НОВОРОССИЯ NEWS. Современные защитные шлемы вс рф
Современные бронешлемы - защитные структуры и технологии изготовления
Главнейшая задача БШ, сформулированная военными ведущих мировых держав, состоит в защите головы бойца от самого массового на поле боя фактора поражения - осколков естественного дробления осколочно-фугасных снарядов, мин и гранат, а также защите черепа от ударных нагрузок.
В середине XX века, когда были проанализированы результаты 1-й и 2-й мировых войн и последующих локальных конфликтов (в Корее и Вьетнаме), стало очевидно, что стальной гомогенный БШ не может обеспечить защиту головы бойца от наиболее массовой части спектра осколочного потока поражения на современном поле боя. Уровень его противоосколочной стойкости (ПОС) был весьма низок и не превышал V50%= 300-350 м/с для осколка массой 1г (50%-ная вероятность непробития корпуса БШ).
Надо сказать, что сделать защиту с более высокой ПОС можно только за счет увеличения толщины корпуса БШ, что сразу "приведет" к существенному увеличению носимой на голове массы. Так, например, чтобы поднять ПОС стального БШ с V50%= 300м/с до V5o%= 600 м/с надо почти удвоить толщину корпуса с 1,6мм до 2,5мм, что при физической плотности стали рст=7,85 г/см3 приведет к увеличению массы корпуса БШ с 1500г до 2350г.
Это недопустимо, т.к. существуют медико-технические ограничения по величине допустимой носимой массы БШ, которые предписывают максимальный предел для общевойскового БШ в 1600г. Такое ограничение обусловлено тем, что опытно-экспериментальным путем медиками была определена возможность получения тяжелой травмы шейного участка позвоночника человеком при превышении носимой распределенной массы БШ на голове сверх 1600г.
Таким образом, на рубеже 60-х - 70-х г.г. XX века появилась задача создания низкоплотных полимерных материалов, обладающих соизмеримым с высокопрочной сталью пределом прочности, которые пришли бы на замену стальному листовому прокату в производство БШ и позволили бы значительно повысить ПОС корпуса без увеличения его массы.
Кроме того, полимерные материалы, ввиду своих физико-механических свойств, лучше поглощают и рассеивают ударно-волновую энергию взаимодействия средства поражения с защитной структурой преграды, чем гомогенная высокоуглеродистая сталь.
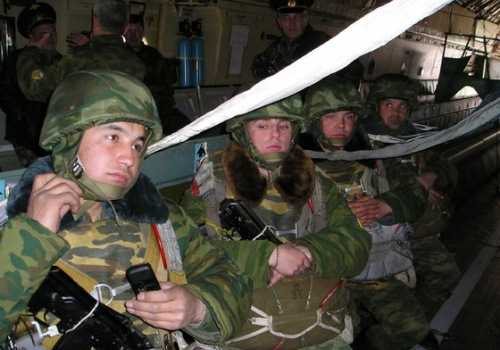
Такой материал был впервые разработан американской фирмой «Dupont» и был назван «параарамидным волокном», имевшим предел прочности такой же, как у конструкционной стали, а физическую плотность рар.=1,43 г/см3, что более чем в 5 раз легче стали. Из параарамидного волокна сделали нить линейной плотности 110 текс. (масса нити в граммах на 1000м длины), которая получила торговую марку «Kevlar®29», и соткали полотно удельной массой 255 г/м2.
Из этой ткани была изготовлена квазигомогенная многослойная тканево-полимерная структура, которая в эквивалентной массе с гомогенной монолитной сталью показала вдвое более высокую ПОС и существенно меньший динамический прогиб композиции при взаимодействии с имитатором стандартного осколка и пистолетной пулей 9мм калибра. Первый в мире тканево-полимерный шлем появился в США.
Его разработала Натикская научно-исследовательская лаборатория Армии США в конце 1970-х годов. В начале 1980-х годов он был принят на вооружение сухопутных войск. Шлем получил название Personnel Armor System, Ground Troops (PASGT). Он был выполнен из ткани на основе волокна Kevlar®29 и связующего - фенольной или PVB смолы.
Масса БШ составляла 1,4 (3,1 фунта) -1,9 кг (4,2 фунта)} имел 5 типоразмеров - XS, S, M, L, XL. Уровень ПОС шлема определялся военным стандартом MIL-STD-662E, полицейским NIJ 0106 и составлял V50% = 600м/с по стандартному осколку STANAG 2920, что примерно соответствует уровню в V50%=570...580 м/с по стальному шарику массой 1,03 г, которым испытываются все российские шлемы. Противоударные характеристики регламентированы стандартом MIL-h54099A.
Технология изготовления этих шлемов достаточно проста. Ткань, пропитанную полимерным связующим, проще говоря, смолой, укладывают в несколько слоев в форму. Полученную заготовку прессуют при определенной температуре, связующее полимеризуется, твердеет. От прессованной оболочки обрезают облой, устанавливают подтулейное устройство - шлем готов,
Так как ткань, пропитанную смолой; называют «препрегом», то и технология изготовления шлемов получила название «препреговой». Основное преимущество этой технологии - простота и малая зависимость конечного результата от точности соблюдения режимов прессования. Поэтому достаточно быстро шлемы, аналогичные PASGT, начали выпускаться во многих странах.
За 30 лет произведено несколько миллионов штук шлемов типа PASGT, он принят в качестве основного в НАТО и до сих пор используется Армией США. В армиях многих стран по всему миру используется или этот шлем или его аналоги. Количество фирм-производителей шлемов типа PASGT перевалило за несколько сотен. Соответственно и разброс характеристик этих шлемов, как по массовым, так и по защитным характеристикам достаточно велик.
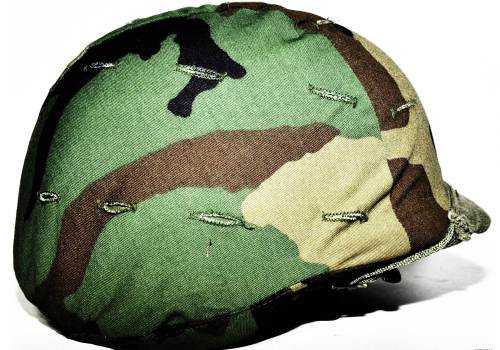
Хотя в целом шлем удовлетворял требованиям военных, работы по его совершенствованию были начаты уже в конце 90-х годов. Работы эти были инициированы началом реализации во многих странах мира программ по оснащению бойца будущего столетия. Этими программами боец и его экипировка рассматриваются как единая система, которая, взаимодействуя с другими системами, должна максимально эффективно выполнять боевую задачу.
Средства защиты, и шлем в частности, принимаются программой как элемент, который кроме выполнения защитных функций должен комплексироваться с другими элементами системы. Практически все программы «Боец будущего» рассматривают шлем как платформу для установки приборов ночного видения, связи, навигации, дисплеев для самоконтроля и информационных функций, что неминуемо приводит к увеличению массы, нагружающей голову.
Поэтому еще в 1996 году МО США была выдвинута двухгодичная программа SEP (Soldier Enhancement Program - Программа повышения боевых возможностей солдата), в рамках которой должна была быть разработана и испытана каска с более легкой основой. В качестве цели была поставлена задача снизить вес шлема на 25%.
Однако реализовать эти цели зарубежным разработчикам удается с большим трудом. Основная причина кроется как раз в созданной и эксплуатируемой ими технологии. Уже давно стало ясно, что баллистическая ткань наиболее эффективно работает, когда ее отдельные нити имеют возможность при упругой деформации растягиваться, достигая предела текучести, что происходит при максимальных нагрузках на материал.
Ткань сама по себе уже ограничивает эластичность нитей и от типа плетения стойкость ткани может существенно меняться. Если же ткань пропитать смачивающим клеевым составом и превратить в жесткий композит, то баллистические характеристики такого композита будут хуже, чем у эквивалентного по массе ничем не связанного тканевого пакета.
Тем не менее, применяя новые, более эффективные, чем Kevlar®29 материалы, зарубежным разработчикам удалось на 10-15% снизить и массу шлема и поднять его ПОС. Так, применение нового усовершенствованного арамидного волокна «Kevlar® KM2» и изготовление из него нитей более низкой линейной плотности (44текс, 67текс.) позволило снизить вес шлема на 8-10%.
Дальнейшие исследования по снижению веса привели к разработке и принятию на вооружение армии США в 2002 г новой, также арамидной, каски АСН (Advanced Combat Helmet), имеющей ещё меньший вес. Правда, снижение веса обеспечивалось, в основном, уменьшением на 8 % площади защиты, но разработчикам удалось увеличить на 6% ее ПОС.
Усиленно работает над проблемой снижения массы шлема и бывший разработчик шлема PASGT- исследовательская лаборатория NATICK. Так, в настоящее время она исследует два новых материала, которые могут решить проблему снижения веса. Один из них - известный материал «Zyion». Используя этот материал, фирме удалось получить шлем массой всего в 800 г. (1,79 фунт).
Однако, этот материал оказался нестойким к воздействию солнечного света, воды и потому непригодным для использования в шлемах. Сейчас фирма исследует новый материал на основе волокна М5, разработанного фирмой Magellan Systems Int. Расчеты показывают, что при том же уровне защиты использование материала М5 позволит уменьшить массу шлема на 35 %. Однако, пока американский солдат воюет в шлеме, масса которого не менее 1,3-1,5 кг, а ПОС не превышает 680-700 м/с по STANAG-2920.
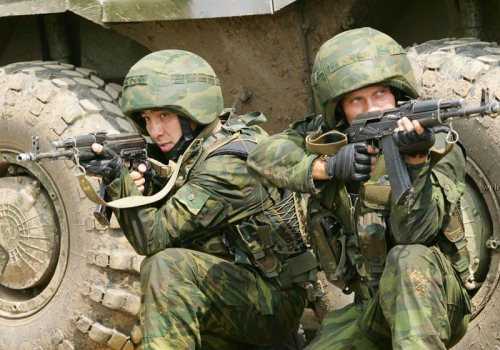
Россия значительно позже многих зарубежных стран начала думать о замене стальной каски CLU-68 на тканево-полимерную, хотя работы по созданию такой каски начались в НИИ Стали в инициативном порядке еще с середины 80-х годов. Разработчики института начали осваивать принципиально другую технологию -технологию термопластичного прессования квазигомогенных многослойных пленочных структур, или - как ее часто сейчас называют - «пленочную» технологию.
Суть ее проста - слои баллистической ткани прокладываются тонкой термопластичной пленкой. Затем пакет закладывается в прессформу, нагревается, прессуется и охлаждается. Пленка расплавляется и соединяет слои ткани. После охлаждения получается жесткая гомогенная оболочка корпуса шлема. По расчетам разработчиков пленка, размягчаясь, не смачивает нити ткани, оставляя им практически полную свободу предельной упругой деформации, а значит, стойкость такой композиции должна быть выше, чем у эквивалентного по массе препрега.
Практика показала, что расчет был верен. Правда, чтобы прийти к желаемому результату институту потребовалось почти 10 лет. Именно столько шла отработка промышленной высокопроизводительной технологии получения шлемов требуемого качества. Зато у разработчиков появилось широкое поле для оптимизации композиции. Варьируя набором тканей в лицевых и тыльных слоях, меняя толщину и материал пленочного связующего можно было подобрать наиболее оптимальный вариант для заданных условий.
В 1999 году первый серийный шлем, произведенный в НИИ Стали под индексом «6Б7», поступил в вооруженные силы российской армии. По своим характеристикам он сразу же превзошел свой зарубежный аналог: масса - не более 1,3-1,35 кг, противоосколочная стойкость -560 м/с, что соответствует 600-610 м/с по STANAG.
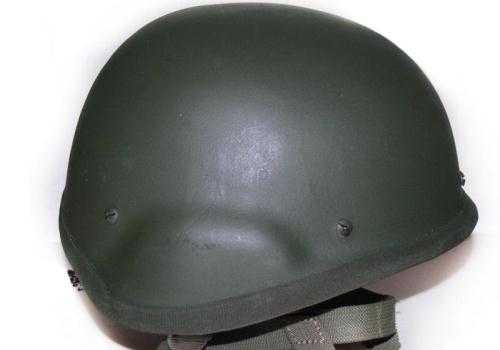
К 2005 году НИИ стали разработал и сдал на вооружение еще 3 модели шлемов - 6Б26, 6Б27 и 6Б28. Все они являлись и до сих пор являются рекордсменами по массе и стойкости. Оптимизируя состав пакета, НИИ Стали удалось создать шлем массой не более 1,1 кг с ПОС выше 700 м/с (по STANAG - 730-740 м/с), причем не в опытном экземпляре, а в серийном производстве. Это прототип конструкции общевойскового БШ 2-го поколения.
Естественно, столь высокие характеристики шлема были достигнуты соответственной ценой. Так, жесткие требования предъявляются к качеству используемой баллистической ткани, малейшее отклонение от паспортных характеристик отправляет ткань в брак. Технология допускает использование в пакетах только цельных кусков, тогда как в препреговой технологии можно использовать пакеты, набранные из кусков баллистической ткани.
Это приводит к увеличению расхода дорогостоящей ткани и, соответственно, стоимости конечного продукта. Сам процесс прессования тоже требует большего времени, чем в препреговой технологии, поскольку контролируемый нагрев заготовки и ее охлаждение происходят непосредственно в прессовой оснастке. Правда своими последними работами разработчики НИИ Стали показали, что резервы в оптимизации этой технологии есть и они не малые.
Найдены решения по сокращению цикла нагрева и охлаждения заготовки. Не следует забывать еще ряд важных моментов. Поскольку пленочная технология не использует вредных смол, она на порядок экологически чище, что проявляется как в производстве, так и при эксплуатации шлема. Да и для организации крупносерийного производства пленочная технология прогрессивнее препреговой, поскольку позволяет автоматизировать процесс сборки тканево-полимерных пакетов для прессования, тогда как в препреговой технологии эта операция выполняется вручную.
Следуя из вышесказанного, и зарубежная, и отечественная конструкция тканево-полимерного БШ используют в качестве защитной структуры многослойную квазигомогенную композицию на основе высокопрочной арамидной ткани и полимерного термореактивного или термопластичного связующего, которое скрепляет слои ткани по всей толщине структуры и заставляет работать корпус БШ как сплошную высокопрочную упругую оболочку - «полимерную броню».
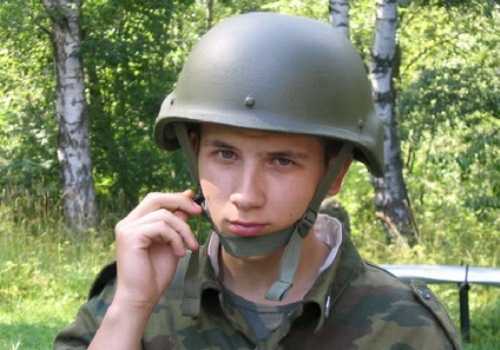
Очень важно отметить тот факт, что сплошная гомогенная оболочка корпуса позволяет оптимально использовать физико-механические свойства материалов структуры, а именно: рассеивать ударную волну, образованную импульсом проникающего высокоскоростного средства поражения, и формируемую ей волну упругой деформации композитного материала, обеспечивая допустимые значения величины динамического прогиба оболочки.
Величина динамического прогиба оболочки корпуса БШ при непробитии защитной структуры является определяющим фактором запреградного контузионного воздействия на голову человека. Поэтому максимально допустимая величина динамического прогиба оболочки всегда определяется в ходе государственных испытаний образцов БШ с помощью рентгеноимпульсной установки в реальном масштабе времени.
Кроме технологии пленочного термопласта, используемой для создания гомогенных сплошных оболочек корпусов БШ, в России была разработана «смешанная» технология, которая включает элементы препреговой технологии в сочетании с «сухими» слоистыми тканевыми арамидными пакетами. При этом наружные тканевые слои защитной структуры пропитываются полимерным термореактивным связующим, а внутренние слои остаются сухими.
Такая структура получила название от своих разработчиков (ЗАО ЦВМ «Армоком») - «дискретно тканевая структура» (ДТС). Начиная с 2000г. российские ВС заказывают тканево-полимерные БШ, изготавливаемые и по пленочной технологии и по технологии ДТС примерно в одинаковых количествах. Только в 2010 - 2011 гг. их было произведено и поставлено в армию около 70 000 шт. Причем, боевые защитные и эксплуатационные характеристики гомогенного и дискретно-тканевого БШ абсолютно одинаковы, цена обоих образцов единая.
В чем же различие? А различие БШ как раз и кроется в составе структуры полимерной защитной композиции, получаемой в результате альтернативных технологических процессов прессования оболочек корпуса. В случае использования пленочного термопласта, как уже было отмечено, получается гомогенная сплошная структура оболочки и процесс взаимодействия средства поражения с такой преградой в общем лежит в плоскости классической теории прочности и упругости материалов.
Корпус БШ, полученный по технологии ДТС, имеет выраженную гетерогенную структуру в состав которой входят две внешние относительно твердые и тонкие оболочки, придающие жесткость всей конструкции, и сухой слоистый пакет арамидной ткани, расположенный между оболочками. Такая структура называется «разнесенной», т.к. более высокоплотные слои находятся на расстоянии друг от друга, а между ними располагается низкоплотный материал.
Разнесенная схема защитной структуры имеет свои преимущества. Например, более эффективное поглощение и рассеивание ударной волны за счет наличия границ раздела между разноплотными слоями материалов композиции. Но это преимущество достигается большей толщиной комбинированного корпуса БШ с ДТС - до 15мм, в то время, как толщина гомогенного пленочного корпуса в самой массивной подтулейной зоне не превышает 8мм.
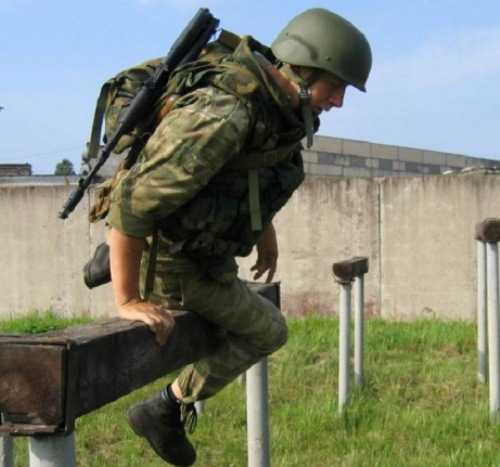
Но кроме этого преимущества больше никаких защитных выгод технология ДТС не дает, не говоря уже об относительно низкой производительности изготовления таких конструкций, прежде всего, за счет большой доли ручного труда, применяемого при сборке тканевого пакета. Вместе с тем, ДТС имеет один существенный недостаток - слишком малую толщину жестко-упругой внутренней оболочки корпуса БШ, задача которой состоит в том, чтобы за счет поглощения энергии упругой деформации сухого тканевого пакета сократить величину динамического прогиба полимерной композиции.
Но т.к. сухой тканевый пакет не связан с тонким упругим подпором из препрега, то и вся энергия упругой деформации пакета приходится на локальную зону поражения тонкой препреговой оболочки, а не распределяется равномерно послойно по всей толщине структуры, как у гомогенного тканево-полимерного корпуса. В этом случае, если в эквивалентных условиях сравнивать значения динамического прогиба двух технологически разных БШ - гомогенного и ДТС, то оказывается что для ДТС величина динамического прогиба больше, чем у гомогенного пленочного термопласта.
Вопрос: «какая из технологий более предпочтительна и прогрессивна?» находится в компетенции Заказчика, который на этапе государственных испытаний детально определил все ТТХ обоих БШ, каждого в отдельности, и допустил в серийное производство оба образца. Пока идет серийное производство тканево-полимерных БШ первого поколения можно было бы и не заострять внимание на технологических аспектах производства различных образцов, тем более, что производство ведется по действующей рабочей конструкторской документации литеры «О1», утвержденной Заказчиком,
Однако, при создании боевой экипировки 2-го поколения, Заказчик выдвинул требование о разработке единой конструкции, а значит и защитной структуры, общевойскового БШ. Становится злободневным «отложенный» Заказчиком вопрос - «Какая структура полимерной защитной композиции отвечает современным требованиям по противоосколочной и противопульной стойкостям в максимальной степени? Какая структура обеспечивает наиболее приемлемые значения запреградного контузионного воздействия?»
Совершенно очевидно, что ответ на этот вопрос Заказчик может получить только после комплексных сравнительных испытаний различных БШ, в том числе и зарубежного производства, в первую очередь медико-биологических исследований результатов динамического воздействия средств поражения на корпус БШ и голову человека. Не ответив на этот вопрос, нельзя будет принять выверенного и обоснованного решения в области боевой экипировки на длительную перспективу.
Источникspec-naz.org
Современные средства бронезащиты российской армии
Автор: Андрей Дмитриев.
Последние несколько лет для Вооруженных сил РФ ознаменовались переходом от участия в миротворческих операциях, в различных конфликтах малой интенсивности к настоящим активным боевым действиям.
Армия, которая долгое время не действовала за рубежом (исключением можно считать разве что краткосрочный конфликт в Южной Осетии), стала проводить крупные войсковые операции как на периферии, так и в дальнем зарубежье – речь идет о действиях российских Вооруженных сил в Крыму, а также об участии в Сирийском конфликте. Внимательный зритель на кадрах современных репортажей сразу заметит разительный контраст между обликом российского солдата сейчас и тем, что мы видели в Чечне и Южной Осетии.
Если раньше российский солдат напоминал скорее наемника (часто экипированного на собственные средства и без какого-либо единообразия), чем бойца регулярной армии, то теперь на видеозаписях, которые приходят из Сирии, мы видим воина, который внешним своим видом практически ничем не уступает своим коллегам из американской армии или Бундесвера.
Мы попробуем разобраться, что представляет собой современное снаряжение, которое находится на вооружении российской армии. Речь на этот раз пойдет о бронежилетах, транспортно-боевых системах (разгрузках) и бронешлемах.
История развития бронежилетов
Первые индивидуальные средства бронезащиты появились в Красной армии – это были стальные нагрудники, по большому счету, не сильно отличавшиеся от кирасы средневекового рыцаря. Такая защита была способна остановить пистолетную пулю и низкоскоростные осколки. Стальные нагрудники активно применялись в специальных штурмовых подразделениях в период Великой Отечественной войны.
После войны работы по созданию индивидуальной бронезащиты были большей частью заморожены. Изучался зарубежный опыт, такой как, например, американская интервенция во Вьетнам, где впервые были массово применены бронежилеты из композитных материалов.
Переломный момент наступил, когда Советская армия начала боевые действия в Афганистане – именно тогда в войска начали массово поступать новые бронежилеты. Разгрузками армия не практически не оснащалась. Приходилось или носить трофейные образцы, или шить самому некое подобие разгрузки из подручных материалов. Все что мог получить от снабженцев рядовой боец – это примитивные брезентовые подсумки. После распада СССР и начала Первой и Второй Чеченских кампаний ситуация в целом изменилась не сильно. Армия была оснащена уже устаревшими на тот момент бронежилетами. Денег на современную экипировку у армии тогда не было.
Наши дни
На данный момент российская армия оснащена в основном двумя моделями общевойсковых бронежилетов. Первый – это 6Б23-1, принятый на вооружение в 2003 году и уже порядком устаревший, а также не очень удобный в эксплуатации. Поставляемые в войска бронежилеты оснащались металлическими бронепластинами, более тяжелыми, чем керамические, а также обеспечивающими худший уровень бронезащиты. Такой бронежилет защищает только по третьему классу в проекции бронепластин. Это в лучшем случае защита от некоторых типов пуль автоматов АК-74 и АКМ. От автоматных пуль с повышенным бронепробитием и пуль снайперских винтовок, таких как СВД, бронежилет 6Б23-1 уже не спасет.
Также этот бронежилет получился не очень удачным в плане эргономики. Например, при стрельбе лежа воротник жилета очень сильно давит на шею солдата. Доходит до того, что в глазах начинает темнеть, и стрельба становится невозможной. Но в то же время отмечается хорошая возможность подогнать бронежилет по фигуре, и он не «болтается» на солдате, как предыдущие образцы. Специальные валики на плечах, которые должны не позволять автоматному ремню сползать в походном положении, сделаны недостаточно большими, вследствие чего автомат на плече приходится постоянно поправлять. Отсутствуют стропы для крепления подсумков УМТБС (универсальной модульной транспортно-боевой системы). Такой недостаток можно компенсировать применением разгрузочной системы, но это увеличивает общий вес снаряжения на солдате (пусть и не очень значительно), а также делает всю конструкцию более громоздкой, что отрицательно сказывается на удобстве ношения.
Однако здесь нужно учитывать, насколько давно 6Б23-1 был принят на вооружение. А также тот факт, что до последнего времени руководство вооруженных сил боевой экипировке уделяло не самое повышенное внимание. Сейчас эти бронежилеты носят в основном военные из частей, находящихся в тылу, и во вспомогательных войсках.
В зоне Сирийского конфликта и в передовых частях российская армия оснащена более современными общевойсковыми бронежилетами 6Б43. Эта модель была принята на снабжение в 2010 году, ее можно заметить в больших количествах в зоне сирийского конфликта, в частях, которые задействованы в миротворческих операциях, и наиболее боеспособных войсках, таких как ВДВ и «Спецназ».
Этот бронежилет во всем превосходит своего предшественника 6Б23-1. Начиная с защиты и заканчивая эргономикой. При меньшем весе, чем у 6Б23-1, он обеспечивает гораздо лучшую бронезащиту. В зоне керамических бронепанелей обеспечивается защита по классу 6А, что означает гарантированную защиту от бронебойно-зажигательных пуль Б-32, выпущенных из винтовки СВД с расстояния 10 метров, а также от снайперских пуль Lapua Magnum, выпущенных с расстояния 300 метров. Бронежилет 6Б43 штатно оборудован климатико-амортизационными подпорами, обеспечивающими лучшую вентиляцию пространства под бронежилетом и снижающими риск получить запреградную травму при попадании вражеской пули в бронежилет.
Также на 6Б43 присутствуют стропы УМТБС, позволяющие устанавливать любые подсумки сразу на бронежилет, не используя дополнительные транспортно-боевые системы. Однако почему-то это не мешает солдатам продолжать носить разгрузки поверх брони, но это уже вопрос к командованию и самим военнослужащим.
Отдельно нужно упомянуть такие вещи, как систему быстрого сброса и эвакуационную петлю. Первая позволяет очень быстро сбросить бронежилет, буквально за несколько секунд, и избавиться от лишней ноши. Достаточно потянуть за специальную петлю возле воротника, и бронежилет сам спадет с бойца. Это особенно важно при форсировании водных преград или при ранении, когда от возможности быстро избавиться от бронежилета может зависеть жизнь солдата.
Эвакуационная петля, как понятно из названия, предназначена для эвакуации раненого бойца в экстренной ситуации, когда нет времени соорудить носилки и нужно максимально быстро покинуть опасный участок. За такую петлю можно перетаскивать раненого бойца даже одной рукой или в положении лежа. На 6Б43 появились специальные упоры для автоматного приклада, чего не было на 6Б23-1, значительно повышающие удобство стрельбы.
6Б43 — один из лучших бронежилетов мира
Бронежилет 6Б43 в полной комплектации.
В целом 6Б43 находится на уровне таких бронежилетов, как, скажем, американский IOTV.
При их сравнении у 6Б43 отмечается лучшая вентиляция, чем у американского аналога, а также более высокое качество бронепанелей. На испытаниях 6Б43 и IOTV бронепанель ESAPI, применяемая в IOTV, потеряла структурную целостность уже после первого выстрела по ней из винтовки СВД. После второго выстрела бронежилет «допустил контузию», третий вовсе его пробил. Бронепанель «Гранит», применяемая в 6Б43, выдержала все три выстрела, не допустив ни пробития, ни контузии. Более того, 6Б43 смог выдержать 10 попаданий без пробития.
Но нужно добавить и «ложку дегтя»: по непонятным причинам 6Б43, поставляемые в войска, не имеют строп системы УМТБС на всей спинной секции, ими обшита только нижняя часть. Теряется возможность повесить на спину подсумок с радиостанцией, как это делается в многих армиях. Возможно, именно поэтому военнослужащие поверх 6Б43 по-прежнему надевают разгрузочный жилет.
В войска идут бронежилеты в базовой комплектации, не имеющие боковых бронепанелей, в то время как снайперы, видя вражеского солдата в бронежилете, чаще всего стараются поразить его в боковую проекцию. Такая экономия может очень дорого обойтись – жизнями российских солдат.
От шлемов витязей к современным средствам бронезащиты
На месте даже самых древних сражений археологи находят защитное снаряжение воинов, в частности, шлемы. Они бывают сделаны из самых разных материалов: кожи, металла и т.п. Но цель, с которой они создавались, была одна: спасти голову от удара холодным оружием.
В древней Руси шлемы делали в основном из металла. Внешний вид у них разнился от эпохи к эпохе, но серьезных изменений в уровне бронезащиты не происходило. После наступления эры огнестрельного оружия шлемы привычной конструкции постепенно вышли из обихода солдата. Они сохранились лишь в некоторых подразделениях, но уже как элемент военной формы, а не средство защиты.
Кардинальные изменения в этой области произошли после начала Первой Мировой войны. С появлением дальнобойной артиллерии и бомбардировочной авиации в статистике потерь личного состава первое место заняли осколочные ранения. При этом ранение в голову чаще всего заканчивалось смертью солдата. Поэтому военные в первую очередь были озабочены защитой головы от осколочных ранений. Разработчики вооружений стран – участниц конфликта по-разному представляли, себе каким должен быть защитный шлем, поэтому первые образцы сильно различались по внешнему виду. Ближе всех по форме к современным оказался шлем, применявшийся в немецкой армии. Российская императорская армия приняла на снабжение шлем, использовавшийся французскими войсками. Позднее она получила на вооружение его улучшенную версию, производившуюся на российских заводах. Такие шлемы могли защитить в лучшем случае от низкоскоростных осколков или ударов камнями.
В период между двумя мировыми войнами боевая экипировка солдат менялась не сильно. В некоторых армиях шлемы, в которых войска принимали участие в Первой Мировой войне, практически без видимых изменений перешли и во Вторую Мировую войну.
В Красной армии в период между двумя мировыми войнами приняли на снабжение шлемы СШ-36 иСШ-40, которые по своему внешнему виду уже гораздо больше напоминали современные средства бронезащиты (и даже до сих пор применяются в некоторых армиях). Различались они формой и подтулейным устройством (что это такое, мы расскажем ниже). Во время Второй Мировой войны большинство армий пришли к форме шлема, напоминавшей сегодняшнюю, близкую по форме к куполу.
Послевоенные разработки, по сути, мало что меняли в защитном снаряжении солдата. Шлемы 1950-х, 1960-х и 1970-х почти не отличались от образцов, появившихся в период Второй Мировой.
Композитный «прорыв»
Прорыв наступил в 1980-х, когда на снабжение армии США поступил арамидный бронешлемPASGT. Он «на голову» превзошел старые стальные шлемы. Если по массе он был примерно равен стальным аналогам, то по бронезащите и эргономике никакого сравнения быть не могло. Такой шлем уже был в состоянии остановить высокоскоростные осколки (основную причину ранений на современном поле боя) и многие пистолетные пули. Изготавливался он путем пропитки множества слоев арамидной ткани полимерными смолами и спрессовыванием их по форме шлема.
Такая технология достаточно недорога в производстве, но вынуждает использовать много слоев арамида, так как под действием смолы он теряет защитные свойства, в итоге это приводит увеличению массы бронешлема.
Современный бронешлем состоит из двух основных деталей: первая – это корпус, та часть, которую мы видим на голове бойца, и вторая – подтулейное устройство или, попросту, подтулейка, которая обеспечивает удобство ношения и гасит все нагрузки, приходящиеся на голову бойца. На старых стальных бронешлемах, таких как СШ-40, эта часть была довольно простой, сделанной с расчетом, что шлем будут носить вместе с армейской шапкой-ушанкой. В холодное время года это позволяло обойтись без специального подшлемника, но в то же время эргономика такого шлема была на очень низком уровне. Из-за отсутствия регулировки по размеру головы СШ-40 постоянно болтался, налезал на глаза, его приходилось все время поправлять или придерживать рукой. Ремешок, удерживающий шлем на голове, крепился только в двух точках и проходил под горлом. Это также делало шлем неустойчивым.
Современные российские бронешлемы
У современных бронешлемов российской армии подтулейное устройство состоит из множества тканевых строп, плотно облегающих голову солдата и не дающих шлему соскальзывать во время движения. Такая система имеет множество регулировок, позволяющих точно подогнать шлем под каждого конкретного бойца. Удерживающий ремешок крепится к шлему в трех или, на некоторых моделях, в четырех точках. В отличие от старых шлемов, он крепится на подбородке, что также повышает удобство ношения.
Первый серийный российский бронешлем из арамидных тканей был принят на снабжение в 2000 году и назывался 6Б7. Изготавливали его по так называемой «пленочной» технологии, когда между слоями ткани поочередно укладывают слои полимерной пленки, затем при нагреве слои пленки спекаются, и заготовка прессуется по форме будущего шлема. Такой способ позволяет обойтись меньшим количеством слоев арамидной ткани, масса бронешлема значительно снижается. В то же время шлем, изготовленный по этой технологии, получается дороже изготовленного аналогично, но при помощи смол.
В дальнейшем на снабжение российской армии были приняты более совершенные шлемы, также изготовленные по этой технологии, – 6Б27 для армии и 6Б28 для воздушно-десантных войск. Они различались формой корпуса: шлем для ВДВ лишен выступающего козырька и оснащен чехлом, полностью закрывающим шлем от набегающего потока воздуха, что положительно сказывается на аэродинамике во время десантирования.
Еще одна технология, применяемая для производства бронешлемов, поставляемых в российскую армию, носит название «дискретно-тканевая». Шлемы, изготовленные таким способом, несколько схожи по конструкции с теми, которые производятся при помощи смолы. Основное отличие заключается в том, что между двумя слоями, пропитанными смолой, оставлен один сухой слой. Две тонкие оболочки обеспечивают жесткость всей конструкции, а расположенный меду ними пакет арамидной ткани гасит нагрузки. Такая схема более эффективно поглощает энергию удара, но в то же время делает всю конструкцию более хрупкой. При изготовлении такого бронешлема применяется много ручного труда, что делает его менее технологичным.
По этой технологии производится последняя разработка, принятая на снабжение ВС РФ. Она носит индекс 6Б47 и обеспечивает защиту от высокоскоростных осколков и пистолетных пуль, при этом имея массу примерно в 1 килограмм. Это один из лучших показателей в мире, что признают и зарубежные специалисты. На шлеме имеются штатные устройства для крепления приборов ночного видения, фонарей. Бойцов в таких шлемах мы можем видеть в районе Сирийского конфликта.
В настоящее время на снабжении российской армии стоят шлемы, изготовленные как по «пленочной», так и по дискретно-тканевой технологии. Какая конструкция окажется более удачной – покажет только время.
dfnc.ru
Современные бронешлемы - защитные структуры и технологии изготовления - Армия России - Россия - Библиотека Стахановского новостного портала
Индивидуальная защитная экипировка бойца на поле боя используется уже не одну тысячу лет и ее компоненты хорошо известны историкам и археологам, изучены до малейших подробностей. Испокон веку важнейшей частью боевой защиты считается бронешлем (БШ). Конструкция и геометрическая форма БШ менялась со временем в зависимости от постоянного совершенствования оружия и средств поражения, от которых надо было защитить человека. Однако, материал, из которого изготавливали корпус БШ - его главную конструктивную часть, практически не менялся на протяжении многих веков. Этим материалом был гомогенный тонкий листовой металл - сначала медь и бронза, потом железо и сталь. До начала 80-х годов XX века только стальные БШ использовались во всех армиях мира. В этой статье специально для ИА "Оружие России" сотрудники НИИ "Стали" Д.Купрюнин, А.Егоров и Е.Чистяков рассматривают некоторые аспекты, относящиеся к современным материалам и конструкциям БШ.
Главнейшая задача БШ, сформулированная военными ведущих мировых держав, состоит в защите головы бойца от самого массового на поле боя фактора поражения - осколков естественного дробления осколочно-фугасных снарядов, мин и гранат, а также защите черепа от ударных нагрузок.
В середине XX века, когда были проанализированы результаты 1-й и 2-й мировых войн и последующих локальных конфликтов (в Корее и Вьетнаме), стало очевидно, что стальной гомогенный БШ не может обеспечить защиту головы бойца от наиболее массовой части спектра осколочного потока поражения на современном поле боя. Уровень его противоосколочной стойкости (ПОС) был весьма низок и не превышал V50%= 300-350 м/с для осколка массой 1г (50%-ная вероятность непробития корпуса БШ).
Надо сказать, что сделать защиту с более высокой ПОС можно только за счет увеличения толщины корпуса БШ, что сразу "приведет" к существенному увеличению носимой на голове массы. Так, например, чтобы поднять ПОС стального БШ с V50%= 300м/с до V5o%= 600 м/с надо почти удвоить толщину корпуса с 1,6мм до 2,5мм, что при физической плотности стали рст=7,85 г/см3 приведет к увеличению массы корпуса БШ с 1500г до 2350г.
Это недопустимо, т.к. существуют медико-технические ограничения по величине допустимой носимой массы БШ, которые предписывают максимальный предел для общевойскового БШ в 1600г. Такое ограничение обусловлено тем, что опытно-экспериментальным путем медиками была определена возможность получения тяжелой травмы шейного участка позвоночника человеком при превышении носимой распределенной массы БШ на голове сверх 1600г.
Таким образом, на рубеже 60-х - 70-х г.г. XX века появилась задача создания низкоплотных полимерных материалов, обладающих соизмеримым с высокопрочной сталью пределом прочности, которые пришли бы на замену стальному листовому прокату в производство БШ и позволили бы значительно повысить ПОС корпуса без увеличения его массы.
Кроме того, полимерные материалы, ввиду своих физико-механических свойств, лучше поглощают и рассеивают ударно-волновую энергию взаимодействия средства поражения с защитной структурой преграды, чем гомогенная высокоуглеродистая сталь.
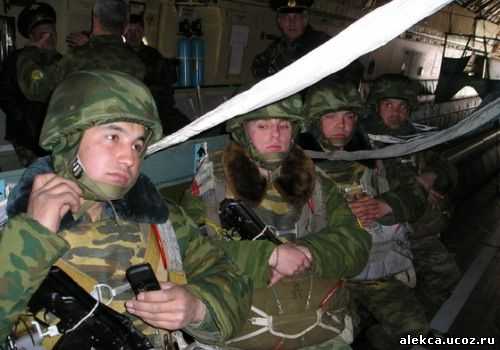
Такой материал был впервые разработан американской фирмой «Dupont» и был назван «параарамидным волокном», имевшим предел прочности такой же, как у конструкционной стали, а физическую плотность рар.=1,43 г/см3, что более чем в 5 раз легче стали. Из параарамидного волокна сделали нить линейной плотности 110 текс. (масса нити в граммах на 1000м длины), которая получила торговую марку «Kevlar®29», и соткали полотно удельной массой 255 г/м2.
Из этой ткани была изготовлена квазигомогенная многослойная тканево-полимерная структура, которая в эквивалентной массе с гомогенной монолитной сталью показала вдвое более высокую ПОС и существенно меньший динамический прогиб композиции при взаимодействии с имитатором стандартного осколка и пистолетной пулей 9мм калибра. Первый в мире тканево-полимерный шлем появился в США.
Его разработала Натикская научно-исследовательская лаборатория Армии США в конце 1970-х годов. В начале 1980-х годов он был принят на вооружение сухопутных войск. Шлем получил название Personnel Armor System, Ground Troops (PASGT). Он был выполнен из ткани на основе волокна Kevlar®29 и связующего - фенольной или PVB смолы.
Масса БШ составляла 1,4 (3,1 фунта) -1,9 кг (4,2 фунта)} имел 5 типоразмеров - XS, S, M, L, XL. Уровень ПОС шлема определялся военным стандартом MIL-STD-662E, полицейским NIJ 0106 и составлял V50% = 600м/с по стандартному осколку STANAG 2920, что примерно соответствует уровню в V50%=570...580 м/с по стальному шарику массой 1,03 г, которым испытываются все российские шлемы. Противоударные характеристики регламентированы стандартом MIL-h54099A.
Технология изготовления этих шлемов достаточно проста. Ткань, пропитанную полимерным связующим, проще говоря, смолой, укладывают в несколько слоев в форму. Полученную заготовку прессуют при определенной температуре, связующее полимеризуется, твердеет. От прессованной оболочки обрезают облой, устанавливают подтулейное устройство - шлем готов,
Так как ткань, пропитанную смолой; называют «препрегом», то и технология изготовления шлемов получила название «препреговой». Основное преимущество этой технологии - простота и малая зависимость конечного результата от точности соблюдения режимов прессования. Поэтому достаточно быстро шлемы, аналогичные PASGT, начали выпускаться во многих странах.
За 30 лет произведено несколько миллионов штук шлемов типа PASGT, он принят в качестве основного в НАТО и до сих пор используется Армией США. В армиях многих стран по всему миру используется или этот шлем или его аналоги. Количество фирм-производителей шлемов типа PASGT перевалило за несколько сотен. Соответственно и разброс характеристик этих шлемов, как по массовым, так и по защитным характеристикам достаточно велик.
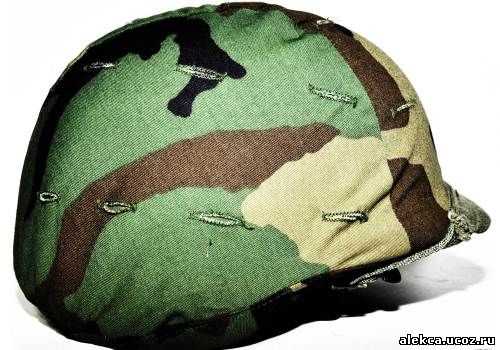
Хотя в целом шлем удовлетворял требованиям военных, работы по его совершенствованию были начаты уже в конце 90-х годов. Работы эти были инициированы началом реализации во многих странах мира программ по оснащению бойца будущего столетия. Этими программами боец и его экипировка рассматриваются как единая система, которая, взаимодействуя с другими системами, должна максимально эффективно выполнять боевую задачу.
Средства защиты, и шлем в частности, принимаются программой как элемент, который кроме выполнения защитных функций должен комплексироваться с другими элементами системы. Практически все программы «Боец будущего» рассматривают шлем как платформу для установки приборов ночного видения, связи, навигации, дисплеев для самоконтроля и информационных функций, что неминуемо приводит к увеличению массы, нагружающей голову.
Поэтому еще в 1996 году МО США была выдвинута двухгодичная программа SEP (Soldier Enhancement Program - Программа повышения боевых возможностей солдата), в рамках которой должна была быть разработана и испытана каска с более легкой основой. В качестве цели была поставлена задача снизить вес шлема на 25%.
Однако реализовать эти цели зарубежным разработчикам удается с большим трудом. Основная причина кроется как раз в созданной и эксплуатируемой ими технологии. Уже давно стало ясно, что баллистическая ткань наиболее эффективно работает, когда ее отдельные нити имеют возможность при упругой деформации растягиваться, достигая предела текучести, что происходит при максимальных нагрузках на материал.
Ткань сама по себе уже ограничивает эластичность нитей и от типа плетения стойкость ткани может существенно меняться. Если же ткань пропитать смачивающим клеевым составом и превратить в жесткий композит, то баллистические характеристики такого композита будут хуже, чем у эквивалентного по массе ничем не связанного тканевого пакета.
Тем не менее, применяя новые, более эффективные, чем Kevlar®29 материалы, зарубежным разработчикам удалось на 10-15% снизить и массу шлема и поднять его ПОС. Так, применение нового усовершенствованного арамидного волокна «Kevlar® KM2» и изготовление из него нитей более низкой линейной плотности (44текс, 67текс.) позволило снизить вес шлема на 8-10%.
Дальнейшие исследования по снижению веса привели к разработке и принятию на вооружение армии США в 2002 г новой, также арамидной, каски АСН (Advanced Combat Helmet), имеющей ещё меньший вес. Правда, снижение веса обеспечивалось, в основном, уменьшением на 8 % площади защиты, но разработчикам удалось увеличить на 6% ее ПОС.
Усиленно работает над проблемой снижения массы шлема и бывший разработчик шлема PASGT- исследовательская лаборатория NATICK. Так, в настоящее время она исследует два новых материала, которые могут решить проблему снижения веса. Один из них - известный материал «Zyion». Используя этот материал, фирме удалось получить шлем массой всего в 800 г. (1,79 фунт).
Однако, этот материал оказался нестойким к воздействию солнечного света, воды и потому непригодным для использования в шлемах. Сейчас фирма исследует новый материал на основе волокна М5, разработанного фирмой Magellan Systems Int. Расчеты показывают, что при том же уровне защиты использование материала М5 позволит уменьшить массу шлема на 35 %. Однако, пока американский солдат воюет в шлеме, масса которого не менее 1,3-1,5 кг, а ПОС не превышает 680-700 м/с по STANAG-2920.
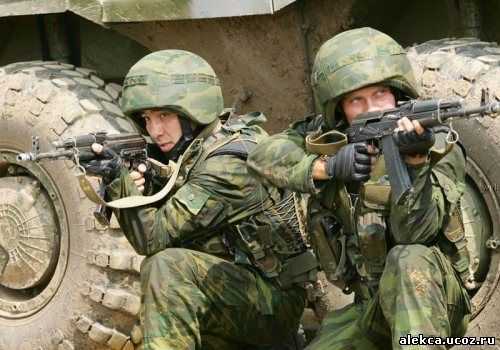
Россия значительно позже многих зарубежных стран начала думать о замене стальной каски CLU-68 на тканево-полимерную, хотя работы по созданию такой каски начались в НИИ Стали в инициативном порядке еще с середины 80-х годов. Разработчики института начали осваивать принципиально другую технологию -технологию термопластичного прессования квазигомогенных многослойных пленочных структур, или - как ее часто сейчас называют - «пленочную» технологию.
Суть ее проста - слои баллистической ткани прокладываются тонкой термопластичной пленкой. Затем пакет закладывается в прессформу, нагревается, прессуется и охлаждается. Пленка расплавляется и соединяет слои ткани. После охлаждения получается жесткая гомогенная оболочка корпуса шлема. По расчетам разработчиков пленка, размягчаясь, не смачивает нити ткани, оставляя им практически полную свободу предельной упругой деформации, а значит, стойкость такой композиции должна быть выше, чем у эквивалентного по массе препрега.
Практика показала, что расчет был верен. Правда, чтобы прийти к желаемому результату институту потребовалось почти 10 лет. Именно столько шла отработка промышленной высокопроизводительной технологии получения шлемов требуемого качества. Зато у разработчиков появилось широкое поле для оптимизации композиции. Варьируя набором тканей в лицевых и тыльных слоях, меняя толщину и материал пленочного связующего можно было подобрать наиболее оптимальный вариант для заданных условий.
В 1999 году первый серийный шлем, произведенный в НИИ Стали под индексом «6Б7», поступил в вооруженные силы российской армии. По своим характеристикам он сразу же превзошел свой зарубежный аналог: масса - не более 1,3-1,35 кг, противоосколочная стойкость -560 м/с, что соответствует 600-610 м/с по STANAG.
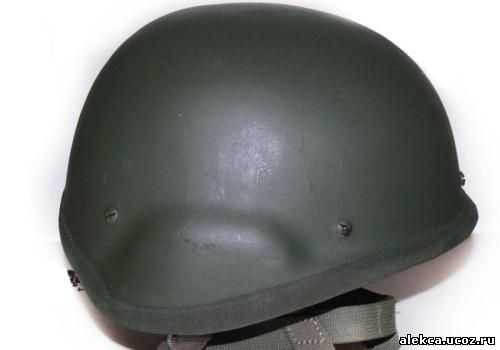
К 2005 году НИИ стали разработал и сдал на вооружение еще 3 модели шлемов - 6Б26, 6Б27 и 6Б28. Все они являлись и до сих пор являются рекордсменами по массе и стойкости. Оптимизируя состав пакета, НИИ Стали удалось создать шлем массой не более 1,1 кг с ПОС выше 700 м/с (по STANAG - 730-740 м/с), причем не в опытном экземпляре, а в серийном производстве. Это прототип конструкции общевойскового БШ 2-го поколения.
Естественно, столь высокие характеристики шлема были достигнуты соответственной ценой. Так, жесткие требования предъявляются к качеству используемой баллистической ткани, малейшее отклонение от паспортных характеристик отправляет ткань в брак. Технология допускает использование в пакетах только цельных кусков, тогда как в препреговой технологии можно использовать пакеты, набранные из кусков баллистической ткани.
Это приводит к увеличению расхода дорогостоящей ткани и, соответственно, стоимости конечного продукта. Сам процесс прессования тоже требует большего времени, чем в препреговой технологии, поскольку контролируемый нагрев заготовки и ее охлаждение происходят непосредственно в прессовой оснастке. Правда своими последними работами разработчики НИИ Стали показали, что резервы в оптимизации этой технологии есть и они не малые.
Найдены решения по сокращению цикла нагрева и охлаждения заготовки. Не следует забывать еще ряд важных моментов. Поскольку пленочная технология не использует вредных смол, она на порядок экологически чище, что проявляется как в производстве, так и при эксплуатации шлема. Да и для организации крупносерийного производства пленочная технология прогрессивнее препреговой, поскольку позволяет автоматизировать процесс сборки тканево-полимерных пакетов для прессования, тогда как в препреговой технологии эта операция выполняется вручную.
Следуя из вышесказанного, и зарубежная, и отечественная конструкция тканево-полимерного БШ используют в качестве защитной структуры многослойную квазигомогенную композицию на основе высокопрочной арамидной ткани и полимерного термореактивного или термопластичного связующего, которое скрепляет слои ткани по всей толщине структуры и заставляет работать корпус БШ как сплошную высокопрочную упругую оболочку - «полимерную броню».
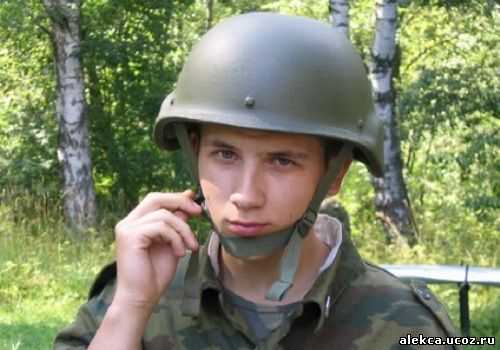
Очень важно отметить тот факт, что сплошная гомогенная оболочка корпуса позволяет оптимально использовать физико-механические свойства материалов структуры, а именно: рассеивать ударную волну, образованную импульсом проникающего высокоскоростного средства поражения, и формируемую ей волну упругой деформации композитного материала, обеспечивая допустимые значения величины динамического прогиба оболочки.
Величина динамического прогиба оболочки корпуса БШ при непробитии защитной структуры является определяющим фактором запреградного контузионного воздействия на голову человека. Поэтому максимально допустимая величина динамического прогиба оболочки всегда определяется в ходе государственных испытаний образцов БШ с помощью рентгеноимпульсной установки в реальном масштабе времени.
Кроме технологии пленочного термопласта, используемой для создания гомогенных сплошных оболочек корпусов БШ, в России была разработана «смешанная» технология, которая включает элементы препреговой технологии в сочетании с «сухими» слоистыми тканевыми арамидными пакетами. При этом наружные тканевые слои защитной структуры пропитываются полимерным термореактивным связующим, а внутренние слои остаются сухими.
Такая структура получила название от своих разработчиков (ЗАО ЦВМ «Армоком») - «дискретно тканевая структура» (ДТС). Начиная с 2000г. российские ВС заказывают тканево-полимерные БШ, изготавливаемые и по пленочной технологии и по технологии ДТС примерно в одинаковых количествах. Только в 2010 - 2011 гг. их было произведено и поставлено в армию около 70 000 шт. Причем, боевые защитные и эксплуатационные характеристики гомогенного и дискретно-тканевого БШ абсолютно одинаковы, цена обоих образцов единая.
В чем же различие? А различие БШ как раз и кроется в составе структуры полимерной защитной композиции, получаемой в результате альтернативных технологических процессов прессования оболочек корпуса. В случае использования пленочного термопласта, как уже было отмечено, получается гомогенная сплошная структура оболочки и процесс взаимодействия средства поражения с такой преградой в общем лежит в плоскости классической теории прочности и упругости материалов.
Корпус БШ, полученный по технологии ДТС, имеет выраженную гетерогенную структуру в состав которой входят две внешние относительно твердые и тонкие оболочки, придающие жесткость всей конструкции, и сухой слоистый пакет арамидной ткани, расположенный между оболочками. Такая структура называется «разнесенной», т.к. более высокоплотные слои находятся на расстоянии друг от друга, а между ними располагается низкоплотный материал.
Разнесенная схема защитной структуры имеет свои преимущества. Например, более эффективное поглощение и рассеивание ударной волны за счет наличия границ раздела между разноплотными слоями материалов композиции. Но это преимущество достигается большей толщиной комбинированного корпуса БШ с ДТС - до 15мм, в то время, как толщина гомогенного пленочного корпуса в самой массивной подтулейной зоне не превышает 8мм.
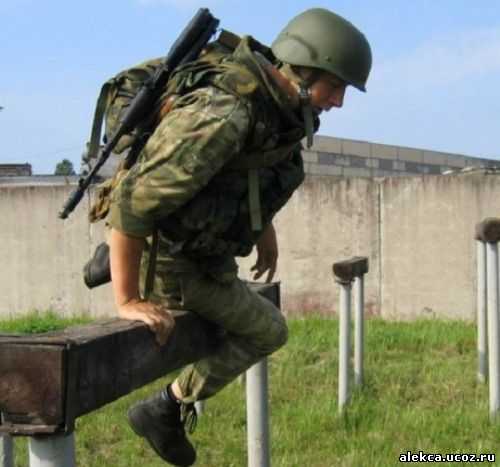
Но кроме этого преимущества больше никаких защитных выгод технология ДТС не дает, не говоря уже об относительно низкой производительности изготовления таких конструкций, прежде всего, за счет большой доли ручного труда, применяемого при сборке тканевого пакета. Вместе с тем, ДТС имеет один существенный недостаток - слишком малую толщину жестко-упругой внутренней оболочки корпуса БШ, задача которой состоит в том, чтобы за счет поглощения энергии упругой деформации сухого тканевого пакета сократить величину динамического прогиба полимерной композиции.
Но т.к. сухой тканевый пакет не связан с тонким упругим подпором из препрега, то и вся энергия упругой деформации пакета приходится на локальную зону поражения тонкой препреговой оболочки, а не распределяется равномерно послойно по всей толщине структуры, как у гомогенного тканево-полимерного корпуса. В этом случае, если в эквивалентных условиях сравнивать значения динамического прогиба двух технологически разных БШ - гомогенного и ДТС, то оказывается что для ДТС величина динамического прогиба больше, чем у гомогенного пленочного термопласта.
Вопрос: «какая из технологий более предпочтительна и прогрессивна?» находится в компетенции Заказчика, который на этапе государственных испытаний детально определил все ТТХ обоих БШ, каждого в отдельности, и допустил в серийное производство оба образца. Пока идет серийное производство тканево-полимерных БШ первого поколения можно было бы и не заострять внимание на технологических аспектах производства различных образцов, тем более, что производство ведется по действующей рабочей конструкторской документации литеры «О1», утвержденной Заказчиком,
Однако, при создании боевой экипировки 2-го поколения, Заказчик выдвинул требование о разработке единой конструкции, а значит и защитной структуры, общевойскового БШ. Становится злободневным «отложенный» Заказчиком вопрос - «Какая структура полимерной защитной композиции отвечает современным требованиям по противоосколочной и противопульной стойкостям в максимальной степени? Какая структура обеспечивает наиболее приемлемые значения запреградного контузионного воздействия?»
Совершенно очевидно, что ответ на этот вопрос Заказчик может получить только после комплексных сравнительных испытаний различных БШ, в том числе и зарубежного производства, в первую очередь медико-биологических исследований результатов динамического воздействия средств поражения на корпус БШ и голову человека. Не ответив на этот вопрос, нельзя будет принять выверенного и обоснованного решения в области боевой экипировки на длительную перспективу.
Не менее интересный материал о бронешлемах можно прочитать здесь.
МОСКВА , 10 марта 2012 , ОРУЖИЕ РОССИИ , Д.Г.Купрюнин, А.И.Егоров, Е.Н.Чистяков
alekca.ucoz.ru