Защита антикоррозионная: описание, особенности, виды и отзывы. Кольчуга антикоррозийное покрытие
400 (Грунтовка Hi-Gear, 311 г) Эта марка известна своими резиносодержащими антикоррозийными средствами, способными продлить срок эффективной эксплуатации кузова авто в 2-3 раза. Вещества Hi-Gear очень быстро сохнут и создают, устойчивую, влагоотталкивающую пленку на поверхности днища, лонжеронов, фартуков, порогов и арок колес. Средства надежно защищают не только от пыли и атмосферных явлений, но также и от соли, которой часто посыпают дорожное покрытие в нашей стране. Основные плюсы:
Минусы:
|
![]() 9.5 / 10 Рейтинг Отзывы Обработал средством Hi-Gear своего «китайчика» сразу после покупки. Качество полностью оправдало вложенные средства. |
www.expertcen.ru
Защита от коррозии энергетического оборудования
Коррозия и защита парогенераторов ТЭС
Энергетические блоки ТЭС (теплоэлектростанций) работают в тяжелых коррозионных условиях: высокая температура (515 - 530°С) и давление (15 МПа) горячего пара. Некоторые узлы изготавливаются из достаточно дешевых марок коррозионностойкой жаропрочной стали, которая устойчива в продуктах сгорания топлива. Основной причиной поломок парогенераторов является отказ самых теплонагруженных его частей, а именно: выходных и лобовых змеевиков, топочных экранов, неохлаждаемых подвесок и опор конвективных пакетов, пароперегревателей острого пара и т.д. Оборудование расположено по блочной системе, поэтому замена какого-либо узла, который вышел из строя в результате коррозии металла – достаточно трудоемкое и нелегкое дело. Чтоб ремонт проводился реже – стараются использовать качественные материалы.
На теплоэлектростанциях в качестве топлива используется угольная пыль и мазут. Твердотопливные котлы набирают все большую популярность. В мазутном топливе содержится большое количество веществ, очень агрессивно влияющих на металлы. Это соли натрия, ванадий, сера. При сгорании мазута образуется черный налет на всех поверхностях нагрева (тепловые экранные трубы). Его достаточно трудно удалить, т.к. он имеет твердую структуру. В процессе работы на некоторых участках с отложениями их температура достигает 600 °С.
В радиационной части топочные экраны разрушаются под воздействием газовой коррозии. При сгорании угольной пыли на поверхностях нагрева скапливается зола. Она состоит, в основном, из кислых и основных оксидов (SO3, CaO, SO2, Na2O, Al2O3, MgO, K2O, Fe2O3), а также Cl2 и h3S.
Именно при сгорании топлива образуется газовая среда слабоокислительного характера. Когда пылеугольное топливо горит не устойчиво, экран топочной камеры может вступить в контакт с факелом. В таком случае образуется восстановительная среда.
Плотный защитный слой в некоторой степени уменьшает скорость высокотемпературной коррозии поверхности нагрева, но если в состав отложений входят хлориды и сульфаты щелочных металлов, оксид ванадия – при температуре в 570 °С образуется расплав и коррозия усиливается.
Для защиты парогенераторов теплоэлектростанций (ТЭС) от коррозии, используются следующие методы: регулярная очистка нагреваемых поверхностей от зольных отложений, использование жаропрочных и коррозионно-стойких сплавов и сталей, введение присадок в топливо (иногда применяются ингибиторы), нанесение защитных покрытий.
При изготовлении оборудования парогенераторов основным материалом является сталь перлитного класса. Часто применяется сталь, легированная ванадием. Хорошей устойчивостью к межкристаллитной коррозии в продуктах сгорания мазута (с высоким содержанием примесей серы) при температуре 650 °С обладает аустенитная сталь марки ДИ-59. Она содержит в своем составе ниобий, марганец и медь.
Если сталь рекомендована для изготовления труб пароперегревателей, лучше, когда в ее составе будет марганец, а не никель, т.к. у первого температура плавления сульфидных эвтектик и сульфидов выше. Подвески и шипы делают из коррозионно-стойких, но малопластичных сильхромов (система Fe – Cr – Si) и сихромалей (Fe – Cr – Si – Al).
Не рекомендовано использовать сплавы, с добавками молибдена, т.к. в продуктах сгорания мазута они не обладают удовлетворительной коррозионной стойкостью. Хром и алюминий уменьшают шанс возникновения ванадиевой коррозии.
Температура подвесок и стоек труб газоходов порой превышает температуру поверхностей нагрева, поэтому для их изготовления применяют сплавы с хромом и никелем (хрома должно быть не меньше 50%). На твердотопливных установках в таких целях используется сталь Х23Н18.
Из аустенитных хромоникелевых сталей, легированных бором, вольфрамом, молибденом и ниобием, изготавливают парогенераторы, которые работают на буром угле либо природном газе (малоагрессивные топлива) и при высоких температурах.
В практике защиты от коррозии парогенераторов различного рода покрытия широкого применения не нашли. Это обуславливается проблематичностью ремонта. Постоянно контролировать их состояние также сложно.
Для увеличения эрозионной стойкости некоторых деталей аппаратуры (форсунок, в частности) используется диффузионное хромирование. В результате данного процесса в 20 – 25 раз увеличивается стойкость к эрозионному разрушению аустенитных хромоникелевых сталей.
Чтоб защитить хромоникелевые подвески труб, их силицируют. Тогда они становятся устойчивыми при контакте с золой, которая содержит оксид ванадия. Если температура не превышает 700 °С – подвески и огневые стенки покрывают боратными системами.
Для уменьшения разрушений необходимо не только использовать материалы с высокой коррозионной стойкостью, но и принимать все меры для уменьшения агрессивности среды. Например, чтоб разрыхлить золовые отложения, снизить их коррозионную активность и облегчить их удаление, вводят в топливо специальные присадки. Из них можно отметить 10-% водный раствор нитрита магния. Он затрудняет припекание золы к нагревательным зонам, а также повышает ее температуру плавления. Такое же действие оказывают и металлоорганические соединения железа, бария и меди. На 1 тонну мазута израсходуется всего 2 килограмма данного вещества.
При введении в угольную пыль 1,5% CaCl2•2h3O при температуре до 700 °С, уменьшается серная коррозия малоуглеродистой стали, а в отходящих газах содержание серы понижается.
Внутренняя поверхность труб покрыта окислами железа и другими веществами, которые способствуют повышению тепловых напряжений. Чтоб эти напряжения уменьшить, необходимо периодически промывать систему кислотными растворами с последующей их нейтрализацией.
Коррозия теплоэнергетического оборудования (паровых котлов, трубопроводов)
Теплоэнергетическое оборудование – это теплосети, установки водоподготовки, паровых котлов, конденсатно-питательного тракта и т.п.
Паровые котлы и установки конденсатно-питательного тракта вступают в контакт с водой, которая подготавливается термически или химически. Для защиты их от коррозии проводят обескислороживание, например, используя для этого гидразинную или термическую обработку (иногда два этих метода вместе).
Паровой котел представляет собой емкость из низколегированной или малоуглеродистой стали, которая обогревается горячими газами. Выходя из парового котла, горячий газ может далее подаваться на перегреватель, где он нагревается еще сильнее. Сталь для изготовления перегревателей используют с большим содержанием легирующих добавок. Для того, чтоб обеспечить максимальную теплопередачу, тепловые трубы формируются в виде пучка, а нагревающий их газ подается в межтрубное пространство (иногда может подаваться прямо в трубы). После того, как пар был использован или совершил работу, он попадает в конденсатор трубчатого типа. Чаще всего конденсаторы изготовлены из медных сплавов. Для охлаждения используют любую воду (пресная, соленая, даже с загрязнениями и примесями). Далее, когда пар перешел в конденсат, он возвращается в котел и происходит новый цикл.
В водных средах при высокой температуре на железе образуется оксидная двухслойная пленка. Для защиты от коррозии паровых котлов широко используется обескислороживание. А в обработанной воде таким способом оксидная пленка представляет собой магнетит Fe3O4. В состав внутреннего защитного слоя входят плотноупакованные кристаллиты, которые очень плотно сцепляются с металлической подложкой. Их диаметр около 0,02 – 0,2 мкм. Внешний слой состоит из кристаллов диаметром 1 мкм, которые упакованные не плотно.
В растворах с высоким или низким значением рН защитный слой магнетитов растворяется, и металлическая подложка в большей степени подвергается коррозионному разрушению.
Если в воде, предназначенной для паровых котлов, присутствует растворенный кислород, то его влияние несколько сложнее.
Предупредить коррозию паровых котлов можно. Для этого необходимо соблюдать режимы водоподготовки и работы самих установок. Кроме того, использовать специальные стали.
Работает в агрессивной коррозионной среде и оборудование теплосетей (трубопроводы, магистрали). Коррозию таких установок условно можно разделить на: внешнюю (со стороны грунта) и внутреннюю (со стороны воды). Коррозия латуней проявляется в виде обесцинкования, а сталей (в горячей воде) - носит язвенный характер. Для защиты установок теплосети от внутренней коррозии, используют герметик АГ-2. Он изолирует зеркало воды в баках-аккумуляторах. Также проводят вакуумную деаэрацию воды и стабилизацию, силикатную обработку. Используют пленкообразующие амины. Проводят различные мероприятия эксплуатационного и конструктивного характера.
Коррозионное разрушение трубопроводов и магистралей со стороны грунта обусловлено постоянным контактом с электрохимически агрессивной средой и воздействием блуждающих токов. Основные способы защиты от коррозии труб это: протекторная защита, электрохимическая защита катодным током и нанесение разнообразных покрытий.
www.okorrozii.com
АНТИКОРРОЗИОННОЕ ПОКРЫТИЕ «КОЛЬЧУГА» | Эмаль
Композиция «Кольчуга» предназначена для антикоррозионной защиты изделий из углеродистых и низколегированных сталей, путем формирования на их поверхности защитного покрытия (технология нанесения композиции «Кольчуга» — это холодное цинкование).
Антикоррозионная композиция «Кольчуга» и технология ее применения полностью соответствует новым требования, предъявляемым к подобным материалам:
Сформированное антикоррозионное покрытие работает по трем защитным механизмам – барьерному, ингибиторному, протекторному. И это позволяет ему гибко реагировать на воздействие изменяющихся условий окружающей среды. Такая антикоррозионная защита металла сохраняет свои свойства не менее 30 лет.Антикоррозионное покрытие «Кольчуга» не требует сложной подготовки поверхности перед нанесением. Композиция поставляется потребителю в заранее расфасованных емкостях, быстро отверждается и полимеризуется.Холодное цинкование с использованием композиции «Кольчуга» безопасно для персонала и окружающей среды (состав не содержит вредных веществ и летучих органических соединений), не горит, можно использовать для защиты емкостей с питьевой водой. Соответствует международным требованиям, предъявляемым к современным ЛКМ.
Антикоррозионное покрытие «Кольчуга» успешно применяется практически во всех промышленных отраслях: гражданское и военное строительство, энергетика и ТЭК, судостроение, транспортное строительство, коммунальное хозяйство и др. — везде, где требуется надежная и долговременная антикоррозионная защита металлоемких объектов. В отраслевых разделах представлены фото объектов, защищенных АЦСК «Кольчуга».
Технологическая инструкция для АЦСК «Кольчуга» (подготовка, нанесение, контроль качества готового антикоррозионного покрытия). В разделе «Перспективные разработки» представлена текстурирующая паста «Шагрень» для подготовки поверхности под окраску: она придает стальной поверхности необходимую шероховатость, за счет чего усиливается адгезия наносимого антикоррозионного покрытия «Кольчуга». Паста используется в случае невозможности песко- или дробеструйной подготовки поверхности.
kupit-emal.ru
НПО «Химические технологии»
Сфера деятельности: разработка и производство антикоррозионных составов, силикатных ЛКМ, материалов для подготовки поверхности, технических моющих средств, консультирование и разработка стандартов для организаций по АКЗ
Контакты:
- адрес: Россия, г. Москва, Волоколамское шоссе, дом 112, к.1, стр.3
- многоканальный телефон: +7 (495) 215-09-56
Телефоны отделов:
- силикатные ЛКМ: +7 (495) 215-09-58
- антикоррозионные защитные покрытия: +7 (495) 215-09-57
- моющие составы, химическая подготовка поверхности: +7 (495) 215-09-56
- жидкое стекло: +7 (495) 215-09-56
- факс: +7 (495) 491-38-01
- электронная почта: Этот адрес электронной почты защищён от спам-ботов. У вас должен быть включен JavaScript для просмотра.
Сайт: www.himtechnologii.ru
О компании
Специалисты компании НПО «ХимТех» (научно-производственное объединение «Химические технологии») разработали и производят цинксиликатные составы для холодного цинкования «Кольчуга», антикоррозионные лакокрасочные материалы (например, грунт-эмаль по ржавчине «Кольчуга-П», в состав материала входит преобразователь ржавчины), технические моющие средства марки «Силика, специальную пасту для подготовки поверхности перед окрашиванием.
Среди продукции НПО «Химические технологии» представлено несколько марок жидкого стекла: классические натриевое, калиевое и жидкое высокомодульное натриевое стекло, изготовленное по специальной технологии.
Специалисты компании оказывают консультативные услуги по АКЗ, проводят экспертизы и оценку затрат защищаемых от коррозии объектов, производят мероприятия по подготовке поверхности (пескоструйная очистка, дробеструйная очистка, обезжиривание, химическое фосфатирование) и нанесению покрытий.
Компания занимается научными разработками в сфере материалов с заданными свойствами.
Производимые составы: антикоррозионное покрытие "Кольчуга".
описание, особенности, виды и отзывы
Предохранение материалов от поражения ржавчиной является обязательной мерой перед введением конструкций и отдельных деталей в эксплуатацию. Развитие коррозии зачастую не только повреждает металлические поверхности, но и негативно влияет на свойства прилегающих материалов – пластиковых или деревянных. Нередко еще на стадии заводского изготовления подбирается метод, по которому будет выполнена такого рода защита. Антикоррозионная оболочка также может быть сформирована и в бытовых условиях с применением специальных средств.
Общие сведения об антикоррозийной обработке
Большинство средств антикоррозийной защиты наносятся на поверхность материала, что и создает покрытие, стойкое к развитию негативных процессов. Обычно такой обработке подвергаются изделия и конструкции, которые тесно контактируют с влагой, почвой и химическими веществами. Чаще всего защита антикоррозионная является многофункциональной. То есть помимо предотвращения той же ржавчины покрытие может повышать и теплоизоляционные качества объекта, обеспечивать эффект шумоподавления.
Каждое средство имеет свой ресурс действия и также разрушается в процессе эксплуатации. Этот нюанс предусматривает технолог в выборе метода обработки. Кроме того, антикоррозионная защита сама по себе может быть активным химическим веществом. Для разных металлов и сплавов подбираются наиболее благоприятные с точки зрения взаимного воздействия защитные покрытия.
Особенности защитных средств от ржавчины
Работа с металлом в части нанесения защитных покрытий требует тщательной подготовки. Как правило, основные работы касаются именно этого этапа. Также в отличие от методов обработки других материалов создание барьера перед ржавчиной для металлов нередко предусматривает дополнительное применение компаунда. Таким образом, уже в комплексе формируется защита антикоррозионная с эффектом электроизоляции.
Специфика использования разных видов антикоррозийной защиты также обуславливается сферой применения целевого объекта. Если конструкцию планируется использовать под землей, как в случае с водопроводом или газовыми коммуникациями, то разрабатываются рецепты многослойных покрытий, обеспечивающие и усиленную механическую защиту. Другие требования предъявляются к материалам, которые контактируют с воздушной средой и водой. В данном случае повышенное внимание уделяется защитной изоляции от влаги, пара и мороза. Для этого в составы добавляют соответствующие присадки и пластификаторы.
Разновидности методов
Традиционным способом защиты металла от коррозии считается нанесение лакокрасочных покрытий, предотвращающих процессы ржавления. Это могут быть составы из распространенных декоративных составов, которые также выполняют эстетическую функцию. Более технологичные способы защиты – это термическая обработка и легирование. При таких методах меняется сама структура материала в верхнем слое.
Например, легирование позволяет переводить металлические сплавы из активного в пассивное состояние. Таким образом, материалы антикоррозионной защиты естественно формируют пленку, представляющую собой барьер перед ржавлением на фоне электрохимического воздействия. Этот способ хорош тем, что эффективно работает не только с железом и легко подвергаемыми коррозии металлами, но и с нержавеющими материалами, которые в агрессивных средах могут деформироваться.
Отзывы о лакокрасочной защите металлов
Это наиболее популярный способ защиты металла от ржавчины. Его ценят за ценовую доступность, относительно высокую эффективность и гибкость в применении. Тем не менее в долгосрочной перспективе лакокрасочная антикоррозионная защита проявляет себя не лучшим образом. Как отмечают пользователи обработанных таким способом конструкций, рассчитывать на полноценную функцию изоляции приходится не более чем на срок в 7-8 лет. Далее приходится обновлять покрытие, зачастую реставрируя и поверхность целевого материала.
Есть и другие недостатки, которые отмечают пользователи антикоррозийных лакокрасочных составов. Например, ограничение в плане использования. Подобный вариант не годится для усиления труб, которые будут проложены под водой или в земле. Если защита антикоррозионная должна служить более 10 лет без обновления, то есть смысл воспользоваться другими методами.
Отзывы о гальванической обработке
Этот метод также относится к традиционным. Он чаще применяется в промышленности и строительной сфере. По мнению многих специалистов, это оптимальный вариант обработки конструкций, рассчитанных на долгосрочную эксплуатацию. Он эффективно оберегает металл от коррозии и других разрушающих процессов. Но также следует помнить, что антикоррозионная защита конструкций гальваническим методом стоит недешево, требует профессионального подхода в реализации и сама по себе является трудоемкой операцией.
По сути, это метод цинкования, который также предполагает предварительную подготовку металлической поверхности. Пользователи отмечают сложности, возникающие при выполнении пескоструйной обработки и травления. В бытовых условиях применять этот способ нецелесообразно. Хотя гальваническое покрытие гораздо эффективнее проявляет себя в эксплуатации, чем лакокрасочные средства.
Отзывы о термической защите
Это один из методов, ориентированных на изменение структуры материала с целью уплотнения молекул. Термическая антикоррозионная защита трубопроводов, к примеру, позволяет не только уберечь металл от ржавчины, но также снять напряжение конструкции, если она располагается под землей.
По мнению пользователей этой методики, она демонстрирует высокие защитные свойства в самых тяжелых условиях эксплуатации. Правда, реализовать такую обработку можно только при использовании специального промышленного оборудования. Печные камеры для обжига и криогенных процессов обходятся недешево, что объясняет низкую популярность данной защиты.
fb.ru
- Все записи пользователя "himtekh"
20 апреля 2015 стартовал федеральный проект ведущего российского производителя антикоррозионных материалов на основе неорганических полимеров НПО «Химические Технологии» — Программа лояльности «Клуб «ХимТех» для проектировщиков. Участвовуют в данной программе как проектные организации, так и непосредственно специалисты-проектировщики.
Программа лояльности «Клуб ХимТех» является долговременной, базируется на индивидуальном подходе к каждому участнику. Основная цель программы заключается в предоставлении специалистам проектной отрасли (нашим партнерам) нового уровня отношений, доверия и сервиса.
Регистрируясь на нашем портале и присоединяясь к сообществу Клуба «ХимТех» http://himtechnologii.ru/club_himtech, у вас теперь есть возможность в
Система защитных покрытий, состоящая из двух композиций: АЦСК «Кольчуга» и «Кольчуга-Ф» внесена в стандарт по антикоррозионной защите мостов СТО -01393674-007-2011 «Защита металлических конструкций мостов от коррозии методом окрашивания».
После длительного перерыва продолжаем серию публикаций о защитных составах под маркой «Кольчуга». С конца марта начат выпуск новых однокомпонентных материалов бюджетной категории для антикоррозионной защиты: водоразбавляемая грунт-эмаль «Кольчуга-П» и акриловая разноцветная эмаль для финишной окраски «Кольчуга-Ф».
Грунт-эмаль «Кольчуга-П» предназначен для недорогой противокоррозионной защиты поверхностей из черного металла. Используется как самостоятельное покрытие по черному металлу, бетону и железобетону, дереву, шиферу, а также как грунт в тех случаях, когда поверхность трудно очистить от ржавчины. Фото в качестве примера:
Акриловая эмаль АК-101 «Кольчуга-Ф» — финишный состав,
НПО «Химические Технологии» освоило производство экологически чистых силикатных красок согласно ГОСТ 18958−73. Необходимо отметить, что связующее этих материалов — калийное жидкое стекло — производится компанией по усовершенствованной технологии. В результате, цвет красок получается более насыщенным, долго не тускнеет, уменьшается расход окрасочного состава. Яркие, насыщенные цвета красок будут долго радовать глаз и создавать отличное настроение у детей и взрослых!
Силикатные краски серии КС-154 не содержат органических растворителей, поэтому не имеют резких запахов, экологически безопасны, и могут использоваться в замкнутых помещениях без принудительной вентиляции. Благодаря своим свойствам, силикатные краски показаны к применению при окраске внутренних и внешних поверхностей в социально значимых объектах: больницах, поликлиниках, школах, детских садах и др. зданиях.
Защита металлоконструкций от коррозии актуальна практически для любой отрасли: энергетика, ТЭК, военно-промышленный комплекс, транспорт, строительство и др. Для того, чтобы антикоррозионные материалы обеспечили надежную и долговечную защиту металла, необходимо тщательно подготовить поверхность под окраску.
По международному стандарту ISO-8501−1 подготовка стальной поверхности под окраску должна соответствовать степени St3 (дробеструйная, пескоструйная обработка) или Sa2,5 (обработка металлическими щетками). Не всегда существует возможность осуществить такую механическую подготовку (остановка производства, демонтаж конструкций, отсутствие необходимого оборудования и расходных материалов и т. д.). В такой ситуации, к вам на помощь придет текстурирующая паста «Шагрень» (см. фото и видео).
12.02.2014 г.
Получено заключение испытательной лаборатории ЦНИИС (Центральный научно-исследовательский институт транспортного строительства): по результатам ускоренных климатических испытаний, композиция «Кольчуга» может применяться для антикоррозионной защиты наружных и внутренних поверхностей металлоконструкций, эксплуатируемых в промышленной зоне с холодным и умеренно холодным климатом (УХЛ1). Прогнозируемый срок службы антикоррозионного покрытия «Кольчуга» — не менее 30 лет. При этом достаточно толщины покрытия 75-90 мкм.
Экономика должна быть экономной! Этот лозунг справедлив как никогда и в наше время.
Поставщики стальной продукции для инфраструктуры Новой Москвы ищут и находят наиболее оптимальные и экономически выгодные методы и технологии защиты металлоконструкций, как наиболее подверженных разрушению от воздействия окружающей среды.
Например, такое обычное явление нашей жизни, как мачты городского освещения. Тяжелые, крупногабаритные они нужны везде. Чтобы долго они служили, их надо защитить. Кто-то подвергает столбы горячему цинкованию:
- Транспортировка на завод горячего цинкования – 24 часа
- Подготовка поверхности очень вредными веществами, горячая оцинковка - 24 часа
- Погрузка, доставка до места – 24 часа
Итого – 3 суток и масса накладных расходов.
На Одинцовском машиностроительном заводе пошли по другому пути, что позволило сэкономить до 50% затрат на антикоррозионную защиту. Завод выпускает мачты городского освещения для Новой Москвы. Никуда их не отвозит, а прямо в цехах завода на заранее подготовленную поверхность мачт наносит цинк наполненную композицию «Кольчуга». Весь процесс занимает 24 часа.
Примеры мачт городского освещения:
Вся наша цивилизация – железная. Куда ни взглянешь – везде металл, да притом ржавый, неприглядная картина. Практически 20% годового мирового производства стали идет на воспроизводство проржавевшего металла! Вот так…..Компания НПО «Химические Технологии» разрабатывает и производит высокоэффективные консервационные и защитные композиции. Практическое использование этих материалов позволяет снизить металлоемкость конструкций и сооружений, расход топливно-энергетических ресурсов, себестоимость продукции.
Но нет предела совершенству! Наши инженеры разработали новый надежный материал для защиты от всемирной напасти под названием «ржа». И носит он гордое русское название «Кольчуга». Создавалась антикоррозионная композиция по новейшей технологии, благодаря которой удалось достигнуть высокой стойкости, долговечности готового антикоррозионного покрытия в различных средах. Это технология – «know how» нашей компании. На фото новое оборудование, сделанное по спецзаказу:
Лаборатория, где производится контроль качества исходных материалов и готовой продукции
Стоимость композиции «Кольчуга» вполне конкурентоспособна, даже по сравнению с отечественными антикоррозионными материалами. Подробности и фотографии объектов, защищенных "Кольчугой" в следующих публикациях.
«Кольчуга» - надежное защитное покрытие для коммуникаций жилых и производственных зданий уже работает
Сердце дома. Техническое подполье каждого многоквартирного дома с полным правом можно назвать его сердцем. Здесь проходят многочисленные тепло- и водопроводы, газовые и канализационные трубы, телефонные и электрические кабели, располагаются пункты управления всеми инженерными коммуникациями.Подвальные помещения и технические подполья жилых и производственных зданий относятся к высокой (С4) либо очень высокой (C5-I) категории коррозионной активности атмосферы (согласно стандарту ISO 12944) благодаря постоянной влажности, выпадению конденсата и очень высокому уровню загрязнения. Такие условия способствуют не только возникновению, но и протеканию с повышенной скоростью коррозионных процессов на металлических поверхностях инженерных коммуникаций. Своевременная и грамотная защита металла от коррозии позволит избежать возникновения нештатных ситуаций, аварий и незапланированных ремонтов.
Рис. 1 Стандартный вид коммуникаций в подвальных помещениях зданий и сооружений.
Идеальное покрытие. В соответствии с «Временными указаниями по проектированию внутриквартальных инженерных коммуникаций в коллекторах, в технических подпольях и технических коридорах» № СН 338-65 «газопроводы и водопроводы в коллекторах, технических подпольях и коридорах очищаются от ржавчины и окрашиваются в один или в два слоя» рекомендованными лакокрасочными материалами (ЛКМ).Однако, эксплуатирующие организации, применяя традиционные ЛКМ, сталкиваются с определенными трудностями:...
sdelanounas.ru
ИНСТРУКЦИЯ по применению антикоррозионной композиции «КОЛЬЧУГА» ТУ
Транскрипт
1 Утверждаю Генеральный директор ООО «НПО «Химические технологии» Метелица Р.В. ИНСТРУКЦИЯ по применению антикоррозионной композиции «КОЛЬЧУГА» ТУ Москва 2013 г
2 1. ВВЕДЕНИЕ Данная инструкция предназначена для определения последовательности работ при изготовлении защитного покрытия композицией «КОЛЬЧУГА» для защиты металлоконструкций от коррозии. В инструкции приведены сведения, касающиеся технологии использования защитного покрытия «КОЛЬЧУГА», требований по подготовке поверхности перед нанесением, рекомендаций по формированию покрытия, контролю, утилизации и проведению ремонта сформированного покрытия. В руководстве приведены универсальные системы покрытий, рекомендованные ООО «НПО «Химические Технологии» для сред разной степени агрессивности. Настоящая технологическая инструкция является базовым руководством при нанесении антикоррозионного защитной композиции «КОЛЬЧУГА». 2.ОПИСАНИЕ АНТИКОРРОЗИОННОЙ КОМПОЗИЦИИ «КОЛЬЧУГА» Антикоррозионная композиция «КОЛЬЧУГА» представляет собой двухкомпонентную цинксиликатную композицию, состоящую из неорганического связующего на основе высокомодульного жидкого стекла (водный раствор силиката натрия) и наполнителя - цинкового мелкодисперсного порошка. Антикоррозионная цинк-силикатная композиция «КОЛЬЧУГА» предназначена для антикоррозионной защиты металлических поверхностей при их контакте с атмосферой, почвой, морской, пресной и питьевой водой, нефтью и нефтепродуктами и др., как в качестве самостоятельного покрытия, так и грунтовки. Антикоррозионная цинк-силикатная композиция «КОЛЬЧУГА» может применяться в нефтегазовой промышленности, атомной и электроэнергетики, гидро-техники, морском и железнодорожном транспорте, морских и портовых сооружениях, трубопроводах, строительстве, ЖКХ, химической промышленности, машиностроение и др.
3 3. ОСНОВНЫЕ ХАРАКТЕРИСТИКИ КОМПОЗИЦИИ «КОЛЬЧУГА». Характеристика Таблица 1. Основные хар-ки покрытия «КОЛЬЧУГА» Значение 1. Цвет и глянец готового серый/серебристый, матовый покрытия 2. Плотность готовой к употреблению композиции, мин. 2,7 3,2 г/см 3 3. Содержание сухого остатка 4. Рекомендуемые типы подложек 5. Условная вязкость композиции не менее 80% по массе сталь, очищенная механическим способом по ISO Sa 2 ½, St 3 поверхность свободна от ржавчины, окалины, масляных и иных органических загрязнений не менее 15 с 6. Температура нанесения допускается нанесение краски на подложку, имеющую температуру от +5 о С до +40 о С и относительной влажности (25 95)%; температура подложки должна быть выше точки росы минимум на 3 о С 7. Время высыхания слоя до не более 30 минут при температуре плюс (20±2) о С. степени 2 8. Время формирования покрытия 9. Жизнеспособность композиции 10. Временной интервал нанесения покровных красок 11. Срок хранения компонентов композиции не менее 24 часов при температуре плюс 20 о С для работы в атмосферных условиях; не менее 5 суток при температуре плюс 20 о С для работы в водных средах (окончательное отверждение покрытия происходит в процессе эксплуатации) не менее 4 часов при температуре (20±2) о С минимальный 24 часа; максимальный не ограничивается, при условии очистки от грязи и солей цинка 12 месяцев с даты изготовления в сухом, прохладном месте 12. Способ поставки в герметичных закрытых емкостях в соответствующих пропорциях 13. Дополнительные данные: а) теоретический расход композиции при средней толщине пленки Комплексные системы защиты толщина, мкм г/м при использовании покрытия «КОЛЬЧУГА» в качестве грунтовки оно может быть перекрыто финишными красками.
4 4. ПОДГОТОВКА ПОВЕРХНОСТИ ДЛЯ ФОРМИРОВАНИЯ ЗАЩИТНОГО ПОКРЫТИЯ. Чтобы система покрытий обеспечивала длительную защиту, перед нанесением защитной композиции необходимо соответствующим образом подготовить поверхность. Для этого следует оценить состояние поверхности стальной конструкции. Стальные поверхности, на которых отсутствует защитное покрытие, могут быть в различной степени покрыты ржавчиной, прокатной окалиной и иными загрязнениями (пыль, жир, водорастворимые соли, отложения и т.п.). Состояние подобных поверхностей определяется стандартом ISO : «Подготовка стальной поверхности перед нанесением красок и подобных покрытий. Визуальная оценка чистоты поверхности». Стандартом определены четыре состояния стали, по степени ржавости: 1. A- Стальная поверхность в значительной мере покрыта прочно прилегающей прокатной окалиной и в малой степени ржавчиной (или ржавчина вообще отсутствует). 2. B- Стальная поверхность, которая начала ржаветь, прокатная окалина начала отслаиваться. 3. C- Стальная поверхность, на которой прокатная окалина исчезла вследствие ржавления или может быть удалена путем соскабливания, имеется некоторый питтинг, видимый невооруженным взглядом. 4. D- Стальная поверхность, на которой прокатная окалина исчезла вследствие ржавления, имеется общий питтинг, видимый невооруженным взглядом. При подготовке поверхности для нанесения необходимо очистить её от продуктов коррозии, окалины, грязи, масляных загрязнений, старого покрытия. Очистка производится абразивными материалами струйным способом (воздух сухой, без масла) либо механическим способом. Очистке подлежит вся стальная поверхность, защищаемая покрытием «КОЛЬЧУГА». Таблица 2. Степени подготовки поверхности способом струйной очистки Sa 3 Sa 2,5 Sa 2 Sa 1 Струйная очистка до визуально чистой стали. На поверхности, осматриваемой невооруженным глазом, не должно быть видно масла, жира и грязи, она должна быть очищена от прокатной окалины, ржавчины, краски и других посторонних частиц. Очищенная поверхность должна иметь однородный металлический цвет. Очень тщательная струйная очистка. На поверхности, осматриваемой невооруженным глазом, не должно быть видно масла, смазки, жира и грязи, она должна быть очищена от прокатной окалины, ржавчины, краски и посторонних частиц. Возможны только остаточные следы загрязнений в виде едва заметных пятен или полос. Тщательная струйная очистка. На поверхности, осматриваемой невооруженным глазом, не должно быть видно масла, смазки, жира, грязи, должна быть удалена почти вся прокатная окалина, ржавчина, краска и посторонние частицы. Любые оставшиеся загрязнения должны приставать прочно и не должны отслаиваться. Легкая струйная очистка. На поверхности, осматриваемой невооруженным глазом, не должно быть видно масла,
5 жира, грязи, должна быть удалена отслаивающаяся прокатная окалина, ржавчина, краска и посторонние частицы. Таблица 3. Степени подготовки поверхности путем очистки ручным или механическим инструментом St 2 St 3 Тщательная очистка ручным и механическим инструментом. На поверхности, осматриваемой невооруженным глазом, не должно быть видно масла, жира, грязи и должна быть удалена отслаивающаяся прокатная окалина, ржавчина, краска и посторонние частицы. Очень тщательная очистка ручным и механическим инструментом. Аналогично St 2, однако поверхность должна обрабатываться более тщательно, чтобы обеспечить металлический блеск поверхности. Перед очисткой с поверхности металлических конструкций необходимо срезать временные монтажные приспособления, удалить заусенцы, задиры и наплывы металла, зачистить сварные швы. Острые кромки закруглить радиусом не менее 0,8 мм. Для формирования качественного защитного покрытия «КОЛЬЧУГА» поверхность СК должна быть очищена до степеней Sa 2,5 или St 3. Наличие на очищенной поверхности влаги, масла и загрязнений при окраске не допускается. В качестве обезжиривающих жидкостей может применяться сольвент, ацетон, «Стекломин» и др. растворители. Временной интервал между очисткой поверхности и нанесением покрытия не должен превышать 24 часов при относительной влажности воздуха не более 90 %.
6 Рис 1. Степени подготовки поверхности металла в зависимости от первоначального её состояния.
7 5. НАНЕСЕНИЕ ЗАЩИТНОГО ПОКРЫТИЯ. 5.1 Порядок подготовки композиции «КОЛЬЧУГА» к формированию защитного слоя Композиция «КОЛЬЧУГА» нетоксична, пожаро-взрывобезопасна, всвязи с чем допускается работа с ней в закрытых помещениях при обеспечении требований техники безопасности. Важно: связующее покрытие приготовлено на неорганической основе, поэтому любые жировые загрязнения приведут к нулевой адгезии (прилипанию) покрытия к защищаемой поверхности и к ее последующему отслоению (отслоение происходит практически сразу же после высыхания). Композиция «КОЛЬЧУГА» поставляется заранее расфасованной на 2 компонента «А» и «В» Для подготовки композиции необходимо вскрыть емкости с компонентами и перемешивая добавить компонент «В» (цинковый порошок) в компонент «А» (связующее). Стандартная фасовка 8 кг готовой композиции. Композиция подготавливается при температуре плюс (5 40) С и относительной влажности (25 95)%. Полученную композицию тщательно перемешивать механически или вручную, не допуская образования комков или осадка. Важно: исключить обратный порядок смешивания (всегда цинковый порошок засыпается в связующее, а не на оборот). Если необходимо меньшее количество композиции, то для приготовления 1 кг композиции надо взять в среднем 250 г связующего «А» и 750 г цинкового порошка «В» (относительное соотношение). После тщательного перемешивания выдержать готовую композицию в течение 30 минут, перемешивая ее несколько раз за это время. Вязкость готовой композиции составляет не менее 15 сек по вискозиметру В3-4 в зависимости от плотности связующего. 5.2 Порядок формирования защитного слоя композицией «КОЛЬЧУГА» Запрещается проведение работ по нанесению покрытия на открытом воздухе во время дождя, конденсации влаги. В этом случае необходимо окрасочные работы проводить в помещении, под навесом. При окрашивании используются кисти, валики и т.д., краскопульт (Приложение Б). Важно: Допустимая температура подложки для нанесения покрытия плюс (5 40) С, должна быть выше точки росы минимум на 3 С. Покрытие наносится при температуре плюс (5 40) С и относительной влажности (25 95)%. Удельный вес порошка намного больше удельного веса связующего, поэтому при окрашивании любым способом необходимо не реже 1 раза в 5-10 минут перемешивать композицию, чтобы избежать седиментации (оседания) порошка. После каждого использования инструментов их необходимо промыть чистой водой. Композиция может наноситься в один или два слоя в зависимости от эксплуатационных условий, в которых она будет использоваться. Стандартная толщина защитного покрытия нанесенного в 1 слой мкм. Сушка до начала эксплуатации не менее 24 часов.
8 При необходимости получения толщины покрытия более 90 мкм, рекомендуется формирование покрытия в 2 слоя. Сформировать первый слой толщиной мкм, второй мкм. При этом время нанесения второго слоя не позже мин после нанесения первого слоя покрытия. Окончательная сушка покрытия не менее 48 часов. При использовании покрытия в качестве грунтовки (в комбинированных системах покрытий): Рекомендуемое количество слоёв покрытия «КОЛЬЧУГА» один. Толщина сухой пленки мкм. Сушка грунтовочного покрытия до нанесения финишного покрытия не менее 24 часов. Примечание - Покрытие совместимо с ЛКП на полиуретановой, эпоксидной и алкидной основе. Важно: В большинстве случаев в результате конденсации влаги на покрытии могут появляться белесые следы. Наличие таких следов подтверждает правильность нанесения покрытия. Их достаточно протереть или промыть чистой водой. ВНИМАНИЕ: Смешанные компоненты А и В не подлежат длительному хранению и должны быть использована в течение 8-10 часов. Разбавлять краску водой или другими разбавителями категорически запрещается Требования безопасности при работе с композицией «КОЛЬЧУГА». Композиция, готовая к применению, пожаро-взрывобезопасна. Температура вспышки, воспламенения и самовоспламенения, температурные и концентрационные пределы распространения пламени отсутствуют. Высушенное покрытие при контакте с водой не выделяет вредных химических веществ. Производственные помещения, в которых производят расфасовку, смешивание компонентов композиции должны быть обеспечены местной вентиляцией или механической приточно-вытяжной вентиляцией по ГОСТ , обеспечивающей состояние воздуха рабочей зоны в соответствии с ГОСТ , ГН , ГН , СанПин , СанПин При применении и испытании краски должны соблюдаться общие требования безопасности по ГОСТ и ГОСТ , требования безопасности при работе с цинковым порошком по ГОСТ Работающие должны быть обеспечены респираторами типа РУ-60, РПГ-67, «Лепесток» и другим по ГОСТ После окончания работы необходимо тщательно вымыть использованное оборудование, руки и открытые части тела чистой водой. Способы обеспечения систем предотвращения пожара и противопожарной защиты, а также организационно-технические мероприятия по предотвращению пожара при производстве краски проводят по ГОСТ Средствами пожаротушения должны служить пенные огнетушители марки ОП-5 или углекислотные марок ОУ-2, ОУ-5 по действующей нормативной документации.
9 Опасные зоны на предприятии, в производственных помещениях, на рабочих местах (площадках) должны быть обозначены соответствующими знаками безопасности по ГОСТ КОНТРОЛЬ КАЧЕСТВА СФОРМИРОВАННОГО ПОКРЫТИЯ. Контроль качества покрытия осуществляется следующими методами: замером толщины покрытия по сухой пленке инструментально; визуальным осмотром изделия для обнаружения дефектов, недопустимых для покрытия. Замер толщины покрытия по сухой пленке производится в 6-10 точках (но не менее чем в 3- х точках) на каждой поверхности окраски. Толщина покрытия принимается как среднее значение всех замеров на одной плоскости. Контроль толщины сухой пленки обычно производится датчиками откалиброванными на эталонах стальных пластин. Эталоны проверяются в соответствии со специальной методикой. При визуальном контроле качества покрытия допускаются включения не более 4 шт. на площади 100 см 2, длиной не более 2-х мм и шириной не более 0,5 мм. Внимание: Потеки краски не допускаются. Не допускаются пропуски в покрытии, механические повреждения, сколы, трещины и отслоения покрытия. Результаты контроля качества покрытия записываются в журнал регистрации качества покрытия. 7. УТИЛИЗАЦИЯ ОТХОДОВ После окончания работы необходимо тщательно вымыть использованное оборудование, руки и открытые части тела чистой водой. После использования композиции и её компонентов их упаковка должна подвергаться погашению и утилизации согласно нормативным актам, действующим у пользователя, с целью предотвращения загрязнения окружающей среды. 8. ПЕРИОДИЧНОСТЬ ОСМОТРА И РЕМОНТ ЗАЩИТНОГО ПОКРЫТИЯ В процессе длительной эксплуатации покрытия или при несоблюдении технологии нанесения (попадание масла из компрессора, некачественная обработка поверхности, несоблюдение режимов влажности при нанесении, сушке или отверждении и т.д.), а также в результате механических повреждений поверхности возможно разрушение покрытия. Поэтому необходимо регулярно осматривать нанесенное покрытие для оценки его текущего состояния. Периодичность осмотров определяется исходя из принятого срока службы покрытия, но не реже 1 раза в три года. При площади разрушения не более 10-15% производится ремонт покрытия, при более обширных разрушениях восстановление. При единичных царапинах протекторные свойства покрытия сохраняются в течение длительного времени, однако общий срок службы снижается. Если в процессе эксплуатации повреждается незначительная часть покрытия (менее 15%), проводится его текущий ремонт. При этом покрытие на отдельных участках может быть разрушено до стальной поверхности, либо до нижнего слоя. В зависимости от этих обстоятельств в каждом конкретном случае определяется объем ремонтных работ. Восстановление разрушившегося покрытия проводится в технологической последовательности, изложенной в пункте 5 настоящего руководства.
10 При восстановлении оставшееся прочно сцепленное с металлом покрытие обрабатывается щеткой, а открытая, подвергшаяся коррозии поверхность очищается механическим способом (Sa 2 ½ или St 3 (пункт 4). Дальнейшая последовательность технологических операций нанесения покрытия должна соответствовать порядку, изложенному в настоящей инструкции. При разрушении до стальной поверхности прокорродировавшие участки очищаются механическим способом. Затем производится восстановление на них покрытия по изложенной выше технологии. Приложение А. ТИПОВЫЕ СИСТЕМЫ ЗАЩИТЫ ОТ КОРРОЗИИ АНТИКОРРОЗИОННЫМ ПОКРЫТИЕМ «КОЛЬЧУГА» Сферы и объекты использования систем антикоррозионного покрытия «Кольчуга» Строительные металлоконструкции (промышленное и гражданское строительство, выхлопные трубы и газоходы, металлоконструкции торговых развлекательных и производственных зданий и помещений) Автотранспортное и транспортное строительство (мостовые и туннельные металлоконструкции, дорожные ограждения, антенно-мачтовые сооружения, опоры освещения, подвижной состав) Нефтегазовый комплекс (наружние и внутренние поверхности резервуаров для хранения нефти, темных и светлых нефтепродуктов, эстакад, галерей, опор нефтеи газопроводов, погружного нефтепромыслового оборудования, трубопроводы снаружи и внутри). Ёмкости с горячей, холодной и питьевой водой (емкости для хранения питьевой воды, баки-аккумуляторы, баки - декарбонизаторы, деаэрационные колонны) Судостроение и судоремонт (подводня и надводная часть судов, жилые, служебные и грузовые помещения судов, трубопроводы снаружи и внутри) Количество слоев и толщина покрытия, мкм (при контакте с атмосферой) или 2 (при контакте с нефтью и нефтепродуктами) или или Таблица А.1. Срок службы, годы, не менее*
11 Портовые и другие гидротехнические сооружения (сооружения причальных и нефтеналивных эстакад, металлоконструкции судопропускных и судоподъемных сооружений, металлоконструкции и оборудование гидроэлектростанций, береговые и прибрежные конструкции различного назначения) Энергетика (опоры ЛЭП и оборудование подстанций) Жилищно-коммунальное хозяйство (магистральные трубопроводы снаружи и внутри, оборудование и коммуникации подвальных помещений, бакиаккумуляторы ТЭЦ ) 1 (при контакте с атмосферой) или 2 (при контакте с морской или речной водой) * - подготовка поверхности перед нанесением до степени Sa 2½ по ИСО
12 Приложение Б. РЕКОМЕНДАЦИИ ПО ПОДБОРУ ОКРАСОЧНОГО ОБОРУДОВАНИЯ. Б.1. Окраска методом воздушного напыления 1. Краскопульт - с верхним расположением бачка; 2. Рекомендуемое давление атм; 3. Диаметр сопла - 1,8..2,5 мм; 4. Ориентировочная толщина слоя краски за 1 проход мкм Б.2. Окраска по технологии HVLP 1. Краскопульт - с верхним расположением бачка; 2. Диаметр сопла - 1,5..2,5 мм; 3. Расстояние от среза сопла до окрашиваемой поверхности см 4. Ориентировочная толщина слоя краски за 1 проход мкм Примечание: По данной технологии воздух, используемый для распыления ЛКМ, не запасается в ресивере с помощью компрессора а нагнетается турбиной. Применение турбины, позволяет снизить вес используемого оборудования (до 5 7 кг), что позволяет перемещать агрегат одному человеку. ВНИМАНИЕ: После окончания окраски и при перерывах в окраске более 5 минут, рекомендуется слить композицию из бачка и промыть краскопульт большим количеством теплой воды. Оставление композиции «КОЛЬЧУГА» в бачке более 5 минут приведет к её отверждению в сопле краскопульта и выходу его из строя.
13 Приложение В. НОРМАТИВНО-ТЕХНИЧЕСКАЯ ДОКУМЕНТАЦИЯ.
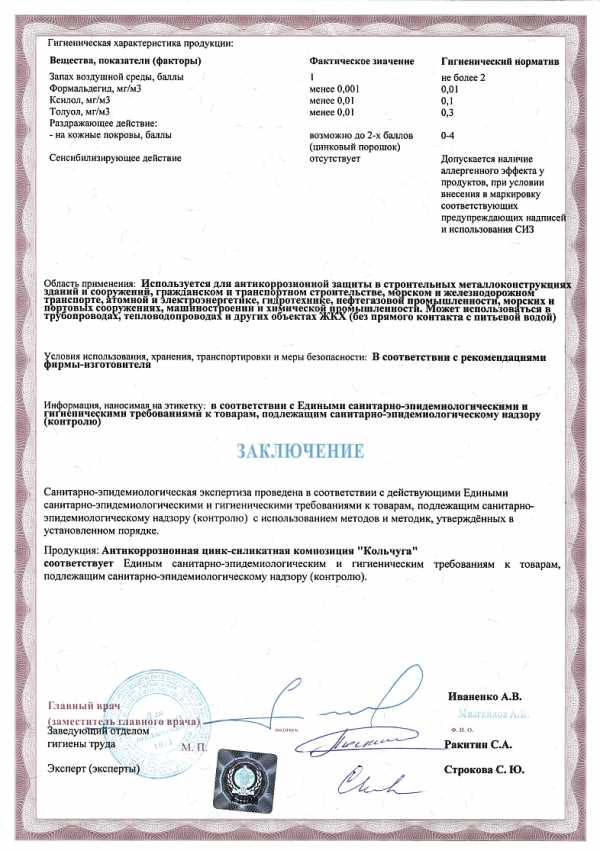
14
15
docplayer.ru