он был принят на вооружение сухопутных войск. Шлем получил название Personnel Armor System, Ground Troops (PASGT). Он был выполнен из ткани на основе волокна Kevlar®29 и связующего - фенольной или PVB смолы. Масса БШ составляла 1,4 (3,1 фунта) -1,9 кг (4,2 фунта)} имел 5 типоразмеров - XS, S, M, L, XL. Уровень ПОС шлема определялся военным стандартом MIL-STD-662E, полицейским NIJ 0106 и составлял V50% = 600м/с по стандартному осколку STANAG 2920, что примерно соответствует уровню в V50%=570...580 м/с по стальному шарику массой 1,03 г, которым испытываются все российские шлемы. Противоударные характеристики регламентированы стандартом MIL-h54099A.
Технология изготовления этих шлемов достаточно проста. Ткань, пропитанную полимерным связующим, проще говоря, смолой, укладывают в несколько слоев в форму. Полученную заготовку прессуют при определенной температуре, связующее полимеризуется, твердеет. От прессованной оболочки обрезают облой, устанавливают подтупейное устройство - шлем готов. Так как ткань, пропитанную смолой, называют «препрегом», то и технология изготовления шлемов получила название «препреговой». Основное преимущество этой технологии - простота и малая зависимость конечного результата от точности соблюдения режимов прессования. Поэтому достаточно быстро шлемы, аналогичные PASGT, начали выпускаться во многих странах. За 30 лет произведено несколько миллионов штук шлемов типа PASGT, он принят в качестве основного в НАТО и до сих пор используется Армией США. В армиях многих стран по всему миру используется или этот шлем, или его аналоги. Количество фирм-производителей шлемов типа PASGT перевалило за несколько сотен. Соответственно и разброс характеристик этих шлемов, как по массовым, так и по защитным характеристикам достаточно велик.
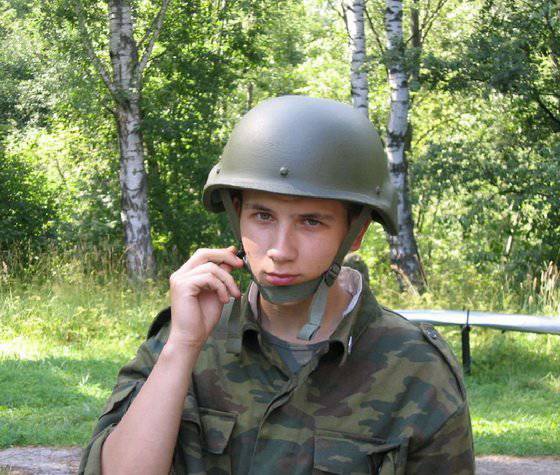
Боец в бронешлеме с коротким ремешком
Хотя в целом шлем удовлетворял требованиям военных, работы по его совершенствованию были начаты уже в конце 90-х годов. Работы эти были инициированы началом реализации во многих странах мира программ по оснащению бойца будущего столетия. Этими программами боец и его экипировка рассматриваются как единая система, которая, взаимодействуя с другими системами, должна максимально эффективно выполнять боевую задачу. Средства защиты, и шлем в частности, принимаются программой как элемент, который кроме выполнения защитных функций должен комплексироваться с другими элементами системы. Практически все программы «Боец будущего» рассматривают шлем как платформу для установки приборов ночного видения, связи, навигации, дисплеев для самоконтроля и информационных функций, что неминуемо приводит к увеличению массы, нагружающей голову.
Поэтому еще в 1996 году МО США была выдвинута двухгодичная программа SEP (Soldier Enhancement Program - Программа повышения боевых возможностей солдата), в рамках которой должна была быть разработана и испытана каска с более легкой основой. В качестве цели была поставлена задача снизить вес шлема на 25%.
Однако реализовать эти цели зарубежным разработчикам удается с большим трудом. Основная причина кроется как раз в созданной и эксплуатируемой ими технологии. Уже давно стало ясно, что баллистическая ткань наиболее эффективно работает, когда ее отдельные нити имеют возможность при упругой деформации растягиваться, достигая предела текучести, что происходит при максимальных нагрузках на материал. Ткань сама по себе уже ограничивает эластичность нитей и от типа плетения стойкость ткани может существенно меняться. Если же ткань пропитать смачивающим клеевым составом и превратить в жесткий композит, то баллистические характеристики такого композита будут хуже, чем у эквивалентного по массе ничем не связанного тканевого пакета.
Тем не менее, применяя новые, более эффективные, чем Kevlar®29 мате-риалы, зарубежным разработчикам удалось на 10-15% снизить и массу шлема и поднять его ПОС. Так, применение нового усовершенствованного арамидного волокна «Kevlar® KM2» и изготовление из него нитей более низкой линейной плотности (44текс, 67текс.) позволило снизить вес шлема на 8-10%.
Дальнейшие исследования по снижению веса привели к разработке и принятию на вооружение армии США в 2002 г новой, также арамидной, каски АСН (Advanced Combat Helmet), имеющей ещё меньший вес. Правда, снижение веса обеспечивалось, в основном, уменьшением на 8 % площади защиты, но разработчикам удалось увеличить на 6% ее ПОС.
Усиленно работает над проблемой снижения массы шлема и бывший разработчик шлема PASGT - исследовательская лаборатория NATICK. Так она в настоящее время исследует два новых материала, которые могут решить проблему снижения веса. Один из них - известный материал «Zyion». Используя этот материал, фирме удалось получить шлем массой всего в 800 г. (1,79 фунт). Однако, этот материал оказался нестойким к воздействию солнечного света, воды и потому непригодным для использования в шлемах. Сейчас фирма исследует новый материал на основе волокна М5, разработанного фирмой Magellan Systems Int. Расчеты показывают, что при том же уровне защиты использование материала М5 позволит уменьшить массу шлема на 35 %. Однако пока американский солдат воюет в шлеме, масса которого не менее 1,3-1,5 кг, а ПОС не превышает 680-700 м/с по STANAG-2920.
Россия значительно позже многих зарубежных стран начала думать о замене стальной каски CLU-68 на тканево-полимерную, хотя работы по созданию такой каски начались в НИИ Стали в инициативном порядке еще с середины 80-х годов. Разработчики института начали осваивать принципиально другую технологию - технологию термопластичного прессования квазигомогенных многослойных пленочных структур, или, как ее часто сейчас называют, - «пленочную» технологию. Суть ее проста - слои баллистической ткани прокладываются тонкой термопластичной пленкой. Затем пакет закладывается в прессформу, нагревается, прессуется и охлаждается. Пленка расплавляется и соединяет слои ткани. После охлаждения получается жесткая гомогенная оболочка корпуса шлема. По расчетам разработчиков пленка, размягчаясь, не смачивает нити ткани, оставляя им практически полную свободу предельной упругой деформации, а значит, стойкость такой композиции должна быть выше, чем у эквивалентного по массе препрега. Практика показала, что расчет был верен. Правда, чтобы прийти к желаемому результату институту потребовалось почти 10 лет. Именно столько шла отработка промышленной высокопроизводительной технологии получения шлемов требуемого качества. Зато у разработчиков появилось широкое поле для оптимизации композиции. Варьируя набором тканей в лицевых и тыльных слоях, меняя толщину и материал пленочного связующего можно было подобрать наиболее оптимальный вариант для заданных условий. В 1999 году первый серийный шлем, произведенный в НИИ Стали под индексом «6Б7», поступил в вооруженные силы российской армии. По своим характеристикам он сразу же превзошел свой зарубежный аналог: масса - не более 1,3-1,35 кг, противоосколочная стойкость -560 м/с, что соответствует 600-610 м/с по STANAG. К 2005 году НИИ стали разработал и сдал на вооружение еще 3 модели шлемов - 6Б26, 6Б27 и 6Б28. Все они являлись и до сих пор являются рекордсменами по массе и стойкости. Оптимизируя состав пакета, НИИ Стали удалось создать шлем массой не более 1,1 кг с ПОС выше 700 м/с (по STANAG - 730-740 м/с), причем не в опытном экземпляре, а в серийном производстве. Это прототип конструкции общевойскового БШ 2-го поколения.
В жизни за все надо платить. Естественно, столь высокие характеристики шлема были достигнуты соответственной ценой. Так жесткие требования предъявляются к качеству используемой баллистической ткани, малейшее отклонение от паспортных характеристик отправляет ткань в брак. Технология допускает использование в пакетах только цельных кусков, тогда как в препреговой технологии можно использовать пакеты, набранные из кусков баллистической ткани. Это приводит к увеличению расхода дорогостоящей ткани и соответственно стоимости конечного продукта. Сам процесс прессования тоже требует большего времени, чем в препреговой технологии, поскольку контролируемый нагрев заготовки и ее охлаждение происходят непосредственно в прессовой оснастке. Правда своими последними работами разработчики НИИ Стали показали, что резервы в оптимизации этой технологии есть и они не малые. Найдены решения по сокращению цикла нагрева и охлаждения заготовки. Не следует забывать еще ряд важных моментов. Поскольку пленочная технология не использует вредных смол, она на порядок экологически чище, что проявляется как в производстве, так и при эксплуатации шлема. Да и для организации крупносерийного производства пленочная технология прогрессивнее препреговой, поскольку позволяет автоматизировать процесс сборки тканево-полимерных пакетов для прессования, тогда как в препреговой технологии эта операция выполняется вручную.
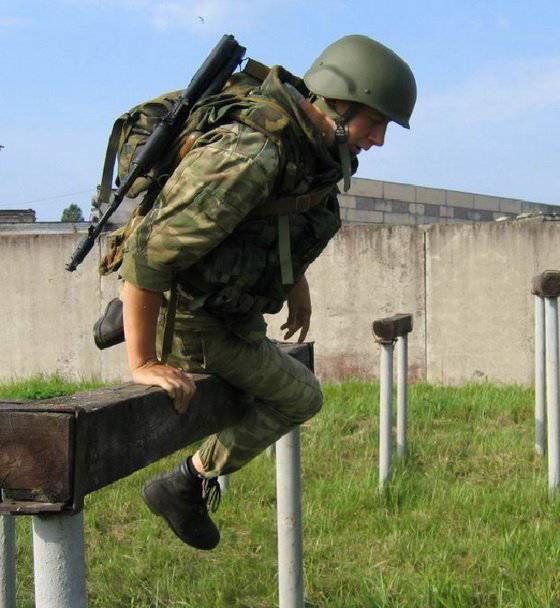
Боец в бронешлеме проходит полосу препятствий
Следуя из вышесказанного, и зарубежная и отечественная конструкция тканево-полимерного БШ используют в качестве защитной структуры многослойную квазигомогенную композицию на основе высокопрочной арамидной ткани и полимерного термореактивного или термопластичного связующего, которое скрепляет слои ткани по всей толщине структуры и заставляет работать корпус БШ как сплошную высокопрочную упругую оболочку - «полимерную броню».
Очень важно отметить тот факт, что сплошная гомогенная оболочка корпуса позволяет оптимально использовать физико-механические свойства материалов структуры, а именно - рассеивать ударную волну, образованную импульсом проникающего высокоскоростного средства поражения, и формируемую ей волну упругой деформации композитного материала, обеспечивая допустимые значения величины динамического прогиба оболочки. А именно величина динамического прогиба оболочки корпуса БШ при непробитии защитной структуры является определяющим фактором запреградного контузионного воздействия на голову человека. Поэтому максимально допустимая величина динамического прогиба оболочки всегда определяется в ходе государственных испытаний образцов БШ с помощью рентгеноимпульсной установки в реальном масштабе времени.
Кроме технологии пленочного термопласта, используемой для создания гомогенных сплошных оболочек корпусов БШ, в России была разработана «сме-шанная» технология, которая включает элементы препреговой технологии в соче-тании с «сухими» слоистыми тканевыми арамидными пакетами. При этом наружные тканевые слои защитной структуры пропитываются полимерным термореактивным связующим, а внутренние слои остаются сухими. Такая структура получила название от своих разработчиков (ЗАО ЦВМ «Армоком») - «дискретно тканевая структура» (ДТС).
Начиная с 2000г., российские ВС заказывают тканево-полимерные БШ, изготавливаемые и по пленочной технологии и по технологии ДТС примерно в одинаковых количествах. Только в 2010 - 2011гг. их было произведено и поставлено в армию около 70000 шт. Причем, боевые защитные и эксплуатационные характеристики гомогенного и дискретно-тканевого БШ абсолютно одинаковы, цена обоих образцов единая. В чем же различие?
А различие БШ как раз и кроется в составе структуры полимерной защитной композиции, получаемой в результате альтернативных технологических процессов прессования оболочек корпуса. В случае использования пленочного термопласта, как уже было отмечено, получается гомогенная сплошная структура оболочки и процесс взаимодействия средства поражения с такой преградой в общем лежит в плоскости классической теории прочности и упругости материалов. Корпус БШ, полученный по технологии ДТС, имеет выраженную гетерогенную структуру в состав которой входят две внешние относительно твердые и тонкие оболочки, придающие жесткость всей конструкции, и сухой слоистый пакет арамидной ткани, расположенный между оболочками. Такая структура называется «разнесенной», т.к. более высокоплотные слои находятся на расстоянии друг от друга, а между ними располагается низкоплотный материал. Разнесенная схема защитной структуры имеет свои преимущества, например, более эффективное поглощение и рассеивание ударной волны за счет наличия границ раздела между разноплотными слоями материалов композиции. Но это преимущество достигается большей толщиной комбинированного корпуса БШ с ДТС - до 15мм, в то время, как толщина гомогенного пленочного корпуса в самой массивной подтулейной зоне не превышает 8мм.
Но кроме этого преимущества больше никаких защитных выгод технология ДТС не дает, не говоря уже об относительно низкой производительности изготовления таких конструкций, прежде всего, за счет большой доли ручного труда, применяемого при сборке тканевого пакета. Вместе с тем, ДТС имеет один существенный недостаток - слишком малую толщину жестко-упругой внутренней оболочки корпуса БШ, задача которой состоит в том, чтобы за счет поглощения энергии упругой деформации сухого тканевого пакета сократить величину динамического прогиба полимерной композиции. Но т.к. сухой тканевый пакет не связан с тонким упругим подпором из препрега, то и вся энергия упругой деформации па¬кета приходится на локальную зону поражения тонкой препреговой оболочки, а не распределяется равномерно послойно по всей толщине структуры как у гомогенного тканево-полимерного корпуса. В этом случае, если в эквивалентных условиях сравнивать значения динамического прогиба двух технологически разных БШ - гомогенного и ДТС, то оказывается что для ДТС величина динамического прогиба больше чем у гомогенного пленочного термопласта.
Вопрос: «какая из технологий более предпочтительна и прогрессивна?» находится в компетенции Заказчика, который на этапе государственных испытаний детально определил все ТТХ обоих БШ, каждого в отдельности, и допустил в се-рийное производство оба образца.
Пока идет серийное производство тканево-полимерных БШ первого поколения можно было бы и не заострять внимание на технологических аспектах производства различных образцов, тем более, что производство ведется по действующей рабочей конструкторской документации литеры «О1», утвержденной заказчиком. Однако при создании боевой экипировки 2-го поколения заказчик выдвинул требование о разработке единой конструкции, а значит и защитной структуры, общевойскового БШ.
Становится злободневным «отложенный» заказчиком вопрос: «Какая структура полимерной защитной композиции отвечает современным требованиям по противоосколочной и противопульной стойкостям в максимальной степени? Какая структура обеспечивает наиболее приемлемые значения запреградного контузионного воздействия?»
Совершенно очевидно, что ответ на этот вопрос заказчик может получить только после комплексных сравнительных испытаний различных БШ, в том числе и зарубежного производства, в первую очередь медико-биологических исследований результатов динамического воздействия средств поражения на корпус БШ и голову человека. Не ответив на этот вопрос, нельзя будет принять выверенного и обоснованного решения в области боевой экипировки на длительную перспективу.
topwar.ru
Бронешлем – эволюция развития » Военное обозрение
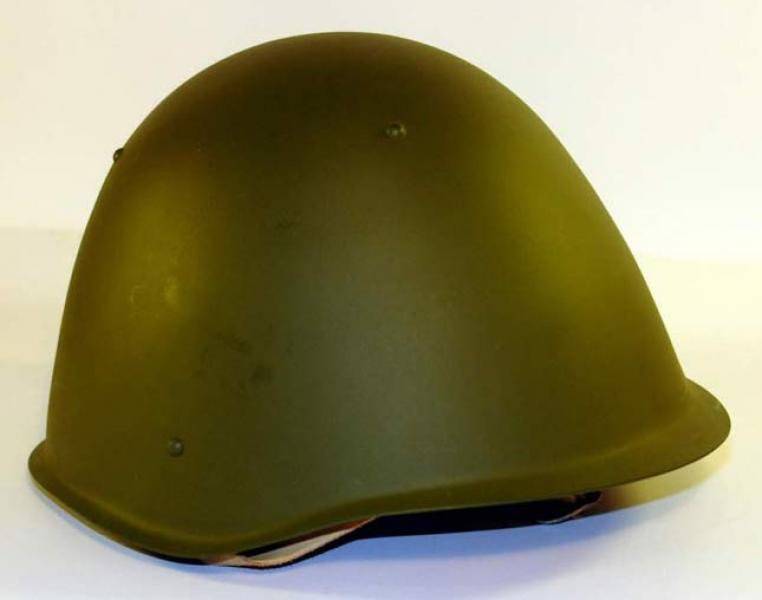
История создания современных бронешлемов В наши дни задача бронешлемов не изменилась - это защита головы от применяемого вооружения, осколков различных снарядов, гранат и мин, уменьшения вероятности попадания из стрелкового оружия, а также предохранение от ударов и нагрузок. В середине прошлого столетия рост новых технологий дал возможность начать работы над низкоплотными полимерными материалами с повышенным пределом прочности в отличие от стали.
Результатом анализа военных конфликтов и мировых войн стало очевидное слабое обеспечение стальным шлемом защиты головы военнослужащего от большинства видов осколков от применяемого вооружения. Уровень ПОС – противоосколочной стойкости шлема из листовой стали, обеспечивал до 350 м/с для одного осколка в 1 грамм (условно), пробивающего корпус бронешлема с 50-процентой вероятностью. Это условная мера, принятая для проведения оценивания ПОС. Улучшение ПОС стальных шлемов приводило лишь к увеличению их массы которую приходилось бы носить военнослужащим на голове. К примеру, для увеличения стандартного ПОС стального шлема вдвое, до 600 м/с, необходимо увеличить толщину стального листа почти вдвое, что увеличивало вес БШ на 700 грамм до 2.35 килограммов. Но тут всплывает другая проблема: проведенные эксперименты по ношению шлемов выявили их предельный вес -1.6 килограмм. Превышение данного веса резко увеличивало возможность получения тяжелых травм шейного позвоночника.
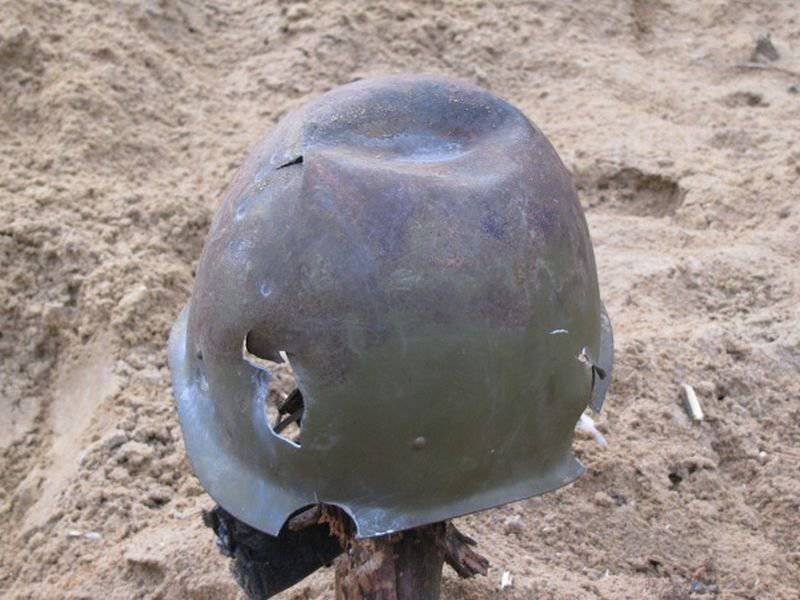
В начале второй половины прошлого века, шли изыскания по созданию шлемов из различных материалов. Успешные результаты создания полимерных материалов с низкой плотностью и высоким пределом прочности дали возможность использовать такие материалы в различных сферах человеческой деятельности. Основной же сферой применения стала возможность замены стальных листов и частей в военной сфере. Как выяснилось, полимерный материал к тому же обладает лучшими физико-механическими свойствами по поглощению и рассеиванию ударно-волновой энергии применяемых средств нападения, чем шлемы из стальных листов.
Первые разработкиПервыми добились успеха конструкторы американской компании «Dupont». Полученный материал получил название параарамидное волокно. Материал по прочности соответствовал конструкционной стали, его физплотность равнялась 1.43 гр на куб.см. – шлем из такого материала весил в пять раз меньше стального. Запатентованная торговая марка параарамидного волокна - Kevlar®29. Из данного волокна выделывали нить, обладающей линейной плотностью в 110 текс и создавали полотно с удельной массой 255 гр на кв.м. Из полотна изготавливали квазигомогенную тканево-полимерную многослойную структуру, которая при одинаковом весе с монолитной гомогенной сталью показывает улучшенные вдвое характеристики ПОС. Кроме того, при воздействии осколков или пули калибра 9-мм заметен намного меньший динамический прогиб под ними. Первыми, кто создал «тканевый» шлем, стали Соединенные Штаты Америки. Шлем спроектировали и создали в Натикской НИЛ СВ в 70-х годах. На вооружение Соединенные Штаты принимают «тканевый» шлем в начале 80-х годов, под названием «PASGT» - Personnel Armor System, Ground Troops.
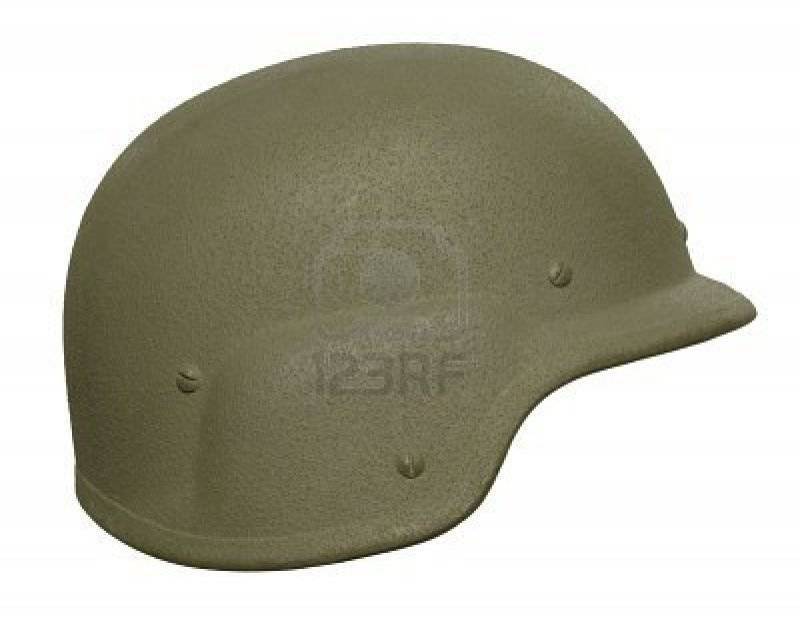
Технология создания PASGTБронешлемы создавали из ткани, в основе которой использовали Kevlar®29 и фенольную или PVB смолы. Вес БШ – 1.4-2.9 килограмма в зависимости от назначения. Серийные бронешлемы имели 5 размеров XL/S/M/L/XL. Характеристики ПОС определялись военными и полицейскими стандартами. Военный MIL-STD-662E и полицейский NIJ 0106 соответствовали до 600 м/с для осколка стандарта STANAG 2920 пробивающего корпус бронешлема с 50-процентой вероятностью. Этот стандарт приблизительно равен российскому стандарту при испытаниях отечественных моделей бронешлема. Само изготовление шлемов довольно простое – материал пропитывают смолой и несколькими слоями укладывают форму. Фому опрессовывают под необходимой температурой. Смола полимеризуется и затвердевает. Затвердевшую оболочку обрезают облой. После этого, оболочка получает подтулейное устройство и процесс создания шлема завершен. Такой метод изготовления называется метод препрегов, от названия ткани, пропитанной смолой (препреги). Простота такой технологии привела к широкому изготовлению и распространению аналогичных шлемов во многих государствах. По сегодняшний день было изготовлено несколько миллионов шлемов PASGT или их аналогов, почти все ВС стран блока НАТО обеспеченны «тканевыми» шламами. В Соединенных Штатах сухопутные подразделения до сих пор экипируются шлемами PASGT. ВС других стран также имеют в своей индивидуальной экипировке подобный шлем собственного или зарубежного производства. Поэтому характеристики БШ тканевого изготовления разных стран могут существенно отличатся друг от друга.
Современные разработки бронешлемов – СШАВсе современные разработки во многих странах идут по программам оснащения бойца будущего. Основой таких программ является единая система по обеспечению эффективного выполнения поставленной задачи. Единая система – полное взаимодействие всех систем экипировки между собой для их эффективного применения носителем. Хоть программы каждого государства и отличаются между собой, БШ в них во всех стал «носителем» различного вспомогательного и дополнительного оборудования, типа ПНВ, средств навигации и связи, информационных дисплеев различной направленности, видеокамер и спецоборудования. Все эти решения привели к повышению носимого на голове веса. Пентагон в 1996 году разработал программу «повышения боевых возможностей солдата». По ней было необходимо создать шлем на более легкой основе с конечной массой ¾ PASGT. Реализация программы проходила с большими трудностями. Основная причина крылась в используемых технологиях. В итоге, используя для создания ткани новые современные технологии, удается снизить вес БШ до 15 процентов, и немного подняв ПОС. для создания БШ использовали улучшенное арамидное волокно Kevlar® KM2, линейная плотность получаемых нитей снизилась в 2 раза. В 2002 году Соединенные Штаты принимают на вооружение бронешлем «Advanced Combat Helmet» малого веса. Этого удалось добиться сокращением на 8 процентов площади защиты, но, правда, улучшились на 6 процентов характеристики ПОС.
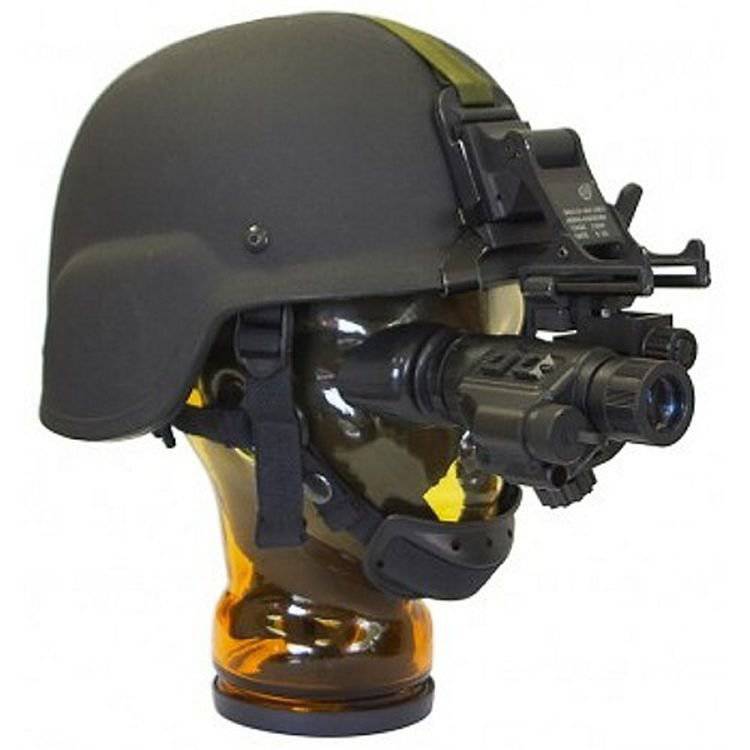
Современные разработки бронешлемов – РоссияРоссийская Федерация в вопросе замены шлемов из листовой стали на тканево-полимерные отстала от западных конкурентов. Но разработки «тканевых» шлемов начались, правда, по собственной инициативе, еще в 80-е годы в НИИ Стали. Советский Союз освоил иную технологию производства шлемов – термопластичное прессование многослойных квазигомогенных пленочных структур, получившую упрощенное название «пленочная».
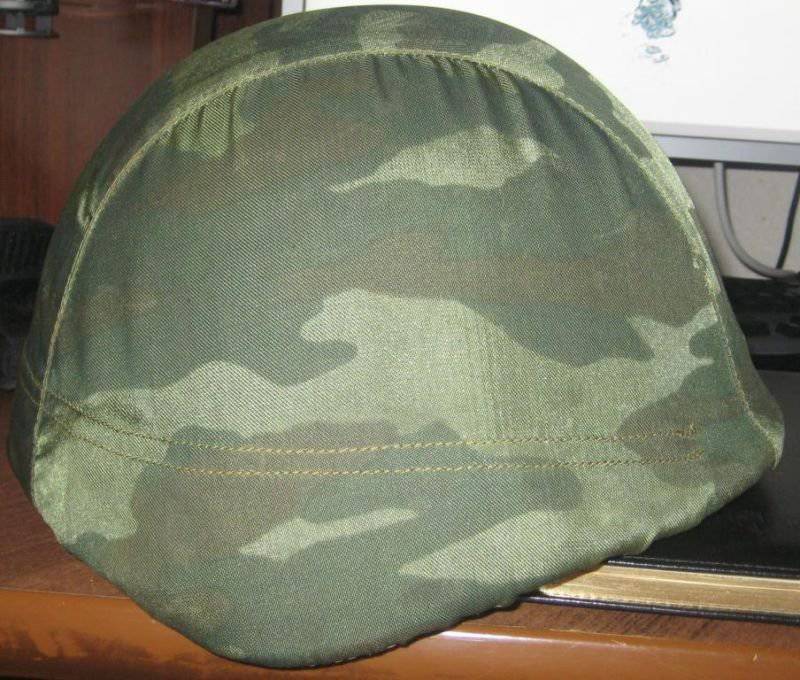
Технология создания российских пленочниковСуть технологии так же не очень сложная – между слоями баллистической ткани прокладывают тонкую термопластичную пленку. Потом, полученный пакет помещают в углубленную пресс-форму, в которой пакет нагревают, прессуют и охлаждают. Термопластическая пленка при нагревании, плавится и соединяет между собой два слоя ткани. Так создается оболочка российского шлема. Такая технология позволила добиться стойкости шлема больше чем американские препреги. До реализации данной технологии НИИ Стали шел целое десятилетие. Но теперь благодаря, тому, что технология досконально изучена, путем замены ткани, толщины ткани и «пленки», можно подобрать необходимый вариант исполнения бронешлема. Первый российский тканевый пленочной шлем поступает на вооружение России в 1999 году под индексом 6Б7. Пленочник сразу обходит по характеристикам зарубежный аналог:- максимальная масса 6Б7 не превышает минимальную массу PASGT;- ПОС 560 м/с, что по STANAG – 61- м/с.В 2005 году у ВС России появились еще 3 модели БШ – 6Б28,6Б27, 6Б26. Они на данное время являются лучшими по характеристикам БШ в мире. Последняя новинка от НИИ Стали – общевойсковой шлем 2-го поколения готовый пойти в серийное производство. Шлем имеет вес не более 1.1 килограмма, ПОС по STANAG до 740 м/с.
Как не жаль, но достижение таких характеристик не обошлось без увеличения цены. Малейшие отклонения в характеристиках баллистической ткани сразу означает брак. В пакеты отбираются куски целые куски ткани, в отличие от американской технологии. Все это привело к подорожанию конечного продукта – бронешлема. Из плюсов технологии – высокая экологичность (не используются смолы) и автоматизация производства.
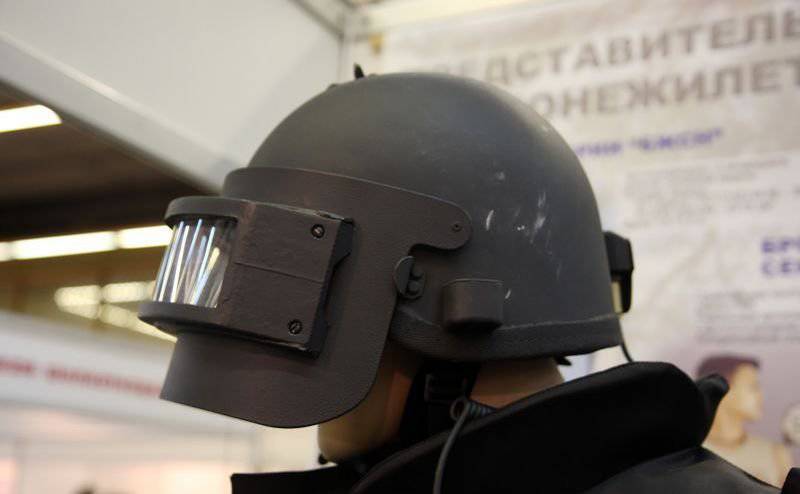
В России есть еще одна технология создания БШ – смешанная или дискретно-тканевая структура (ДТС). Разработчик компания «ЦВМ Армоком». Смысл технологии использование элементов препреги и сухих арамидных слоистых пакетов. В пакетах, только наружные слои ткани пропитывают смолой, а внутренние остаются сухими. Такая структура создания называется разнесенной. Положительный момент такого способа – более эффективное рассеивание и поглощение ударных волн, который достигается большой толщиной корпуса бронешлема – до 1.5 сантиметров. Для сравнения – пленочный бронешлем имеет толщину не более 0.8 сантиметра. Отрицательный момент смешанной технологии – малая толщина внутренней жесткоупругой оболочки. Динамический прогиб у данного бронешлема больший, чем у бронешлема изготовленного по пленочной технологии.
Открытый вопрос экипировки российского солдата будущегоС 2000 года российские военнослужащие получают бронешлемы выполненные по пленочной и смешанной технологиям приблизительно в равном количестве. Все характеристики и цена у них практически одинаковы. По опубликованным данным известно, что в 2010-11 годах ВС РФ получили 70 тысяч бронешлемов созданных по этим технологиям. Теперь же перед выходом БШ 2-го поколения в серийное производство, как и всей экипировки 2-го поколения, военное ведомство выдвигает требования к ее созданию – единая система. Это приведет к тому, что в России останется только одна технология создания БШ, и кто из них более будет соответствовать выдвинутым требованиям, сможет определить только сам заказчик при проведении комплексных испытаний единой системы 2-го поколения.
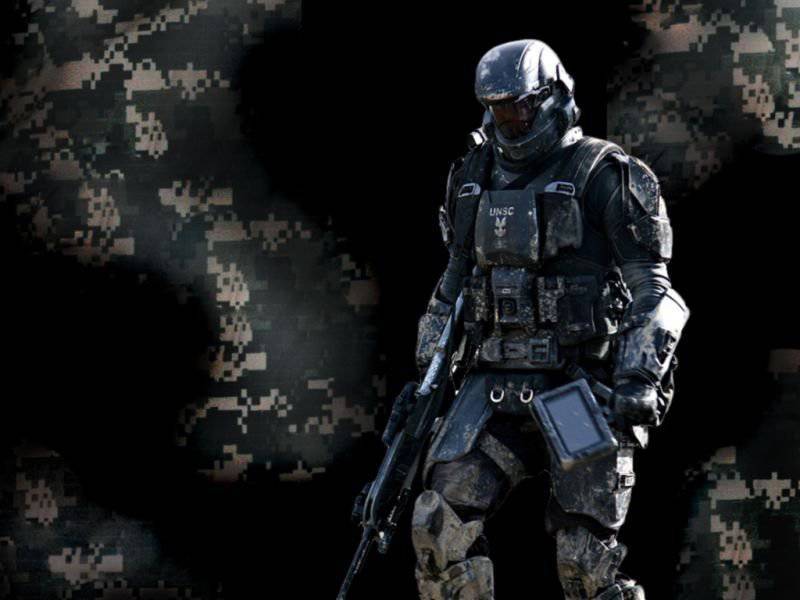
Недалекое будущее БШ - НанотехнологииАмериканские и российские конструкторы «NATICK» и НИИ Стали разрабатывают новые технологии создания бронезащиты. Американцы проводят исследования двух новых материалов созданных при помощи нанотехнологий –« Zyion» и волокно фирмы «Magellan Systems Int» М5. Первый материал позволил создать шлем весом около 0.8 килограмма, но материал пока неустойчив к воде и солнечному свету. Волокно при использовании поможет снизить вес американского шлема почти на треть, пока ведутся исследования. Российские специалисты создали материал который увеличил ПОС, уменьшил динамический прогиб, но материал тоже на данное время «боится» воды. Технология носит название жидкой брони.
Источники информации:http://www.posthunt.net/news/read/Tolko_tkan_luchshe_stali.htmlhttp://www.arms-expo.ru/055057052124050055048052048.htmlhttp://history-news.org/?p=3471
Автор: Роман Джерелейко
topwar.ru